Grinder maintenance is a critical aspect of ensuring the longevity and efficiency of your grinding equipment. Whether you are operating a small workshop or a large manufacturing facility, the performance of your grinder directly impacts the quality of your work. Regular maintenance not only enhances the machine’s operational capabilities but also minimizes the risk of unexpected breakdowns that can lead to costly downtime.
Understanding the fundamentals of grinder maintenance is essential for anyone involved in machining or metalworking. In this article, we will explore various facets of grinder maintenance, from the importance of regular upkeep to specific tasks that should be performed to keep your equipment in optimal condition. By adhering to a structured maintenance routine, you can ensure that your grinder operates smoothly and efficiently, ultimately contributing to better productivity and output quality.
Key Takeaways
- Regular maintenance is crucial for the proper functioning of grinders and to ensure longevity.
- Safety precautions must be followed during maintenance to prevent accidents and injuries.
- Cleaning and lubricating the grinder regularly can prevent wear and tear and extend its lifespan.
- Belts, pulleys, and other components should be inspected for any signs of damage or wear.
- Blades should be sharpened or replaced as needed, and tension should be checked and adjusted for optimal performance.
Importance of Regular Maintenance
Regular maintenance is paramount for any piece of machinery, and grinders are no exception. Over time, wear and tear can lead to diminished performance, which can affect the precision and quality of the grinding process. By implementing a consistent maintenance schedule, operators can identify potential issues before they escalate into significant problems.
This proactive approach not only extends the lifespan of the grinder but also enhances its overall performance. Moreover, regular maintenance can lead to cost savings in the long run. By preventing major breakdowns and ensuring that all components are functioning correctly, businesses can avoid expensive repairs and replacements.
Additionally, a well-maintained grinder operates more efficiently, which can result in lower energy consumption and reduced operational costs. Therefore, investing time and resources into regular maintenance is not just beneficial; it is essential for maintaining a competitive edge in the industry.
Safety Precautions for Maintenance
Before embarking on any maintenance tasks, it is crucial to prioritize safety. Grinders are powerful machines that can pose significant risks if not handled properly. Operators should always wear appropriate personal protective equipment (PPE), including safety goggles, gloves, and ear protection.
These precautions help mitigate the risk of injury from flying debris or accidental contact with moving parts. Furthermore, it is essential to disconnect the grinder from its power source before performing any maintenance work. This simple step can prevent accidental startups that could lead to serious injuries.
Additionally, operators should familiarize themselves with the machine’s manual and adhere to all safety guidelines provided by the manufacturer. By cultivating a culture of safety during maintenance activities, operators can protect themselves and their colleagues while ensuring that the grinder remains in good working order.
Cleaning and Lubrication
Cleaning and lubrication are fundamental components of grinder maintenance that should not be overlooked. Dust, debris, and metal shavings can accumulate on and around the grinder, potentially affecting its performance and leading to premature wear. Regular cleaning helps maintain a clean working environment and ensures that the machine operates efficiently.
Operators should use appropriate cleaning agents and tools to remove buildup without damaging any components. Lubrication is equally important for maintaining the grinder’s functionality. Proper lubrication reduces friction between moving parts, which can help prevent overheating and wear.
It is essential to use the correct type of lubricant as specified by the manufacturer. Regularly checking and replenishing lubrication levels will ensure that all moving parts operate smoothly, contributing to the overall efficiency of the grinder.
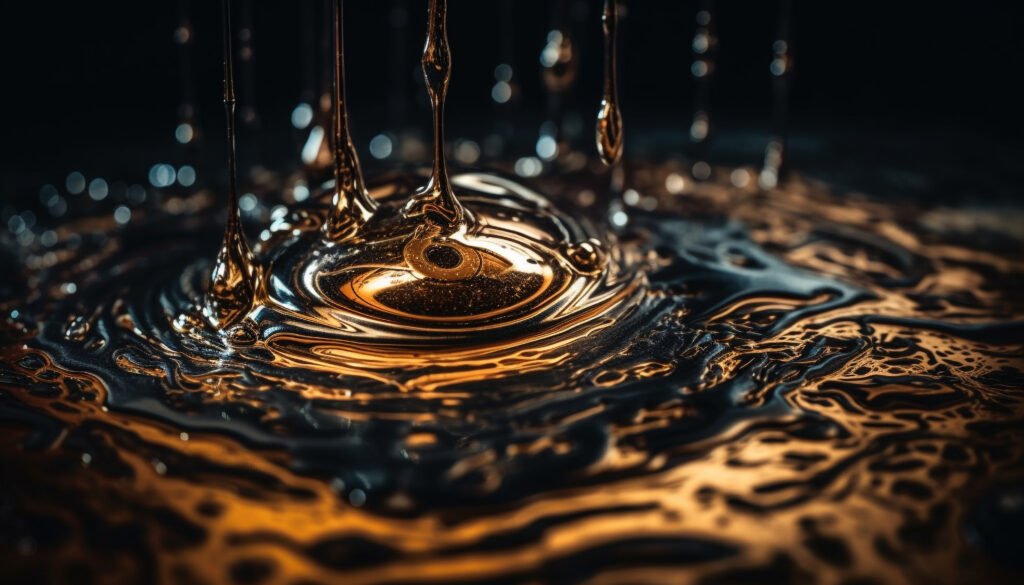
Inspection of Belts and Pulleys
The belts and pulleys of a grinder play a crucial role in its operation, as they transfer power from the motor to the grinding wheel. Regular inspection of these components is vital to ensure they are in good condition. Operators should look for signs of wear, such as fraying or cracking in belts, as well as any misalignment or damage to pulleys.
