The 2×72 grinder is a vital tool in the world of metalworking and woodworking, renowned for its versatility and efficiency. This machine is primarily used for shaping, sharpening, and finishing various materials, making it an essential piece of equipment for blacksmiths, knife makers, and artisans alike. The designation “2×72” refers to the size of the belt used in the grinding process, which measures two inches in width and seventy-two inches in length.
This specific configuration allows for a wide range of applications, from heavy material removal to fine finishing work. TorusCNC has established itself as a leader in the production of 2×72 grinders, offering machines that combine robust construction with advanced features. These grinders are designed to meet the demands of both hobbyists and professionals, providing a reliable solution for various grinding tasks.
With a focus on quality and performance, TorusCNC’s 2×72 grinders are engineered to deliver consistent results, making them a preferred choice among users who require precision and durability in their tools.
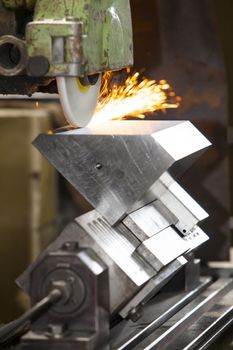
Key Takeaways
- 2×72 Grinder is a popular tool used in metalworking and knife making for shaping and sharpening metal components.
- Finite Element Analysis (FEA) is a powerful tool in CNC manufacturing that allows for virtual testing and optimization of designs before physical production.
- FEA can help identify weak points and areas for improvement in the design of 2×72 Grinder, leading to enhanced durability and efficiency.
- By implementing FEA, manufacturers can optimize the design and performance of 2×72 Grinder to ensure better stress and strain distribution in its components.
- FEA-driven design changes can be incorporated into the CNC manufacturing process to enhance the overall quality and performance of 2×72 Grinder.
Understanding Finite Element Analysis (FEA) in CNC Manufacturing
Finite Element Analysis (FEA) is a computational technique used to predict how products will react to real-world forces, vibration, heat, and other physical effects. In the context of CNC manufacturing, FEA plays a crucial role in the design and optimization of machinery, including the 2×72 grinder. By breaking down complex structures into smaller, manageable elements, engineers can analyze the behavior of each component under various conditions.
This method allows for a detailed understanding of how different materials and designs will perform, ultimately leading to improved product reliability and efficiency. Incorporating FEA into the design process enables manufacturers to identify potential weaknesses in their products before they are built. This proactive approach not only saves time and resources but also enhances the overall quality of the final product.
For TorusCNC, utilizing FEA in the development of their 2×72 grinders means that they can ensure their machines are not only effective but also capable of withstanding the rigors of daily use. By simulating real-world conditions, engineers can make informed decisions about material selection, structural design, and other critical factors that influence performance.
Identifying Areas for Improvement in 2×72 Grinder
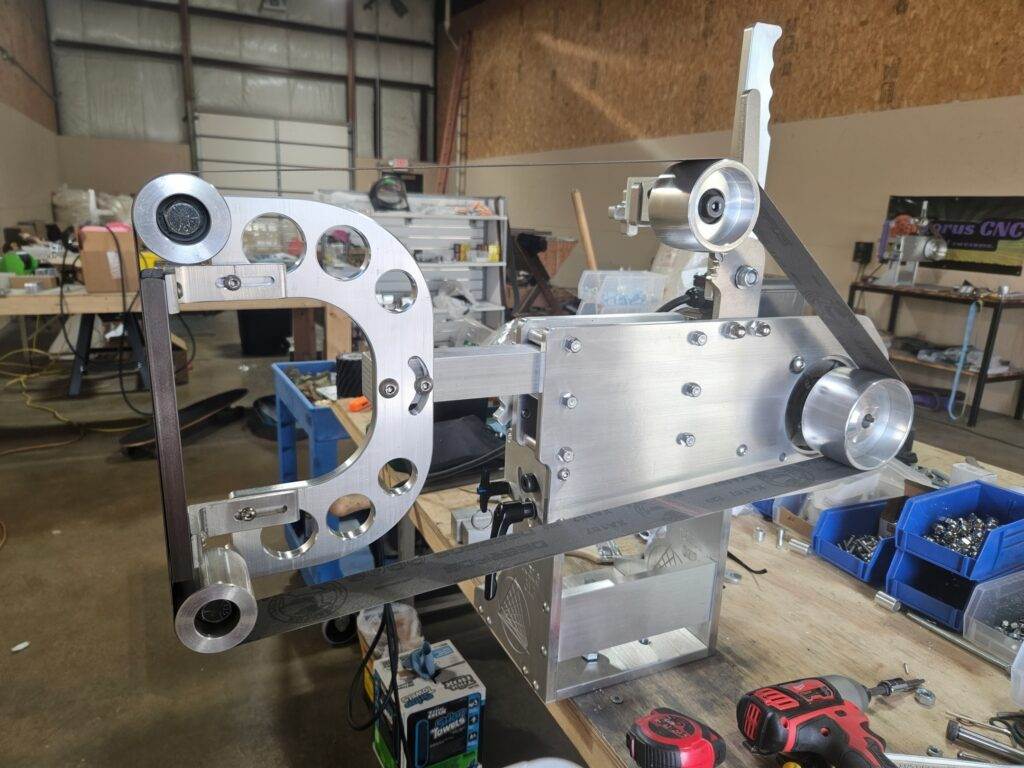
To enhance the performance of the 2×72 grinder, it is essential to identify specific areas that may benefit from improvement. One common aspect that can be scrutinized is the grinder’s frame and support structure. A robust frame is crucial for minimizing vibrations during operation, which can lead to inaccuracies in grinding and affect the quality of the finished product.
