Compact CNC aluminum grinders have emerged as essential tools in various manufacturing and fabrication environments. Their primary advantage lies in their ability to deliver high precision and efficiency while occupying minimal space. This is particularly beneficial for small workshops or production facilities where every square foot counts.
The compact design allows for easy integration into existing setups without the need for extensive reconfiguration of the workspace. Moreover, these grinders are engineered to handle a variety of materials, making them versatile tools for different applications. Another significant benefit of compact CNC aluminum grinders is their user-friendly operation.
Many models come equipped with intuitive controls and interfaces that simplify the grinding process, allowing operators to achieve optimal results with minimal training. This ease of use not only enhances productivity but also reduces the likelihood of errors during operation. Additionally, the advanced technology incorporated into these machines often results in lower energy consumption, contributing to cost savings over time.
As industries increasingly prioritize sustainability, the energy efficiency of compact CNC aluminum grinders becomes an attractive feature.
Key Takeaways
- Compact CNC aluminum grinders offer portability and convenience for on-the-go grinding needs.
- The space-saving design of compact CNC aluminum grinders makes them ideal for small workspaces or travel.
- Compact CNC aluminum grinders maximize efficiency with their precise and powerful grinding capabilities.
- CNC aluminum grinders are known for their precision and durability, ensuring long-lasting performance.
- When choosing a compact CNC aluminum grinder, consider the size and features that best fit your workspace and production needs.
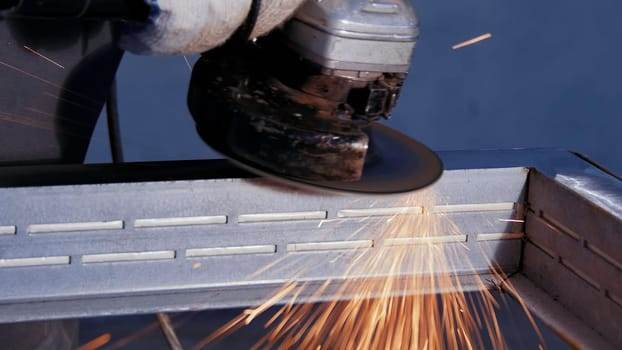
Exploring the Space-Saving Design of Compact CNC Aluminum Grinders
The design of compact CNC aluminum grinders is a testament to modern engineering, focusing on maximizing functionality while minimizing footprint. These machines are often built with a streamlined structure that allows them to fit into tight spaces without sacrificing performance. The thoughtful arrangement of components ensures that operators can access all necessary parts without difficulty, promoting a more efficient workflow.
This space-saving design is particularly advantageous in environments where multiple machines are in operation, as it allows for better organization and movement within the workspace. Furthermore, the compact nature of these grinders does not compromise their capabilities. Many models are equipped with powerful motors and advanced grinding technology that enable them to perform complex tasks with ease.
The integration of high-quality materials in their construction ensures that they remain robust and reliable despite their smaller size. This combination of compactness and capability makes them an ideal choice for businesses looking to optimize their production processes without requiring extensive floor space.
Maximizing Efficiency with Compact CNC Aluminum Grinders
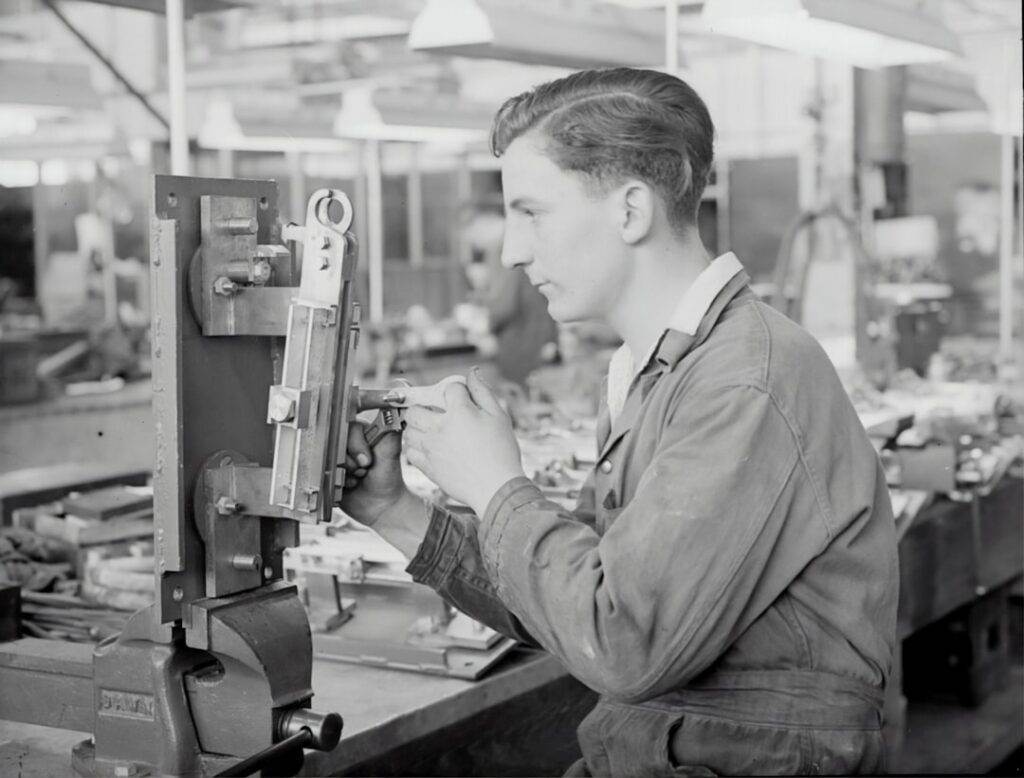
Efficiency is a critical factor in any manufacturing process, and compact CNC aluminum grinders excel in this regard. Their design allows for rapid setup and changeover, enabling operators to switch between different tasks with minimal downtime. This agility is essential in today’s fast-paced production environments, where meeting tight deadlines is often a priority.
