Overview of Knife Making Efficiency
In the world of knife making, efficiency is paramount. Crafting a high-quality blade requires not only skill but also the right tools to streamline the process. Embracing modern technology, such as electric grinders, can significantly enhance productivity and consistency. When discussing knife-making efficiency, it’s essential to consider various factors that can impact the overall performance:
- Time Management: The ability to produce knives quickly without sacrificing quality is crucial for both hobbyists and professionals.
- Material Usage: Efficient grinding minimizes waste and maximizes the yield from raw materials.
- Skill Development: Leveraging efficient tools allows blade smiths to focus on refining their techniques rather than struggling with outdated equipment.
Each aspect contributes to improving the overall experience and output in knife making.
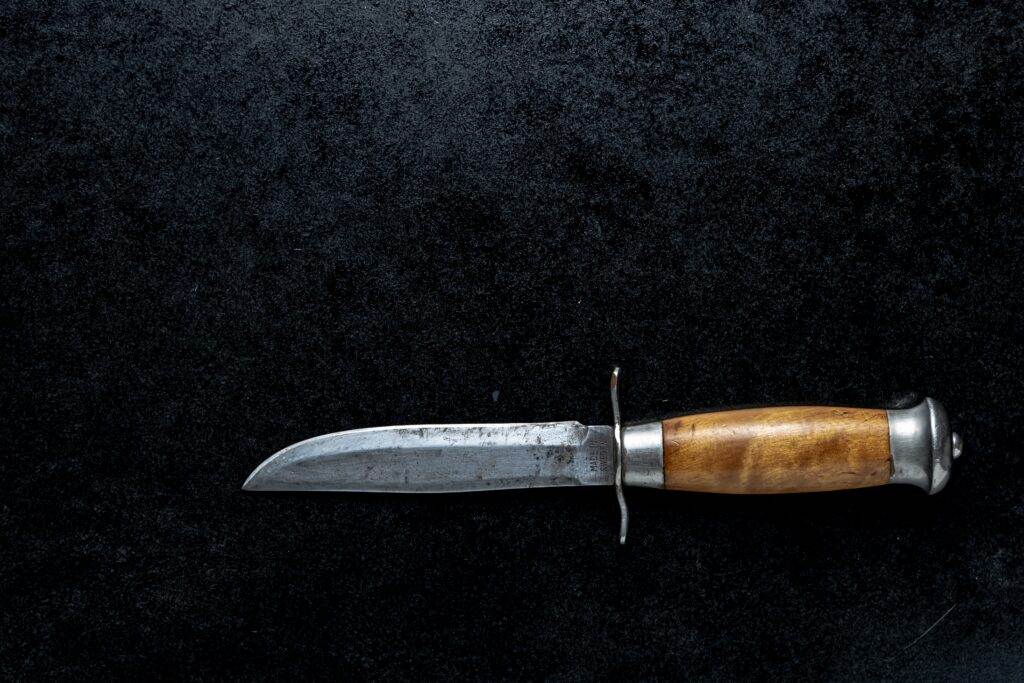
Importance of Using a 2×72 Grinder
At this juncture, the 2×72 grinder stands out as an indispensable tool for anyone serious about knife making. Its versatility and power make it the go-to choice for both beginners and seasoned professionals. Here’s why:
- Versatility: The flat, wide surface supports a variety of belt grits, allowing for everything from rough profiling to fine finishes in one machine.
- Speed: With its powerful motor, a 2×72 grinder can drastically reduce grinding time, providing high-speed sanding and shaping that traditional methods simply cannot match.
- Precision: The design facilitates accurate control, enabling makers to create intricate designs and razor-sharp edges effortlessly.
In essence, incorporating a 2×72 grinder into the knife making workflow not only enhances productivity but elevates the overall craftsmanship by allowing the maker to focus on the artistry involved.
