Belt friction heat is a critical phenomenon that occurs in various mechanical systems, particularly in applications involving conveyor belts, drive belts, and other similar components. When two surfaces come into contact and move against each other, friction is generated, leading to the production of heat. This heat can significantly impact the performance and longevity of the belt and the machinery it operates within.
Understanding the mechanics of belt friction heat is essential for engineers and operators alike, as it can influence everything from efficiency to safety. The generation of heat due to friction is a natural consequence of the laws of physics. As belts operate under load, the friction between the belt and pulleys or other surfaces increases, leading to a rise in temperature.
This heat can cause various issues, including material degradation, reduced efficiency, and even failure of the belt system. Therefore, a comprehensive understanding of how belt friction heat is generated and dissipated is crucial for optimizing performance and ensuring the reliability of mechanical systems.
Key Takeaways
- Belt friction heat is generated when two surfaces rub against each other during the operation of a belt drive system.
- Factors affecting belt friction heat include belt material, tension, speed, and environmental conditions.
- Managing belt friction heat is important to prevent premature wear, reduce energy loss, and increase the lifespan of the belt drive system.
- Techniques for reducing belt friction heat include proper tensioning, choosing the right belt material, and implementing lubrication and cooling methods.
- Proper belt tensioning is crucial for reducing heat generation and ensuring optimal performance of the belt drive system.
Factors Affecting Belt Friction Heat
Several factors contribute to the generation of belt friction heat, each playing a significant role in determining the overall thermal performance of a belt system. One of the primary factors is the material composition of the belt itself. Different materials exhibit varying coefficients of friction, which directly influence the amount of heat generated during operation.
For instance, rubber belts may produce more heat than polyurethane belts under similar conditions due to their inherent properties. Another critical factor is the load applied to the belt. The greater the load, the more friction is generated, leading to increased heat production.
Additionally, environmental conditions such as temperature and humidity can also affect friction levels. High temperatures can exacerbate heat generation, while humidity may alter the friction characteristics of certain materials. Understanding these factors is essential for engineers to design systems that minimize heat generation and enhance overall efficiency.
Importance of Managing Belt Friction Heat
Managing belt friction heat is vital for several reasons, primarily related to performance, safety, and cost-effectiveness. Excessive heat can lead to premature wear and tear on belts, resulting in frequent replacements and increased maintenance costs. By effectively managing heat levels, organizations can extend the lifespan of their belts and reduce downtime associated with repairs or replacements.
Moreover, controlling belt friction heat is crucial for maintaining operational safety. Overheating can lead to catastrophic failures, posing risks not only to machinery but also to personnel working in proximity to these systems. By implementing effective heat management strategies, companies can create safer working environments while ensuring that their machinery operates at optimal efficiency.