The ability to quickly adapt to varying project requirements ensures that businesses can maintain a competitive edge. Moreover, these grinders often feature advanced programming capabilities that allow for precise control over grinding parameters. Operators can easily input specifications for different materials and desired finishes, ensuring consistent quality across batches.
This level of precision not only enhances the final product but also reduces waste, as less material is discarded due to errors or inconsistencies. By maximizing efficiency through both design and technology, compact CNC aluminum grinders contribute significantly to overall productivity in manufacturing settings.
The Precision and Durability of CNC Aluminum Grinders
Feature | Specification |
---|---|
Material | CNC Aluminum |
Precision | High precision grinding |
Durability | Long-lasting and sturdy |
Size Options | Available in various sizes |
Performance | Consistent and reliable |
Precision is a hallmark of CNC technology, and compact aluminum grinders are no exception. These machines are designed to deliver exceptional accuracy, which is crucial for applications requiring tight tolerances. The integration of computer numerical control allows for intricate designs and complex geometries to be achieved with ease.
This level of precision ensures that components fit together seamlessly, reducing the need for additional machining processes and saving time and resources. Durability is another key feature of compact CNC aluminum grinders. Constructed from high-quality materials, these machines are built to withstand the rigors of continuous operation.
Their robust design minimizes wear and tear, ensuring longevity even in demanding environments. Regular maintenance can further enhance their durability, allowing businesses to maximize their investment over time. The combination of precision engineering and durable construction makes these grinders a reliable choice for manufacturers seeking consistent performance.
Choosing the Right Size and Features for Your Workspace
Selecting the appropriate size and features for a compact CNC aluminum grinder is crucial for optimizing its performance within a specific workspace. Businesses must assess their production needs and available space before making a decision. A thorough evaluation of the types of materials being processed, as well as the complexity of the tasks at hand, will guide this selection process.
It is essential to choose a model that not only fits within the physical constraints of the workspace but also meets the operational demands. In addition to size, various features can enhance the functionality of compact CNC aluminum grinders. Options such as programmable controls, automatic tool changers, and advanced cooling systems can significantly improve efficiency and output quality.
Businesses should consider their specific requirements and future growth potential when selecting features, ensuring that the chosen grinder can adapt to evolving production needs. By carefully evaluating size and features, manufacturers can make informed decisions that lead to improved productivity and operational success.