History of 2×72 Grinders
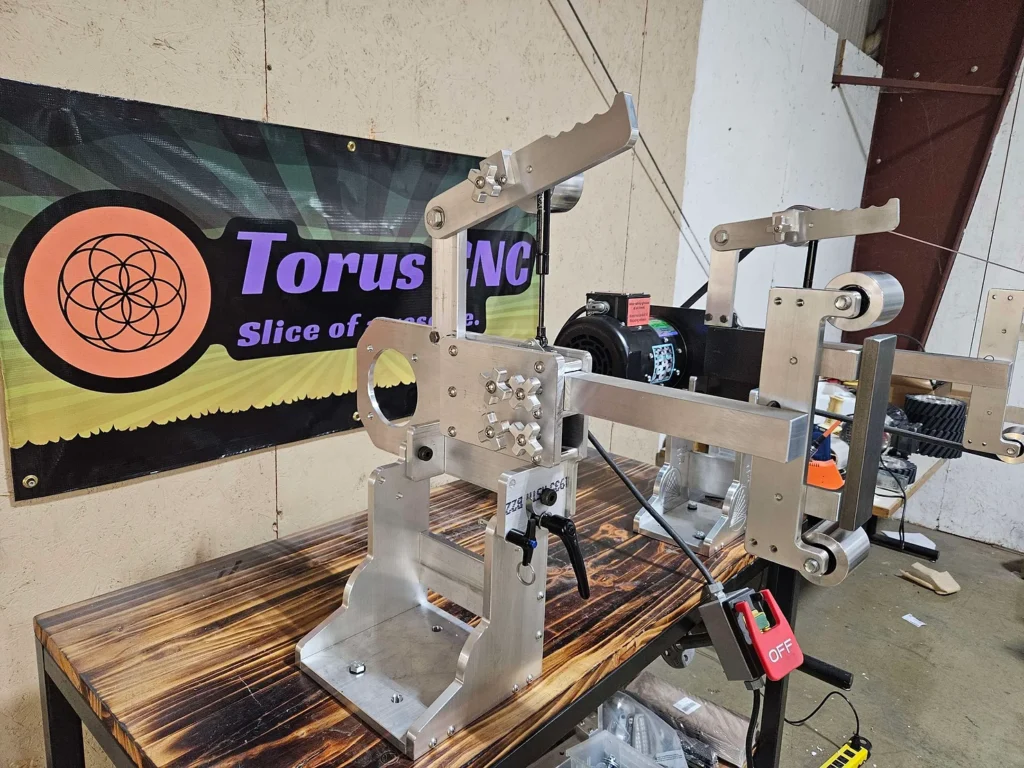
Evolution of Grinding Technology
The journey of grinding technology has been a fascinating one, significantly shaping the landscape of metalworking and knife making. Initially, blacksmiths depended on rudimentary tools and manual labor to shape metal, which was both time-consuming and labor-intensive. As industrialization took hold, innovations began to emerge, leading to the development of power-driven equipment. The introduction of belt grinders marked a significant turning point. Among these, the 2×72 grinder emerged as a formidable tool due to its unique dimensions and capabilities. Key milestones in this evolution include:
- Introduction of Electric Motors: The shift from manual sharpening to electric motors drastically improved efficiency.
- Belt Size Standardization: The 2×72 belt became a standard, offering versatility and ease of use for a variety of applications.
- Advancements in Materials: Development in grinding belts made it possible to grind faster and produce smoother finishes, enhancing overall quality.
This leap in technology has undoubtedly transformed the precision and speed of knife making.
Impact on Knife Making Industry
The introduction and widespread use of the 2×72 grinder have reshaped the knife making industry on multiple fronts. Its significance can be highlighted as follows:
- Increased Accessibility: With the ability to create high-quality knives at home, more enthusiasts are drawn into the craft, expanding the knife-making community.
- Enhanced Skill Development: The speed and efficiency of the 2×72 grinder allow knife makers to experiment with intricate designs, helping them hone their skills and craftsmanship.
- Professional Standards: This grinder enables makers to produce knives that meet or exceed professional standards, fostering a culture of quality within the industry.
The evolution of grinding technology, particularly the advent of the 2×72 grinder, has not only made knife making more efficient but has sparked creativity and innovation across the craft. As technology continues to progress, one can anticipate even more advancements that will further enhance the art of knife making.
Understanding the Components
Motor Power and Speed
One of the most fundamental elements of a 2×72 grinder is its motor, which plays a crucial role in determining the efficiency and effectiveness of knife making. A powerful motor not only enhances performance but also impacts the overall grinding experience. When evaluating motor power and speed, consider the following:
- Horsepower (HP): Most 2×72 grinders range from 1 HP to 3 HP. A higher horsepower enables quicker stock removal and smoother finishes, which can be essential for larger blades.