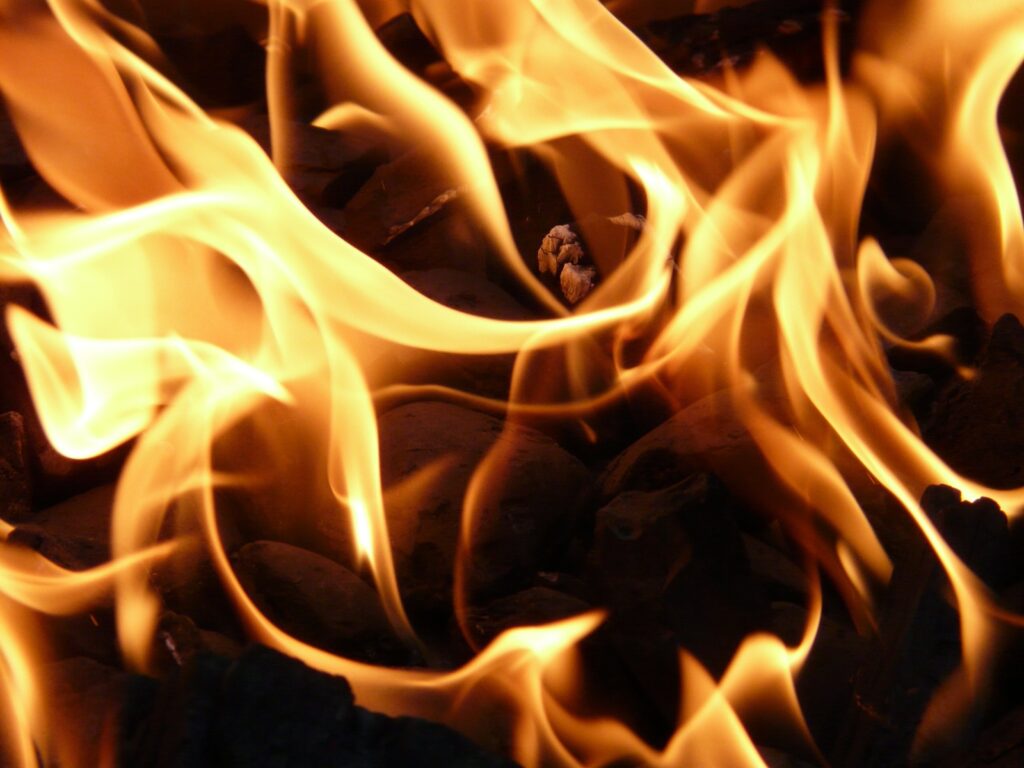
Techniques for Reducing Belt Friction Heat
There are several techniques that can be employed to reduce belt friction heat effectively. One common approach is to optimize the design of the belt system itself. This includes selecting appropriate pulleys and ensuring that they are aligned correctly to minimize unnecessary friction.
Additionally, using belts with lower coefficients of friction can significantly reduce heat generation during operation. Another effective technique involves adjusting operational parameters such as speed and load. By operating within recommended limits, it is possible to minimize the amount of friction generated.
Furthermore, implementing regular maintenance schedules can help identify potential issues before they escalate into significant problems, thereby reducing the likelihood of excessive heat generation.
Choosing the Right Belt Material for Heat Management
Selecting the appropriate belt material is a fundamental aspect of managing belt friction heat effectively. Different materials possess unique properties that influence their performance under varying conditions. For instance, materials like neoprene or polyurethane may offer better resistance to heat compared to traditional rubber belts.
Understanding these material properties allows engineers to make informed decisions when designing belt systems. In addition to thermal resistance, other factors such as flexibility, durability, and cost must also be considered when choosing belt materials. A well-rounded approach ensures that the selected material not only manages heat effectively but also meets other operational requirements.
By carefully evaluating these aspects, organizations can enhance their overall efficiency while minimizing issues related to belt friction heat.
Proper Belt Tensioning for Heat Reduction
Proper belt tensioning is another critical factor in managing belt friction heat. An incorrectly tensioned belt can lead to increased friction between the belt and pulleys, resulting in higher temperatures during operation. Ensuring that belts are neither too tight nor too loose is essential for optimal performance.
A well-tensioned belt operates smoothly, reducing unnecessary wear and tear while minimizing heat generation. Regularly checking and adjusting belt tension should be part of a comprehensive maintenance program. This proactive approach helps identify any deviations from optimal tension levels before they lead to significant issues.
By maintaining proper tensioning practices, organizations can effectively manage belt friction heat and enhance the overall reliability of their systems.
Lubrication and Cooling Methods for Belt Friction Heat
Incorporating lubrication and cooling methods into belt systems can significantly mitigate the effects of friction heat. Lubricants reduce friction between moving surfaces, thereby lowering the amount of heat generated during operation. Selecting the right type of lubricant is crucial; it must be compatible with both the belt material and the operating environment to ensure effectiveness.
Cooling methods can also play a vital role in managing heat levels within a belt system. This may involve using air or liquid cooling systems to dissipate excess heat generated during operation. Implementing these cooling strategies not only helps maintain optimal operating temperatures but also enhances overall system efficiency by preventing overheating-related failures.
