In the realm of manufacturing, the demand for precision and efficiency has never been higher. As industries evolve, the need for customized solutions becomes increasingly apparent. CNC (Computer Numerical Control) aluminum customization stands at the forefront of this evolution, offering unparalleled accuracy and versatility.
This technology allows manufacturers to create intricate designs and components tailored to specific requirements, making it an invaluable asset in various sectors, from aerospace to automotive. CNC aluminum customization leverages advanced machining techniques to produce parts that meet exact specifications. The process involves using computer-controlled machines to cut, shape, and finish aluminum materials with remarkable precision.
This capability not only enhances the quality of the final product but also streamlines production processes, reducing lead times and minimizing waste. As businesses seek to differentiate themselves in competitive markets, CNC aluminum customization emerges as a powerful tool for innovation and efficiency.

Key Takeaways
- CNC aluminum customization offers a wide range of benefits for industries looking to upgrade their parts and components.
- Upgrading to CNC aluminum parts can result in improved performance, durability, and precision for various applications.
- Customization options for CNC aluminum parts include intricate designs, complex shapes, and specific material properties to meet unique industry needs.
- The process of upgrading to CNC aluminum is simplified with the use of advanced technology and expertise in the field.
- Successful case studies demonstrate the positive impact of CNC aluminum customization on industry, showcasing improved efficiency and cost savings.
Benefits of Upgrading to CNC Aluminum Parts
Upgrading to CNC aluminum parts offers a multitude of advantages that can significantly enhance operational efficiency and product quality. One of the primary benefits is the precision that CNC machining provides. Traditional manufacturing methods often struggle to achieve the same level of accuracy, leading to inconsistencies and potential rework.
With CNC technology, manufacturers can produce components that adhere closely to design specifications, ensuring a perfect fit and function every time. Another key benefit is the material properties of aluminum itself. Known for its lightweight yet durable characteristics, aluminum is an ideal choice for a wide range of applications.
By utilizing CNC machining, manufacturers can exploit these properties to create parts that are not only strong but also lightweight, contributing to improved performance in various applications. This is particularly advantageous in industries such as aerospace and automotive, where weight reduction can lead to enhanced fuel efficiency and overall performance.
Customization Options for CNC Aluminum Parts
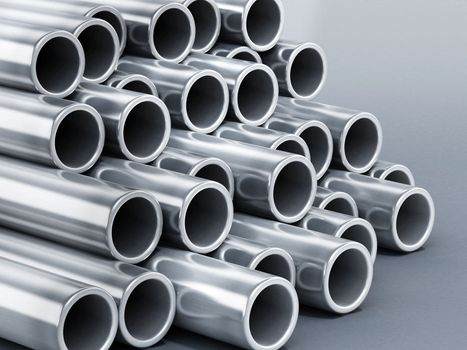
The customization options available with CNC aluminum parts are virtually limitless, allowing manufacturers to tailor components to their specific needs. One of the most significant aspects of customization is the ability to create complex geometries that would be challenging or impossible to achieve with traditional manufacturing methods. This includes intricate designs, unique shapes, and detailed features that enhance both functionality and aesthetics.
Additionally, manufacturers can choose from a variety of surface finishes and treatments to further customize their aluminum parts. Options such as anodizing, powder coating, and polishing not only improve the appearance of the components but also enhance their resistance to corrosion and wear. This level of customization ensures that the final product not only meets functional requirements but also aligns with branding and design standards.
Simplified Process of Upgrading to CNC Aluminum
Steps | Details |
---|---|
Step 1 | Assess current equipment and capabilities |
Step 2 | Research CNC aluminum machining options |
Step 3 | Investigate CNC machine suppliers |
Step 4 | Acquire necessary CNC equipment |
Step 5 | Train staff on CNC aluminum machining |
Step 6 | Implement CNC aluminum machining processes |
Transitioning to CNC aluminum parts may seem daunting at first, but the process is more straightforward than many manufacturers anticipate. The first step typically involves assessing current production methods and identifying areas where CNC machining could provide improvements. This evaluation allows businesses to pinpoint specific components that would benefit from customization and precision machining.
Once the decision is made to upgrade, collaborating with a reputable CNC machining provider is essential. Companies like TorusCNC 2×72 Grinders specialize in delivering high-quality CNC solutions tailored to individual needs. They can assist in designing parts, selecting materials, and optimizing production processes.
With their expertise, manufacturers can navigate the transition smoothly, ensuring that they reap the full benefits of CNC aluminum customization without significant disruptions to their operations.
Case Studies: Successful Implementations of CNC Aluminum Customization
Numerous industries have successfully implemented CNC aluminum customization, showcasing its transformative impact on production processes. For instance, in the aerospace sector, a leading manufacturer adopted CNC aluminum parts for their aircraft components. By utilizing advanced machining techniques, they were able to produce lighter and more aerodynamic parts that significantly improved fuel efficiency.
The precision achieved through CNC machining also reduced assembly time and minimized errors, leading to substantial cost savings. In another case, an automotive company sought to enhance the performance of their vehicles by integrating custom CNC aluminum components into their designs. By collaborating with a specialized CNC provider, they developed unique engine parts that optimized airflow and reduced weight.
The result was a noticeable improvement in vehicle performance and handling. These case studies illustrate how CNC aluminum customization not only meets industry demands but also drives innovation and competitive advantage.
