In recent years, the automotive industry has witnessed a significant shift towards the use of aluminum as a primary material in vehicle manufacturing. This transition is largely driven by the increasing demand for fuel-efficient vehicles and the need to meet stringent environmental regulations. As automakers strive to reduce the weight of their vehicles, aluminum has emerged as a favored choice due to its favorable strength-to-weight ratio.
The lightweight nature of aluminum allows manufacturers to design vehicles that not only consume less fuel but also produce fewer emissions, aligning with global sustainability goals. The rise of aluminum in automotive applications is also fueled by advancements in manufacturing technologies. Innovations such as improved welding techniques and enhanced alloy formulations have made it easier for manufacturers to incorporate aluminum into their designs without compromising structural integrity.
As a result, many leading automotive brands are now integrating aluminum components into their vehicles, from body panels to engine parts, marking a significant evolution in automotive engineering.
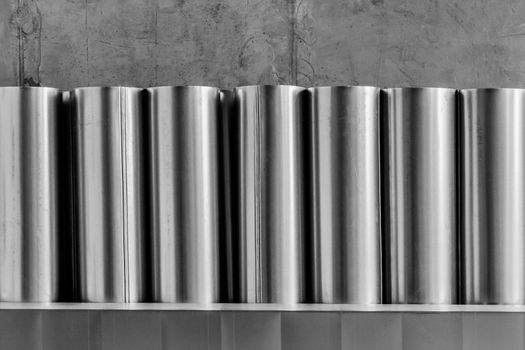
Key Takeaways
- Aluminum is increasingly being used in the automotive industry for its lightweight and strong properties, contributing to fuel efficiency and performance.
- Common misconceptions about aluminum strength are debunked, as it is proven to be a durable and reliable material for automotive design.
- The advantages of aluminum for automotive design include its corrosion resistance, recyclability, and ability to be formed into complex shapes.
- Aluminum plays a crucial role in achieving sleek and lightweight vehicles, contributing to improved aerodynamics and overall performance.
- Debunking myths surrounding aluminum durability reveals its ability to withstand harsh conditions and provide long-term reliability in automotive manufacturing.
Common Misconceptions about Aluminum Strength
Despite its growing popularity, aluminum is often misunderstood when it comes to its strength characteristics. A common misconception is that aluminum is inherently weak compared to traditional materials like steel. While it is true that aluminum has a lower density than steel, this does not equate to lower strength.
In fact, modern aluminum alloys can be engineered to achieve impressive strength levels, making them suitable for various structural applications in vehicles. The key lies in understanding that strength can be enhanced through alloying and heat treatment processes. Another misconception is that aluminum is prone to fatigue and failure under stress.
While it is true that certain grades of aluminum may exhibit fatigue under extreme conditions, advancements in alloy technology have produced materials that can withstand significant loads and stresses. Manufacturers are increasingly utilizing high-strength aluminum alloys that offer excellent fatigue resistance, making them ideal for critical automotive components. By dispelling these myths, it becomes clear that aluminum can be a robust and reliable material for automotive applications.
The Advantages of Aluminum for Automotive Design
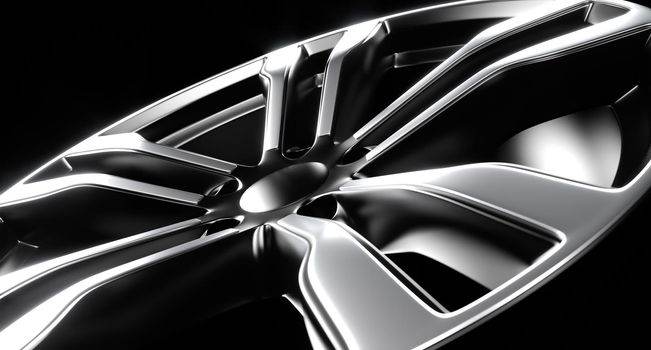
Aluminum offers a multitude of advantages that make it an attractive option for automotive design. One of the most significant benefits is its lightweight nature, which directly contributes to improved vehicle performance. By reducing the overall weight of a vehicle, manufacturers can enhance acceleration, braking, and handling characteristics.
This weight reduction also allows for more efficient use of powertrains, leading to better fuel economy and reduced emissions. In addition to its weight advantages, aluminum is highly malleable and can be easily shaped into complex forms. This flexibility in design enables engineers to create more aerodynamic vehicle profiles, which further enhances fuel efficiency.
The ability to produce intricate designs without compromising structural integrity allows for greater creativity in automotive styling. As a result, vehicles can achieve both aesthetic appeal and functional performance, making aluminum an essential material in modern automotive design.