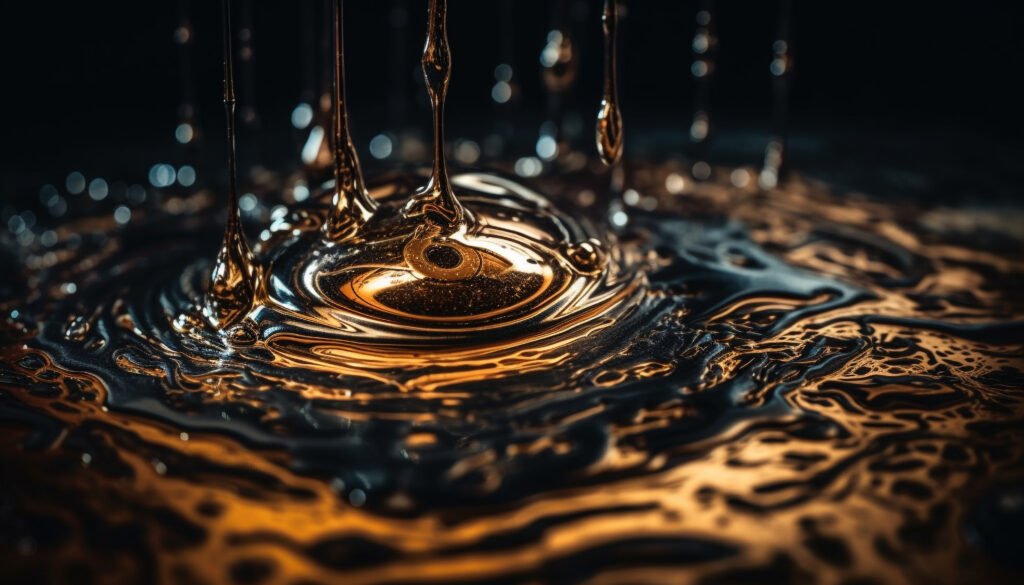
Monitoring and Maintenance for Heat Management
Continuous monitoring and maintenance are essential components of an effective strategy for managing belt friction heat. Utilizing temperature sensors and monitoring systems allows operators to track heat levels in real-time, enabling them to respond quickly to any anomalies that may arise. This proactive approach helps prevent overheating and extends the lifespan of both belts and associated machinery.
Regular maintenance practices should include inspections for wear and tear, alignment checks, and tension adjustments. By adhering to a structured maintenance schedule, organizations can identify potential issues early on and implement corrective measures before they escalate into more significant problems. This commitment to monitoring and maintenance ultimately leads to improved performance and reduced costs associated with downtime and repairs.
Training and Education for Personnel on Heat Management
Investing in training and education for personnel involved in operating and maintaining belt systems is crucial for effective heat management. Providing employees with knowledge about the causes and consequences of belt friction heat empowers them to take proactive measures in their daily operations. Training programs should cover topics such as proper tensioning techniques, lubrication practices, and monitoring strategies.
Furthermore, fostering a culture of safety and awareness around heat management can lead to improved operational practices across the board. When personnel understand the importance of managing belt friction heat, they are more likely to adhere to best practices and contribute positively to overall system performance.
Case Studies and Best Practices for Managing Belt Friction Heat
Examining case studies and best practices from various industries can provide valuable insights into effective strategies for managing belt friction heat. For instance, companies that have successfully implemented advanced monitoring systems have reported significant reductions in overheating incidents and associated costs. These case studies highlight the importance of investing in technology that enables real-time tracking of temperature levels.
Additionally, organizations that prioritize employee training have seen improvements in operational efficiency as personnel become more adept at identifying potential issues related to heat management. By learning from these examples, other companies can adopt similar practices tailored to their specific needs, ultimately enhancing their ability to manage belt friction heat effectively.
Future Trends in Belt Friction Heat Management
As technology continues to evolve, new trends are emerging in the field of belt friction heat management. Innovations such as smart sensors and predictive analytics are paving the way for more sophisticated monitoring systems that can anticipate potential overheating issues before they occur. These advancements enable organizations to take a proactive approach to maintenance, reducing downtime and improving overall efficiency.