- RPM (Revolutions Per Minute): The speed at which the motor operates is also vital. Commonly, a grinder will have speeds ranging from 1,750 to 3,600 RPM. Higher speeds allow for more aggressive grinding but require careful handling to avoid overheating the blade.
- Torque: Motor torque is crucial for maintaining consistent power, especially during detailed work. Less torque can lead to stalling, which is frustrating and counterproductive.
Investing in a high-quality motor can greatly increase both the efficiency and quality of the finished product.
Belt Size and Material
Equally important to understanding the components of a 2×72 grinder is the belt size and material, which significantly influence the grinding process.
- Belt Size: The 2×72 designation refers to the belt’s dimensions—2 inches wide and 72 inches long. This standard sizing offers a vast array of belt grit options for various tasks, from heavy material removal to fine finishing.
- Belt Material: Common materials include aluminum oxide, ceramic, and zirconia. Each has its unique qualities:
- Aluminum Oxide: Great for general purpose and is cost-effective.
- Ceramic: Ideal for heavy grinding tasks due to its durability and longevity.
- Zirconia: Perfect for grinding hardened steel and provides a high removal rate.
By understanding these components—motor power and speed as well as belt size and material—knife makers can choose the appropriate tools for their specific needs, ultimately enhancing their craftsmanship and productivity.
Setting Up Your 2×72 Grinder
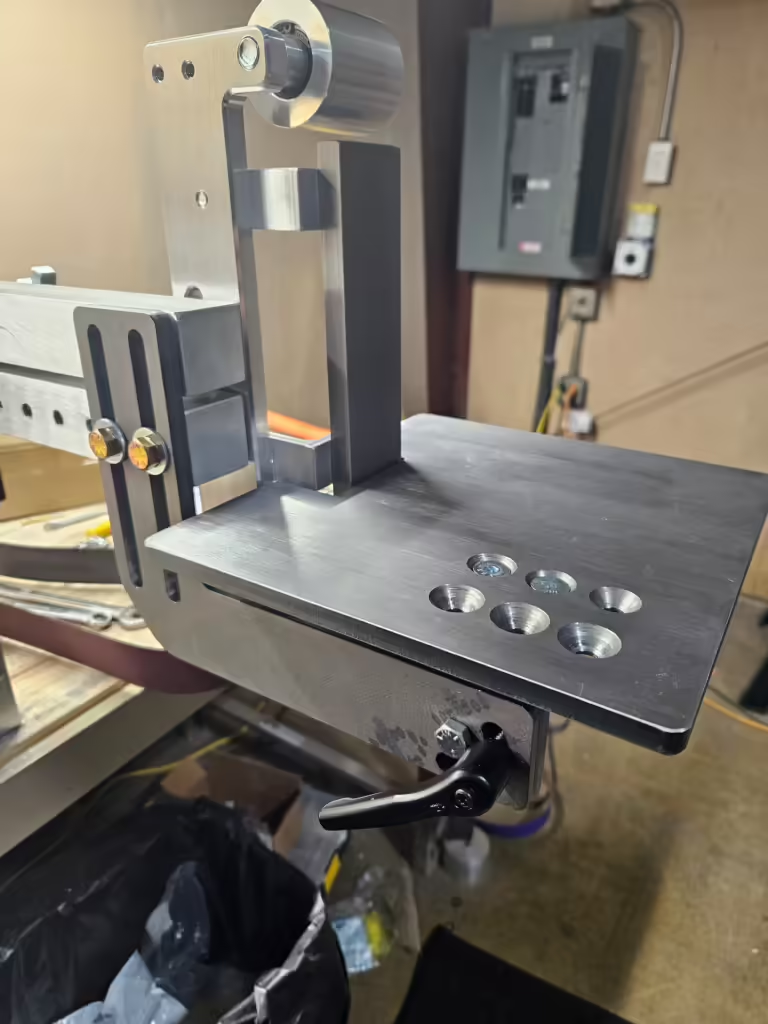
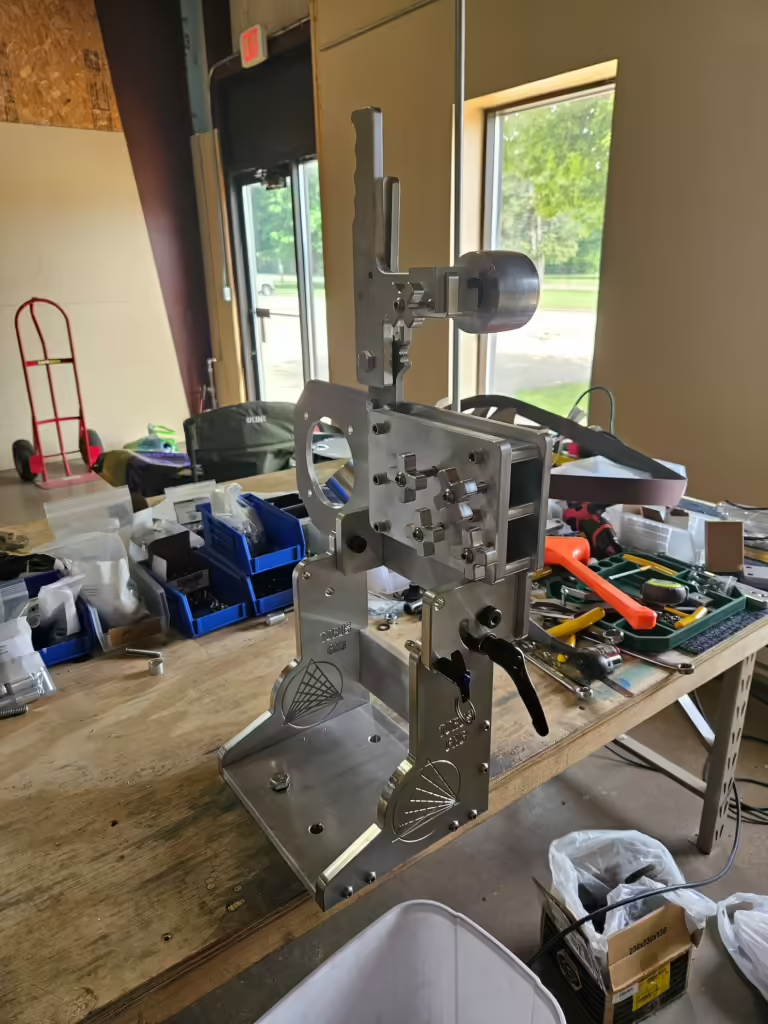
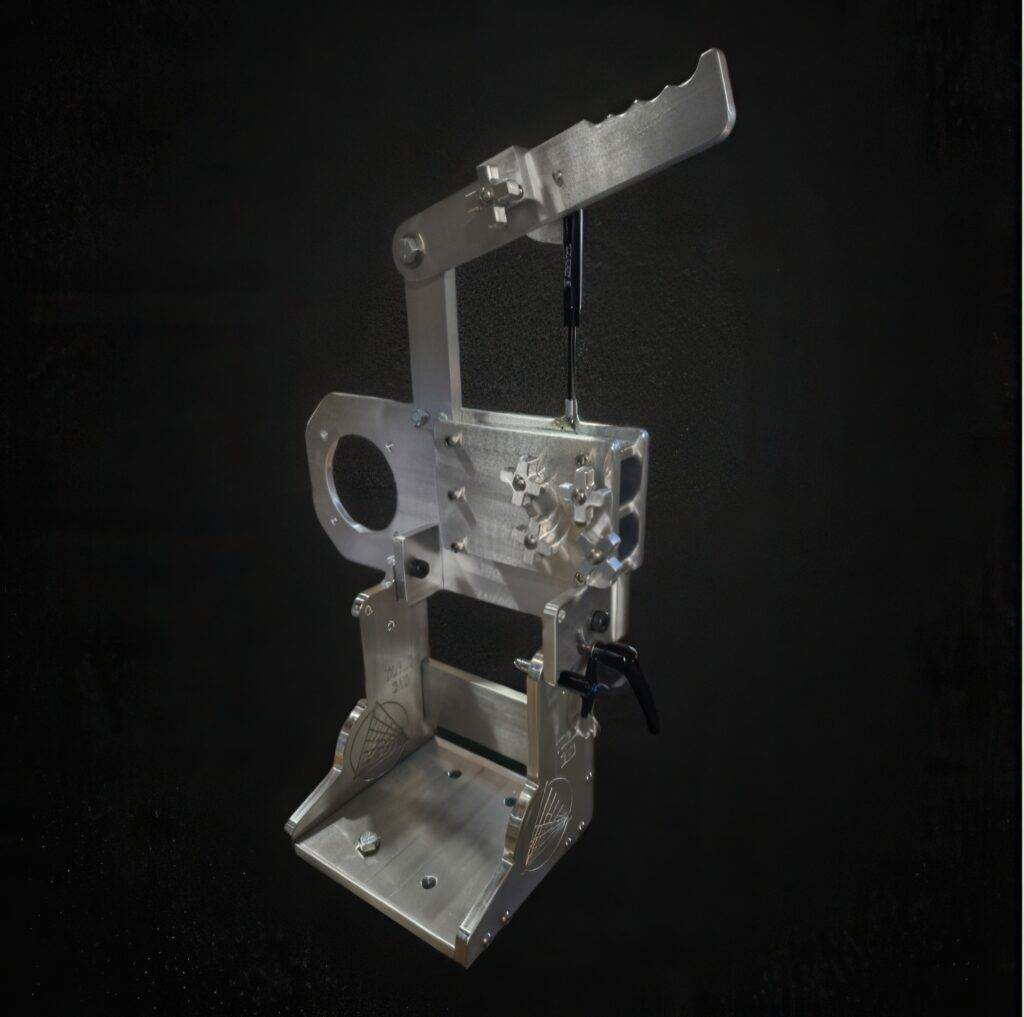
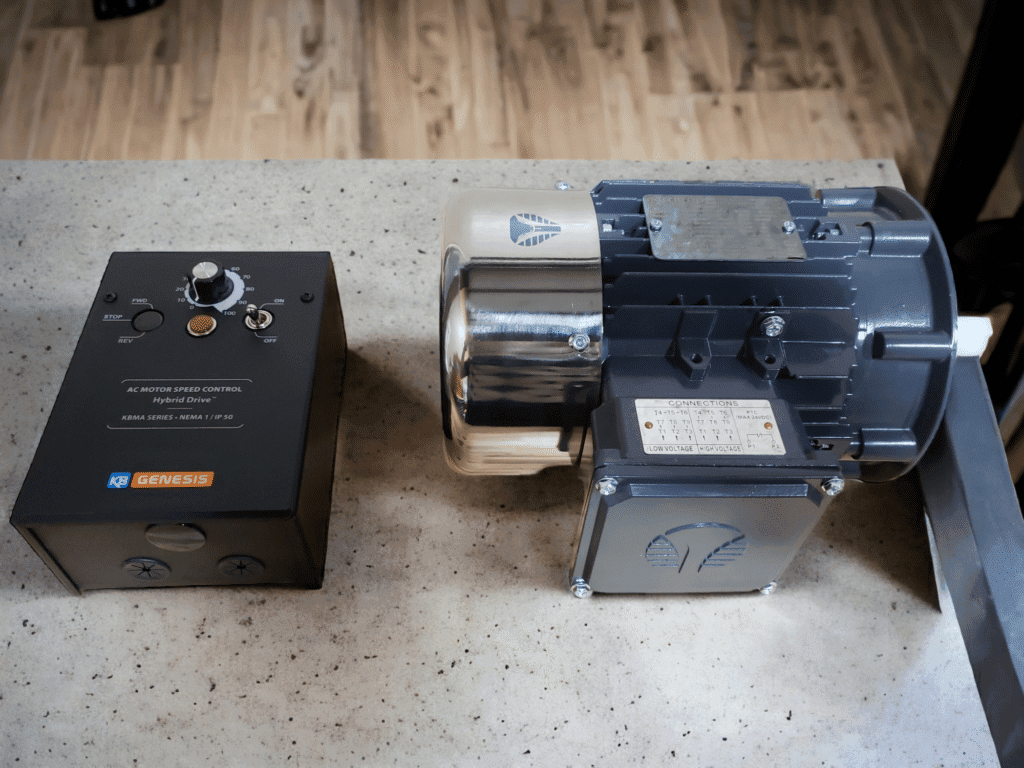
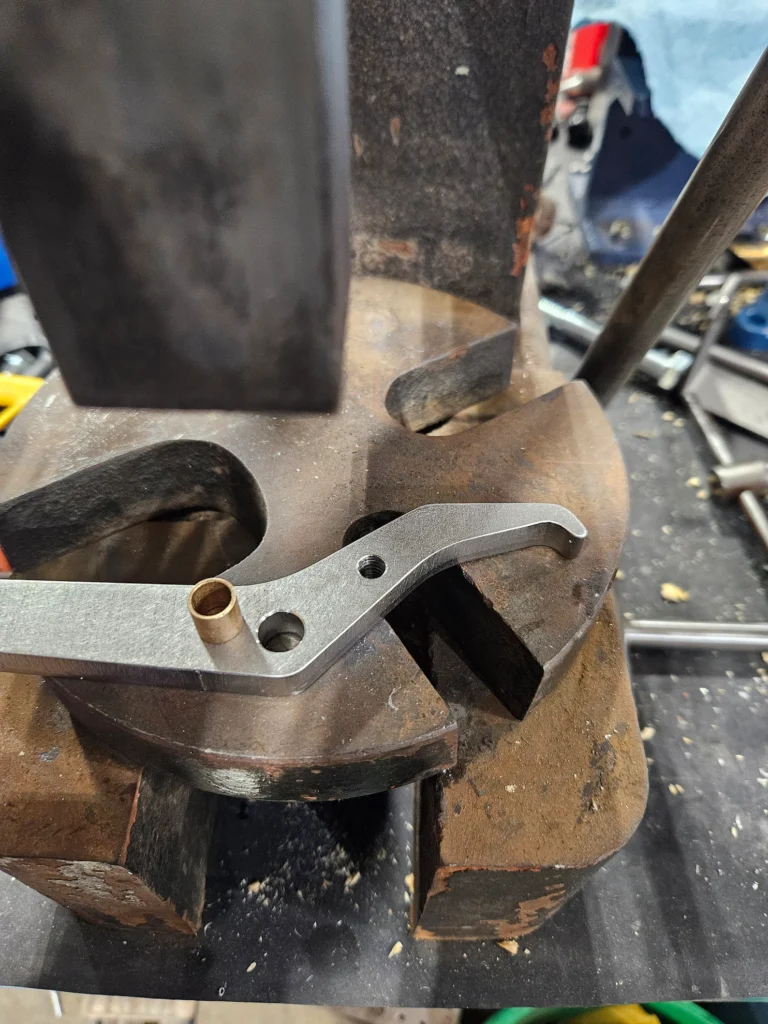
Proper Assembly Instructions
Setting up your 2×72 grinder correctly is essential for achieving optimal performance and safety. Ideally, you want to follow these step-by-step assembly instructions to ensure that your equipment is functioning smoothly:
- Unpack and Organize: Begin by laying out all components and tools required for assembly. Make sure you have:
- The grinder frame