By analyzing the current design through FEA, engineers can pinpoint areas where material can be added or removed to optimize strength without compromising weight. Another area ripe for enhancement is the motor and drive system. The efficiency of these components directly impacts the grinder’s performance.
By examining the torque and power distribution through FEA simulations, manufacturers can determine if adjustments are needed to improve energy consumption or increase output. Additionally, evaluating the cooling mechanisms within the grinder can lead to better thermal management, ensuring that components operate within safe temperature ranges during extended use.
Implementing FEA to Optimize Design and Performance
Metrics | Value |
---|---|
Number of FEA simulations conducted | 50 |
Reduction in material usage | 15% |
Improvement in structural strength | 20% |
Reduction in product weight | 10% |
Once areas for improvement have been identified, implementing FEA becomes a critical step in optimizing design and performance. Engineers can create detailed models of the 2×72 grinder’s components and simulate various operational scenarios to assess how changes will affect overall functionality. This iterative process allows for rapid prototyping without the need for physical models, significantly reducing development time.
For TorusCNC, this means that they can refine their 2×72 grinder designs based on empirical data derived from FEA simulations. By testing different configurations and materials virtually, they can arrive at an optimal design that balances performance with cost-effectiveness. This approach not only enhances the grinder’s capabilities but also ensures that it meets or exceeds industry standards for safety and reliability.
Analyzing Stress and Strain Distribution in 2×72 Grinder Components
A critical aspect of FEA is its ability to analyze stress and strain distribution across various components of the 2×72 grinder. By understanding how forces are transmitted through the machine during operation, engineers can identify potential failure points and areas that may require reinforcement. This analysis is particularly important for high-stress components such as the motor mounts, belt tensioners, and grinding arms.
Through detailed simulations, engineers can visualize how different loads affect each part of the grinder. For instance, if a specific component experiences excessive strain under normal operating conditions, it may indicate a need for redesign or material substitution. By addressing these issues early in the design process, TorusCNC can enhance the longevity and reliability of their grinders, ensuring that they perform optimally even under demanding conditions.
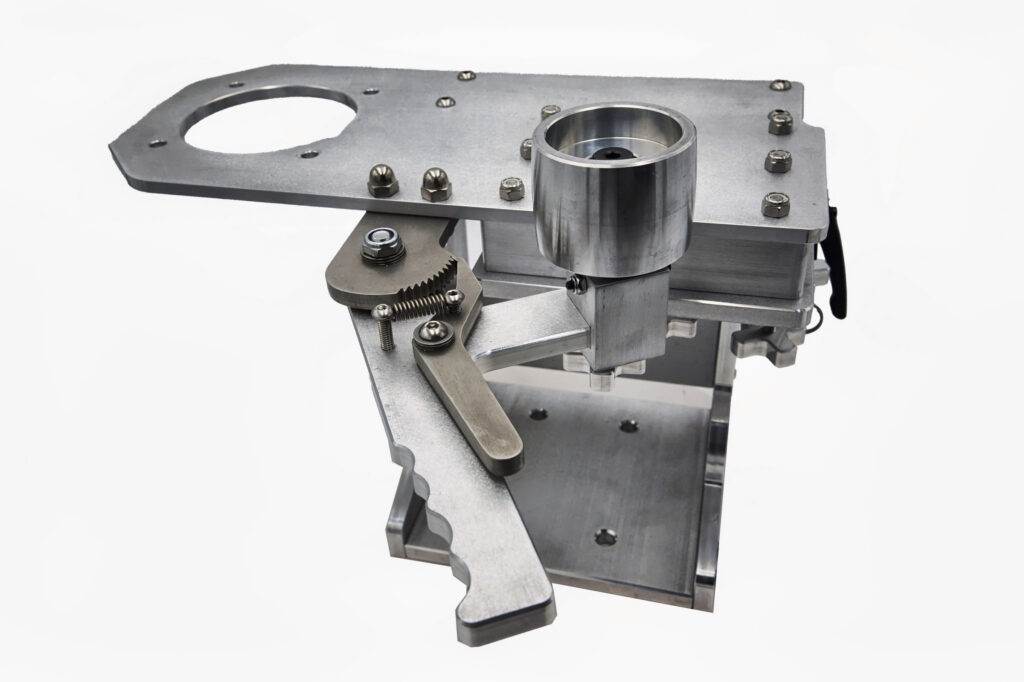
Enhancing Durability and Efficiency through FEA Results
The insights gained from FEA not only contribute to improved durability but also enhance overall efficiency in the 2×72 grinder’s operation. By optimizing component designs based on stress analysis, manufacturers can create machines that are less prone to wear and tear over time. This durability translates into lower maintenance costs and longer service life for users, making TorusCNC grinders a wise investment for both professionals and hobbyists.