Moreover, ongoing research into advanced materials may lead to the development of belts with enhanced thermal properties that can withstand higher temperatures without compromising performance. As industries continue to prioritize sustainability and efficiency, these trends will play a crucial role in shaping the future landscape of belt friction heat management. In conclusion, understanding and managing belt friction heat is essential for optimizing performance in various mechanical systems.
By considering factors such as material selection, proper tensioning, lubrication methods, and continuous monitoring, organizations can effectively mitigate the risks associated with excessive heat generation. Investing in training and adopting best practices will further enhance operational efficiency while ensuring safety within industrial environments. As technology advances, future trends will continue to shape how industries approach this critical aspect of mechanical engineering.
FAQs
What is belt friction heat?
Belt friction heat refers to the heat generated when two surfaces, such as a belt and a pulley, rub against each other during operation. This heat is a result of the friction between the surfaces and can lead to increased wear and reduced efficiency of the system.
How does belt friction heat affect industrial equipment?
Excessive belt friction heat can lead to premature wear and failure of the belt and pulley system. It can also cause a decrease in the overall efficiency of the equipment and may result in increased maintenance and replacement costs.
What are the factors that contribute to belt friction heat?
Factors that contribute to belt friction heat include the tension of the belt, the speed of the belt, the material and surface finish of the belt and pulley, and the environmental conditions in which the equipment operates.
How can belt friction heat be managed?
Belt friction heat can be managed by ensuring proper belt tension, using suitable lubricants, selecting the right belt and pulley materials, and implementing effective cooling methods such as ventilation or cooling fans.
Why is it important to understand and manage belt friction heat?
Understanding and managing belt friction heat is important to ensure the longevity and efficiency of industrial equipment. By controlling the heat generated from friction, companies can reduce maintenance costs, improve equipment reliability, and enhance overall operational performance.
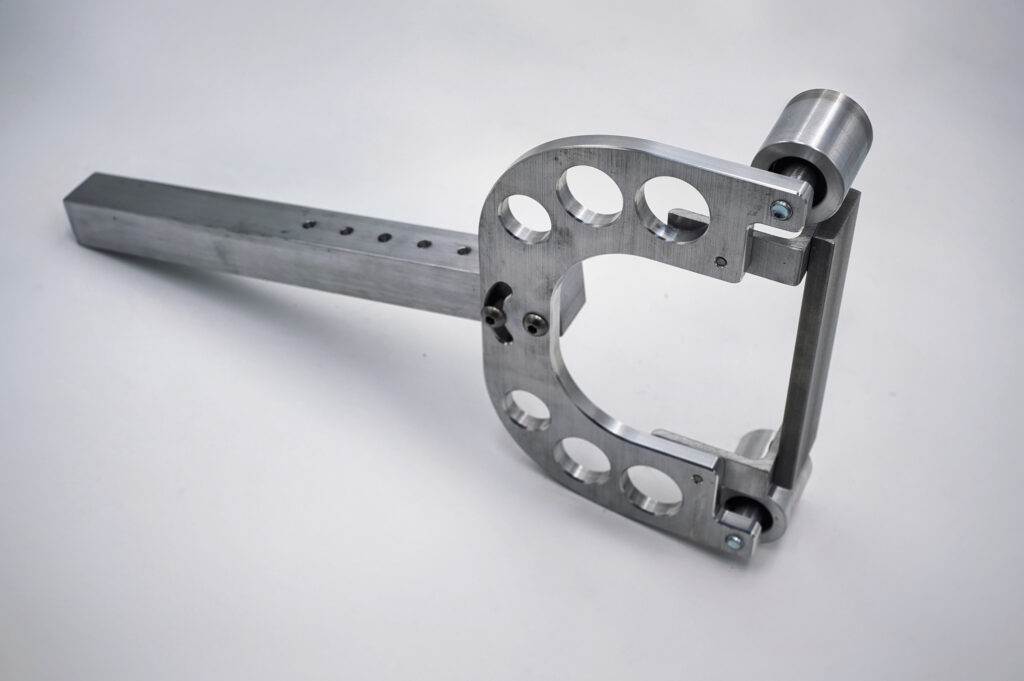