- Motor
- Contact wheels
- Grinding belts
- Fasteners and tools
- Assemble the Frame: Start by attaching the motor to the grinder frame. Use the provided bolts and securely fasten them to prevent vibrations during operation.
- Install the Contact Wheels: Position the contact wheels on the appropriate mounts and ensure they are aligned correctly. This alignment will prevent unnecessary wear on both the wheels and the belts.
- Attach the Belt Guard: Safety first! Make sure to install the belt guard to protect yourself from moving parts.
- Final Checks: Before powering it up, double-check that all connections are tight, and the belts are properly aligned.
Adjusting for Precision and Safety
Once your grinder is assembled, it’s crucial to make adjustments for precision and safety:
- Belt Tension: Adjust the tension of the belt to ensure it is tight enough to prevent slipping, yet not so tight that it strains the motor.
- Tracking Adjustment: Make sure to adjust the tracking of the belt. This ensures it runs straight and does not wear unevenly.
- Height Adjustment: Position your grinder at a comfortable work height. Ideally, your elbows should be slightly above the grinder to maintain good posture.
- Safety Gear: Always wear appropriate protective gear such as goggles, respirators, and hearing protection when using your grinder.
By paying careful attention to assembly and making the right adjustments, you can ensure that your 2×72 grinder is both effective and safe, setting the stage for a smooth and productive knife-making experience.
Techniques for Efficient Knife Making
Blade Grinding Methods
Once your 2×72 grinder is set up and ready to go, mastering various blade grinding methods will significantly enhance your knife-making efficiency. Different techniques are suited for specific tasks, and understanding when to use each can save time and improve results.
- Profile Grinding: This is the initial step where you shape the knife into the desired outline. Use a coarse grit belt (around 36 to 60 grit) to quickly remove material. Keep the blade at a consistent angle to achieve symmetry.