Moreover, efficiency gains can be realized through better energy management within the grinder’s system. By analyzing power distribution and identifying areas where energy loss occurs, engineers can implement design changes that minimize waste. This not only improves performance but also aligns with growing demands for sustainable manufacturing practices.
As a result, TorusCNC’s commitment to utilizing FEA leads to products that are not only high-performing but also environmentally responsible.
Incorporating FEA-Driven Design Changes in CNC Manufacturing Process
Incorporating FEA-driven design changes into the CNC manufacturing process requires a collaborative approach between engineers and production teams. Once optimal designs have been established through simulations, it is essential to translate these findings into practical manufacturing techniques. This may involve adjusting machining processes, selecting appropriate materials, or implementing new quality control measures to ensure that the final product aligns with the intended specifications.
For TorusCNC, this integration means that their manufacturing processes are continuously evolving based on data-driven insights from FEA analyses. By fostering a culture of innovation and responsiveness within their teams, they can quickly adapt to new findings and implement changes that enhance product quality. This agility not only benefits their 2×72 grinders but also positions TorusCNC as a forward-thinking leader in CNC manufacturing.
The Future of 2×72 Grinder Improvement with FEA in CNC Manufacturing
The future of 2×72 grinder improvement lies in the continued application of Finite Element Analysis within CNC manufacturing processes. As technology advances and computational power increases, manufacturers like TorusCNC will be able to conduct even more sophisticated simulations that provide deeper insights into product performance. This ongoing commitment to innovation will enable them to refine their designs further, ensuring that their grinders remain at the forefront of industry standards.
By embracing FEA as a core component of their design philosophy, TorusCNC is not only enhancing the durability and efficiency of their 2×72 grinders but also setting a benchmark for quality in CNC manufacturing. As they continue to leverage this powerful analytical tool, users can expect even greater advancements in performance and reliability from their products. The integration of FEA into every stage of development signifies a promising future for both manufacturers and end-users alike, paving the way for more efficient and effective tools in metalworking and woodworking industries.
FAQs
What is Finite Element Analysis (FEA)?
Finite Element Analysis (FEA) is a computerized method for predicting how a product reacts to real-world forces, vibration, heat, fluid flow, and other physical effects. It is commonly used in engineering to simulate the behavior of mechanical parts and systems.
How do CNC manufacturers use FEA in building a 2×72 grinder?
CNC manufacturers use FEA to analyze the structural integrity, thermal performance, and vibration characteristics of the 2×72 grinder. This helps them optimize the design, material selection, and manufacturing process to ensure the grinder meets performance and safety requirements.
What are the benefits of using FEA in building a 2×72 grinder?
Using FEA allows CNC manufacturers to identify potential design flaws, optimize the performance of the grinder, reduce material and manufacturing costs, and minimize the risk of failure or malfunction.
What are the key considerations when using FEA in building a 2×72 grinder?
Key considerations when using FEA in building a 2×72 grinder include accurately modeling the grinder’s geometry, material properties, and operating conditions, as well as validating the FEA results through physical testing and analysis.
How does FEA contribute to building a better 2×72 grinder?
FEA contributes to building a better 2×72 grinder by enabling CNC manufacturers to optimize the grinder’s design, performance, and reliability, leading to a more efficient and durable product.