Cost Considerations for Upgrading to CNC Aluminum
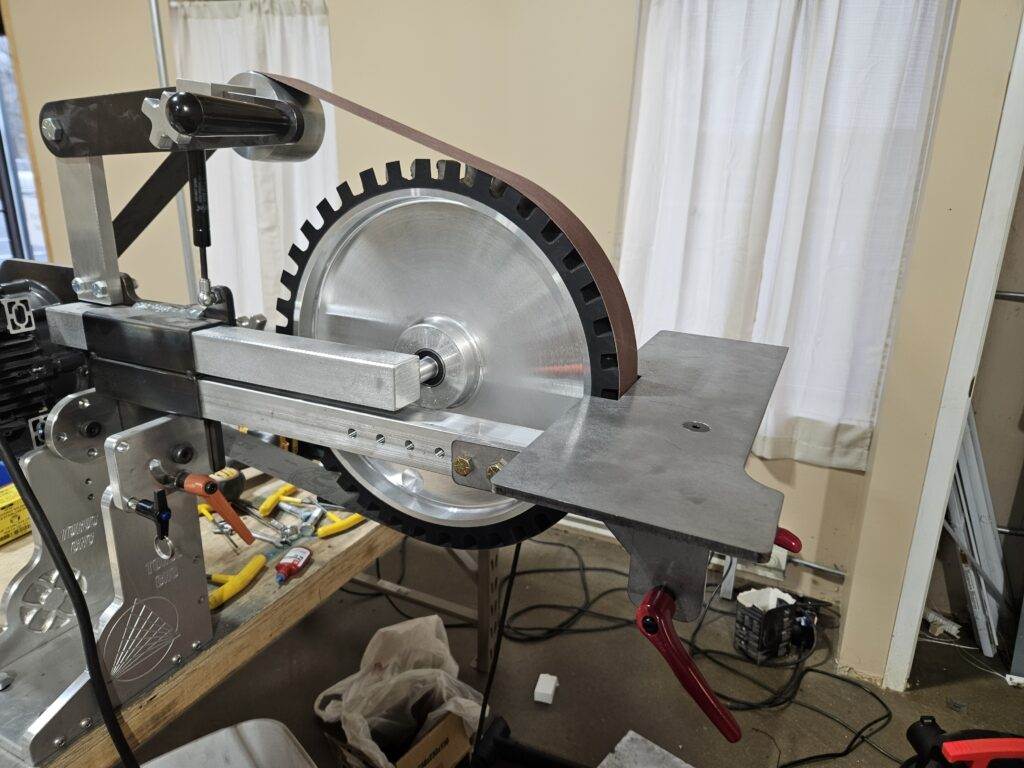
While the benefits of upgrading to CNC aluminum parts are clear, cost considerations are an essential aspect of the decision-making process. Initially, there may be higher upfront costs associated with acquiring CNC machinery or outsourcing production to specialized providers like TorusCNC 2×72 Grinders. However, it is crucial to view these costs in the context of long-term savings and efficiency gains.
Over time, the precision and consistency offered by CNC machining can lead to reduced material waste and lower labor costs due to decreased rework and faster production times. Additionally, the durability of aluminum parts often results in lower maintenance costs over their lifespan. When evaluating the overall financial impact, many manufacturers find that the initial investment pays off through enhanced productivity and reduced operational expenses.
Future Trends in CNC Aluminum Customization
As technology continues to advance, several trends are emerging in the field of CNC aluminum customization that promise to shape its future. One notable trend is the increasing integration of automation and artificial intelligence into CNC machining processes. These technologies can optimize production schedules, improve quality control, and enhance overall efficiency by minimizing human error.
Another trend is the growing emphasis on sustainability within manufacturing practices. As industries strive to reduce their environmental impact, there is a rising demand for eco-friendly materials and processes. CNC aluminum customization aligns well with this trend, as aluminum is highly recyclable and can be sourced sustainably.
Manufacturers are likely to explore innovative ways to incorporate sustainable practices into their CNC operations while maintaining high standards of quality and performance.
The Impact of CNC Aluminum Customization on Industry
CNC aluminum customization represents a significant advancement in manufacturing technology, offering numerous benefits that can transform production processes across various industries. From enhanced precision and material properties to limitless customization options, the advantages are compelling for manufacturers seeking a competitive edge. As businesses increasingly recognize the value of upgrading to CNC aluminum parts, they position themselves for success in an ever-evolving market.
The future of CNC aluminum customization looks promising, with emerging trends poised to further enhance its impact on industry practices. By embracing these advancements and collaborating with specialized providers like TorusCNC 2×72 Grinders, manufacturers can navigate the complexities of modernization while reaping substantial rewards in efficiency, quality, and sustainability. Ultimately, the integration of CNC aluminum customization will continue to shape the landscape of manufacturing, driving innovation and excellence for years to come.
FAQs
What is CNC aluminum design?
CNC aluminum design refers to the process of creating aluminum parts or products using computer numerical control (CNC) machines. This process allows for precise and complex designs to be achieved with aluminum material.
How do CNC aluminum designs facilitate customization?
CNC aluminum designs facilitate customization by allowing for precise and intricate designs to be created, making it easier to modify and customize products according to specific requirements. This modularity enables easy upgrades and alterations to the design.
What are the benefits of using CNC aluminum designs for customization?
Using CNC aluminum designs for customization offers benefits such as high precision, durability, and the ability to create complex and unique designs. It also allows for easy integration of additional components or modifications, making upgrades and customization more efficient.
What industries can benefit from CNC aluminum designs for customization?
Various industries can benefit from CNC aluminum designs for customization, including aerospace, automotive, electronics, and consumer goods. These industries often require precise and customized components, making CNC aluminum designs an ideal choice for their manufacturing needs.