- Edge Grinding: After profiling, shift to a finer grit belt (80 to 120 grit) to refine the cutting edge. Focus on maintaining an angle—typically between 15 to 20 degrees—for optimal sharpness.
- Hollow Grinding: This method involves using a wheel to create a concave surface along the edge. It’s particularly effective for creating a sharper edge on thinner blades. Adjust the belt position to work closer to the wheel for this technique.
- Flat Grinding: Ideal for thicker blades, flat grinding maintains a straight edge without concaving. This method can also help in achieving a sturdier blade.
Each of these techniques contributes to creating a functional blade, so it’s beneficial to practice and become familiar with them.
Finishing and Polishing
After the grinding processes, finishing and polishing are critical to achieving that professional look and feel. Proper finishing not only enhances appearance but can also improve performance and durability.
- Sanding: Start with a medium grit (around 220) and progress to finer grits (up to 600 or higher) using your grinder. This helps eliminate any grinding marks and prepares the surface for polishing.
- Buffing: Utilize a buffing wheel with polishing compound to achieve a shine on your blade. This step not only enhances aesthetics but also adds a protective layer, reducing oxidation.
- Final Touches: Inspect your work closely for any imperfections. A quick touch-up with a finer belt or a hand-held pad can make a significant difference.
By mastering these techniques for both blade grinding and finishing, knife makers can streamline their workflow and produce high-quality, professional-grade knives consistently.
Advantages of Using a 2×72 Grinder
Time-saving Benefits
One of the most compelling reasons to invest in a 2×72 grinder is the significant time savings it offers. In the realm of knife making, an efficient workflow can set apart the hobbyist from the professional. Here are some of the specific time-saving benefits:
- Rapid Stock Removal: The power and speed of a 2×72 grinder allow for quick removal of material, accelerating the profiling and shaping of blades. This means less time spent on each project without sacrificing quality.
- Faster Belt Changes: With the right setup, switching belts can be accomplished within minutes, enabling knife makers to move smoothly between different grits and tasks.
- Reduced Fatigue: The design of a 2×72 grinder minimizes the physical strain on the user. This allows for longer working sessions without the fatigue often associated with hand tools, enhancing productivity overall.
In the fast-paced world of knife making, these efficiencies are invaluable, allowing craftsmen to take on more projects and explore creative designs.
Consistent and Professional Results
In addition to time savings, using a 2×72 grinder ensures a level of consistency and professionalism that is hard to achieve with manual tools. Here’s how:
- Uniform Grinding: The control offered by a 2×72 grinder facilitates consistent grinding angles and pressures, leading to uniform results across multiple pieces. This is crucial for maintaining quality, especially for batch production.
- Enhanced Finish Quality: The versatility in belt options allows knife makers to easily switch from rough grinding to fine finishing, ensuring each blade looks polished and is functionally effective.
- Improved Precision: With the grinder’s adjustable components, users can achieve highly precise outcomes, resulting in blades that not only perform better but also meet exact specifications required by customers or projects.
Overall, the advantages of using a 2×72 grinder in terms of time efficiency and consistency not only enhance the knife-making process but also elevate the quality of the finished product, solidifying its place as a vital tool in any craftsman’s workshop.
Safety Measures and Maintenance
Protective Gear and Procedures
Ensuring safety while using your 2×72 grinder is paramount. Proper protective gear and adherence to safety procedures can help prevent accidents and injuries. Here are essential safety measures to consider:
- Eye Protection: Always wear safety glasses or goggles to protect against flying debris and sparks generated during grinding. Consider using a face shield for added protection.
- Hearing Protection: The noise generated by grinders can be significant. Use earplugs or earmuffs to protect your hearing during prolonged use.
- Respiratory Protection: Grinding produces fine dust that may be harmful when inhaled. Wearing a dust mask or respirator helps ensure that you are not exposed to harmful particles.
- Proper Clothing: Wear long-sleeved shirts and resistant gloves to protect your skin. Avoid loose clothing that could get caught in moving parts.
- Posture and Positioning: Maintain a stable stance while operating the grinder, keeping the work area tidy to minimize the risk of tripping hazards.
By adhering to these safety measures, you create a secure working environment conducive to effective knife making.