Addressing these issues promptly can prevent further damage and maintain optimal performance. In addition to visual inspections, it is advisable to check the tension of the belts regularly. A belt that is too loose may slip, while one that is too tight can cause excessive wear on both the belt and the motor.
Adjusting belt tension according to manufacturer specifications will help ensure that power is transmitted efficiently, allowing for consistent grinding results.
Checking for Loose or Damaged Parts
Another critical aspect of grinder maintenance involves checking for loose or damaged parts. Over time, vibrations from operation can cause screws, bolts, and other fasteners to loosen. Regularly inspecting these components helps ensure that everything is securely fastened, which is essential for safe operation.
Loose parts can lead to misalignment or even catastrophic failure if not addressed promptly. In addition to fasteners, operators should also inspect other components for signs of damage or wear. This includes checking for cracks in the housing or any other structural elements that could compromise the integrity of the machine.
Identifying and replacing damaged parts early on can prevent more extensive repairs down the line and keep the grinder running smoothly.
Sharpening and Replacing Blades
The blades of a grinder are critical for achieving precise results in grinding operations. Over time, blades can become dull or damaged due to regular use, which can negatively impact performance and quality. Regularly sharpening blades is essential for maintaining their effectiveness; dull blades require more force to achieve the same results, leading to increased wear on both the blades and the machine itself.
When sharpening is no longer sufficient to restore blade performance, replacement becomes necessary. Operators should be familiar with how to properly replace blades according to manufacturer guidelines. Using high-quality replacement blades ensures that the grinder continues to perform at its best while producing high-quality results.
Checking and Adjusting Tension
Tension plays a vital role in the operation of a grinder, particularly concerning belts and chains that drive various components. Proper tension ensures that power is transmitted effectively without causing undue stress on any part of the machine. Regularly checking tension levels is essential for maintaining optimal performance; too much tension can lead to excessive wear, while too little can result in slippage.
Adjusting tension should be done according to manufacturer specifications, as each machine may have different requirements. Operators should familiarize themselves with these specifications and make adjustments as needed during routine maintenance checks. By ensuring proper tension levels, operators can enhance both efficiency and safety during grinding operations.
Inspecting Electrical Components
Electrical components are integral to the operation of modern grinders, making their inspection a crucial part of maintenance routines. Regularly checking wiring, connections, and electrical panels helps identify potential issues before they escalate into serious problems. Loose connections or frayed wires can lead to electrical failures or even pose fire hazards if not addressed promptly.
In addition to visual inspections, operators should also test electrical components for functionality. This includes checking switches, relays, and circuit breakers to ensure they are operating correctly. By maintaining a close eye on electrical systems, operators can prevent unexpected downtime caused by electrical failures and ensure that their grinders operate safely and efficiently.