Integrating Compact CNC Aluminum Grinders into Your Production Line
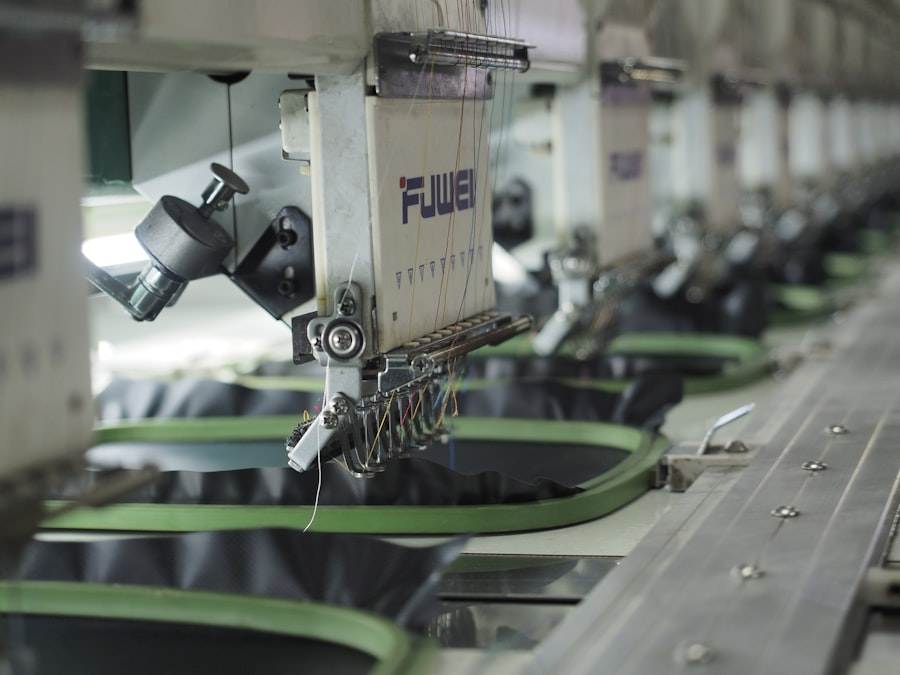
Integrating compact CNC aluminum grinders into an existing production line requires careful planning and execution. It is essential to assess how the new equipment will interact with current processes and machinery. A seamless integration can lead to enhanced workflow efficiency and reduced bottlenecks in production.
Businesses should consider factors such as material handling, operator training, and maintenance schedules during this integration phase. Collaboration between different departments—such as engineering, production, and maintenance—can facilitate a smoother transition when introducing new equipment like compact CNC aluminum grinders. Open communication ensures that all stakeholders understand the capabilities and limitations of the new machinery, allowing for better planning and execution of tasks.
By fostering a collaborative environment, businesses can maximize the benefits of integrating these advanced grinders into their production lines.
Tips for Maintaining and Optimizing Compact CNC Aluminum Grinders
Proper maintenance is vital for ensuring the longevity and optimal performance of compact CNC aluminum grinders. Regular inspections should be conducted to identify any signs of wear or potential issues before they escalate into more significant problems. Keeping the machine clean and free from debris will also contribute to its efficiency and accuracy.
Operators should be trained on best practices for maintenance, including lubrication schedules and proper handling techniques. In addition to routine maintenance, optimizing the use of compact CNC aluminum grinders can lead to improved productivity. Operators should familiarize themselves with all available features and settings to fully leverage the machine’s capabilities.
Experimenting with different grinding parameters can help identify optimal configurations for specific tasks, resulting in better quality outputs and reduced cycle times. By prioritizing both maintenance and optimization strategies, businesses can ensure that their compact CNC aluminum grinders operate at peak performance.
Future Innovations in Compact CNC Aluminum Grinder Technology
The landscape of manufacturing technology is continually evolving, and compact CNC aluminum grinders are no exception. Future innovations are likely to focus on enhancing automation capabilities, allowing for even greater efficiency in production processes. Developments in artificial intelligence could lead to smarter machines that can learn from previous operations and adjust settings automatically for optimal performance.
Additionally, advancements in materials science may result in even more durable components for these grinders, further extending their lifespan and reliability. As industries increasingly embrace sustainability, future models may also incorporate eco-friendly technologies that reduce energy consumption and waste generation during operation. By staying abreast of these innovations, manufacturers can position themselves at the forefront of technological advancements in compact CNC aluminum grinding solutions, ensuring they remain competitive in an ever-changing market landscape.
FAQs
What are CNC aluminum grinders?
CNC aluminum grinders are precision machining tools that use computer numerical control (CNC) technology to shape and finish aluminum materials. These grinders are commonly used in manufacturing and metalworking industries for creating precise and intricate designs.
What are the advantages of compact design in CNC aluminum grinders?
Compact design in CNC aluminum grinders allows for maximizing workspace efficiency. It enables the grinders to be easily integrated into smaller workspaces, saving valuable floor space and improving overall productivity. Additionally, compact design often results in lower energy consumption and reduced material waste.
How do CNC aluminum grinders contribute to workspace efficiency?
CNC aluminum grinders contribute to workspace efficiency by offering a smaller footprint, which allows for more efficient use of available space. This can lead to better organization, improved workflow, and increased productivity in manufacturing and metalworking environments.
What industries can benefit from the compact design advantages of CNC aluminum grinders?
A wide range of industries can benefit from the compact design advantages of CNC aluminum grinders, including aerospace, automotive, electronics, medical device manufacturing, and more. Any industry that requires precision machining of aluminum components can benefit from the space-saving and efficiency-enhancing features of compact CNC aluminum grinders.