The Role of Aluminum in Achieving Sleek and Lightweight Vehicles
Metrics | Benefits |
---|---|
Weight Reduction | Aluminum helps in achieving lightweight vehicles, improving fuel efficiency and performance. |
Strength | Aluminum provides high strength-to-weight ratio, enhancing vehicle safety and durability. |
Corrosion Resistance | Aluminum offers excellent corrosion resistance, increasing the lifespan of vehicles. |
Formability | Aluminum can be easily formed into complex shapes, allowing for sleek and aerodynamic vehicle designs. |
Recyclability | Aluminum is highly recyclable, contributing to sustainable and eco-friendly vehicle manufacturing. |
The pursuit of sleek and lightweight vehicles has become a defining trend in the automotive industry, and aluminum plays a pivotal role in this evolution. Its lightweight properties allow manufacturers to create vehicles that are not only visually appealing but also efficient in terms of performance. The reduction in weight achieved through the use of aluminum enables automakers to design vehicles with lower centers of gravity, improving stability and handling.
Moreover, the use of aluminum contributes to the overall aesthetic of modern vehicles. With its ability to be formed into smooth curves and sharp lines, aluminum allows designers to craft visually striking profiles that capture consumer interest. This combination of functionality and style has made aluminum a preferred material for high-end vehicles and sports cars, where performance and appearance are equally prioritized.
As the automotive industry continues to evolve, the role of aluminum in achieving sleek designs will only become more pronounced.
Debunking the Myths Surrounding Aluminum Durability
Durability is a critical factor in automotive manufacturing, and misconceptions about aluminum’s durability can hinder its acceptance in certain applications. One prevalent myth is that aluminum is more susceptible to corrosion than steel. While it is true that untreated aluminum can corrode under certain conditions, modern manufacturing techniques often involve protective coatings and treatments that significantly enhance corrosion resistance.
Additionally, aluminum naturally forms a protective oxide layer when exposed to air, which helps prevent further corrosion. Another myth is that aluminum components are more likely to suffer from impact damage compared to their steel counterparts. In reality, high-strength aluminum alloys are designed to absorb energy during impacts, providing excellent crashworthiness while maintaining structural integrity.
This characteristic makes aluminum an ideal choice for safety-critical components such as crumple zones and chassis structures. By addressing these misconceptions, it becomes evident that aluminum can offer durability on par with traditional materials used in automotive manufacturing.
How Aluminum Contributes to Fuel Efficiency and Performance

The integration of aluminum into vehicle design has profound implications for fuel efficiency and overall performance. By reducing vehicle weight, aluminum allows for smaller engines or hybrid powertrains to deliver the same level of performance as heavier vehicles with larger engines. This not only leads to improved fuel economy but also reduces greenhouse gas emissions, aligning with global efforts to combat climate change.
Furthermore, the lightweight nature of aluminum enhances acceleration and braking performance. Vehicles equipped with aluminum components can achieve quicker acceleration times due to reduced mass, allowing drivers to experience a more responsive driving experience. Additionally, lighter vehicles require less energy to decelerate, resulting in shorter stopping distances and improved safety.
As automakers continue to prioritize fuel efficiency and performance, the role of aluminum will remain central to their strategies.
The Future of Aluminum in Automotive Manufacturing
Looking ahead, the future of aluminum in automotive manufacturing appears promising as technological advancements continue to evolve. The development of new alloys and manufacturing processes will likely expand the range of applications for aluminum within the industry. Innovations such as 3D printing with aluminum alloys may revolutionize how components are produced, allowing for greater customization and efficiency in manufacturing.
Moreover, as electric vehicles (EVs) gain traction in the market, the demand for lightweight materials like aluminum will only increase. EVs benefit significantly from reduced weight since it directly impacts battery efficiency and range. As automakers strive to create more efficient electric models, the use of aluminum will play a crucial role in achieving these goals.
The ongoing research into recycling methods for aluminum will also contribute to sustainability efforts within the industry, ensuring that aluminum remains a viable option for future automotive applications.
Embracing the Strength and Sleekness of Aluminum
In conclusion, the rise of aluminum in the automotive industry represents a significant shift towards more sustainable and efficient vehicle design. By debunking common misconceptions about its strength and durability, it becomes clear that aluminum offers numerous advantages for modern automotive applications. Its lightweight nature not only enhances performance but also contributes to sleek designs that appeal to consumers.
As the industry continues to evolve, embracing the strengths of aluminum will be essential for meeting future challenges related to fuel efficiency and environmental sustainability. With ongoing advancements in technology and manufacturing processes, aluminum is poised to play an even more prominent role in shaping the future of automotive design and engineering. The journey towards lighter, more efficient vehicles is well underway, with aluminum leading the charge toward a more sustainable automotive landscape.
FAQs
What is the myth about aluminum’s strength?
The myth about aluminum’s strength is that it is not sturdy enough for certain applications, particularly in comparison to other materials such as steel.
Is aluminum actually strong enough for various applications?
Yes, aluminum is a strong and durable material that is suitable for a wide range of applications, including in the automotive, aerospace, and construction industries.
What are some advantages of using aluminum for strength?
Aluminum offers several advantages for strength, including its high strength-to-weight ratio, corrosion resistance, and ability to be easily formed into complex shapes.
How is aluminum’s strength compared to other materials like steel?
While steel is generally stronger than aluminum, aluminum’s strength-to-weight ratio is higher, making it a favorable choice for applications where weight is a concern.
What are some examples of products or structures that rely on aluminum’s strength?
Examples of products and structures that rely on aluminum’s strength include aircraft components, automotive parts, bicycle frames, and building facades.