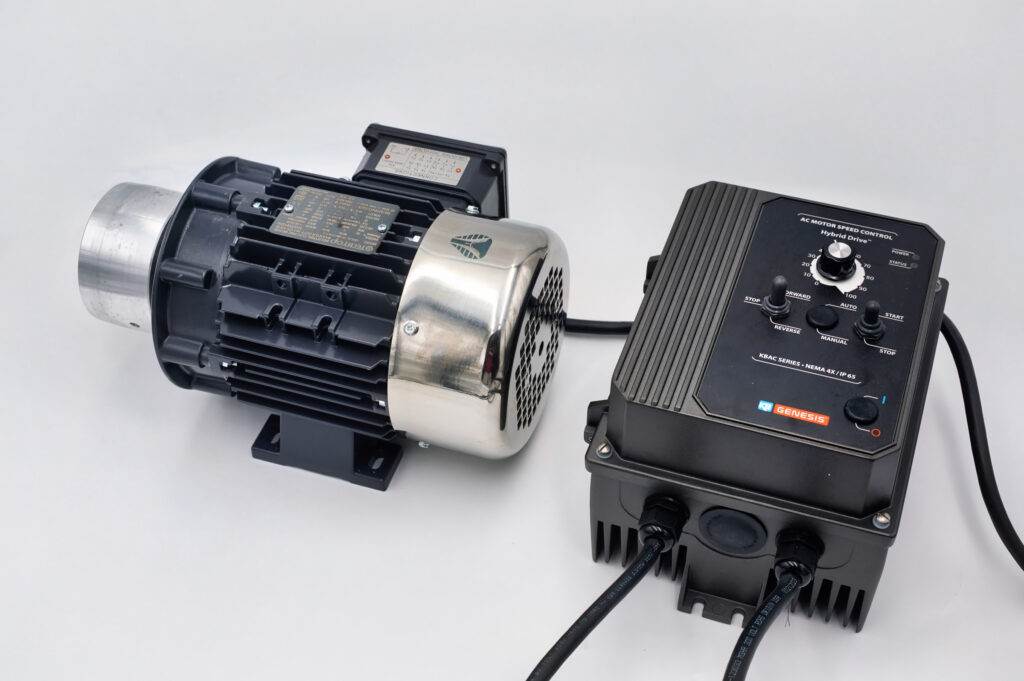
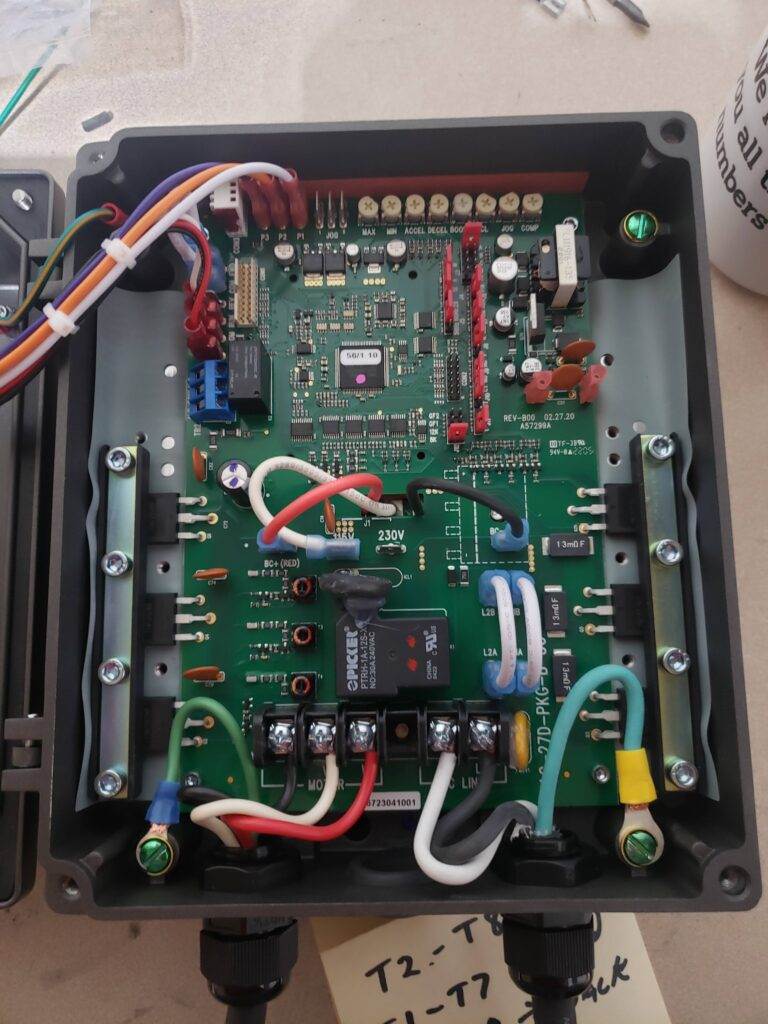
Testing and Calibrating Controls
The controls of a grinder are essential for achieving precise results during operation. Regular testing and calibration of these controls help ensure that they function correctly and provide accurate readings. Operators should familiarize themselves with how to test each control feature according to manufacturer guidelines.
Calibration may involve adjusting settings based on specific parameters or using specialized tools to verify accuracy. By regularly testing and calibrating controls, operators can maintain consistent performance levels while ensuring that their grinding processes meet quality standards.