Cleaning and Lubricating Your Grinder
Maintenance is also crucial to keep your grinder working efficiently over time. Regular cleaning and lubrication can extend the lifespan of the equipment:
- Daily Cleaning: After each use, clean the grinder to remove dust and debris. A compressed air blower works well to clear out any particles lodged in crevices.
- Belt Inspection: Routinely check the grinding belts for wear and tear. Replace any frayed or worn belts to maintain quality grinding performance.
- Lubrication: Periodically, apply lubricant to moving parts as per the manufacturer’s guidelines. This reduces friction and prevents premature wear.
- Alignment Checks: Regularly inspect the alignment of wheels and belts. Proper alignment is essential for optimal performance and to prevent uneven wear.
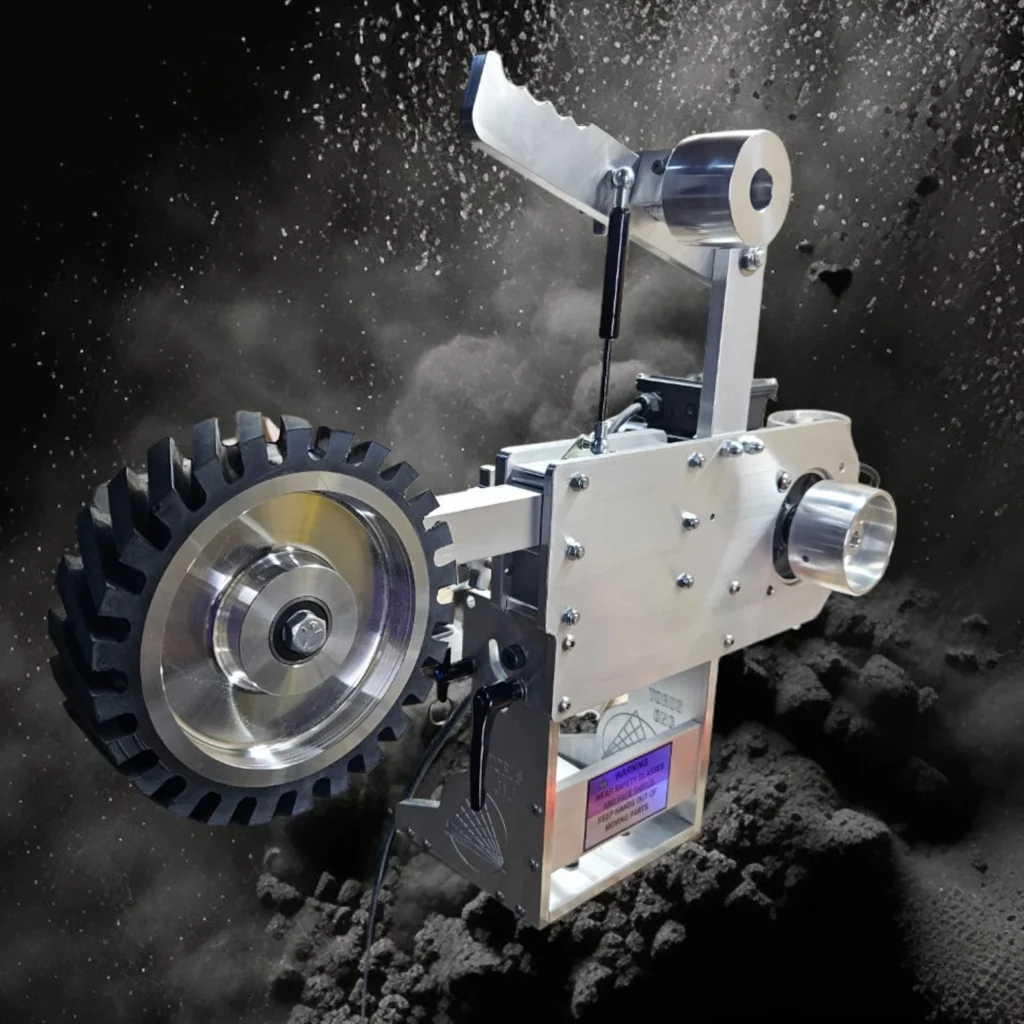
Incorporating these safety measures and maintenance practices into your routine ensures that your 2×72 grinder remains a reliable and safe tool for your knife-making projects. By prioritizing safety and upkeep, you can focus on developing your skills and achieving professional-quality results.