Final Checks and Test Run
After completing all maintenance tasks, it is essential to conduct final checks before putting the grinder back into operation. This includes reviewing all adjustments made during maintenance, ensuring that all components are securely fastened, and confirming that lubrication levels are adequate. A thorough final inspection helps catch any oversights that may have occurred during maintenance.
Once all checks are complete, performing a test run is crucial for verifying that everything is functioning correctly. During this test run, operators should monitor for any unusual noises or vibrations that may indicate underlying issues. If everything operates smoothly during this test run, the grinder is ready for use once again, ensuring optimal performance for future grinding tasks.
In conclusion, regular maintenance of grinders is essential for ensuring their longevity and efficiency in various applications. By adhering to a structured maintenance routine that includes cleaning, lubrication, inspection of components, sharpening blades, checking tension levels, inspecting electrical systems, testing controls, and conducting final checks, operators can keep their grinders in peak condition. This proactive approach not only enhances productivity but also contributes to a safer working environment while minimizing unexpected downtime due to equipment failure.
FAQs
What is a grinder maintenance schedule?
A grinder maintenance schedule is a set of regular checks and tasks that need to be performed on a grinder to ensure it is operating efficiently and safely.
Why is it important to have a grinder maintenance schedule?
Having a grinder maintenance schedule is important to prevent unexpected breakdowns, reduce the risk of accidents, and prolong the lifespan of the grinder.
What should be checked every 50 hours in a grinder maintenance schedule?
Some of the things that should be checked every 50 hours in a grinder maintenance schedule include inspecting the grinder’s belts, checking for any loose or damaged parts, and lubricating moving parts.
How can a grinder maintenance schedule help in preventing accidents?
A grinder maintenance schedule can help prevent accidents by ensuring that all safety features are in working order, and that any potential hazards are identified and addressed promptly.
What are the consequences of not following a grinder maintenance schedule?
Not following a grinder maintenance schedule can lead to increased risk of accidents, decreased efficiency, and costly repairs or replacements due to premature wear and tear.
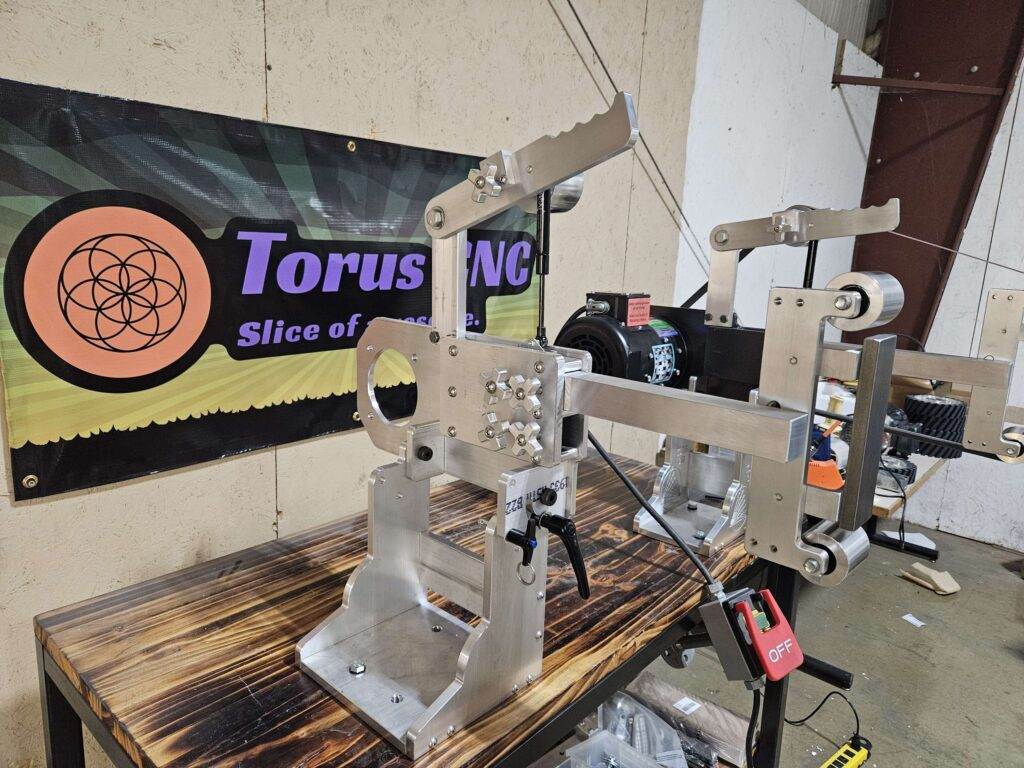