In the realm of manufacturing, particularly in the production of tools and machinery, consistency is paramount. CNC (Computer Numerical Control) technology has revolutionized the way products are designed and manufactured, allowing for precision and repeatability that manual processes simply cannot achieve. For companies like TorusCNC, which specializes in 2×72 grinders, maintaining a high level of consistency is essential not only for product quality but also for customer satisfaction.
When a customer invests in a 2×72 grinder, they expect it to perform reliably and deliver the same results every time. This expectation places a significant responsibility on manufacturers to ensure that each unit produced meets stringent quality standards. Moreover, consistency in CNC machining leads to reduced waste and increased efficiency.
When machines operate with precision, the likelihood of errors diminishes, resulting in fewer defective products and less material waste. This efficiency translates into cost savings for manufacturers and ultimately benefits consumers through competitive pricing. In the context of TorusCNC, achieving consistency means that each 2×72 grinder produced is not only a reflection of the company’s commitment to quality but also a testament to the advanced technology and skilled craftsmanship that goes into every machine.
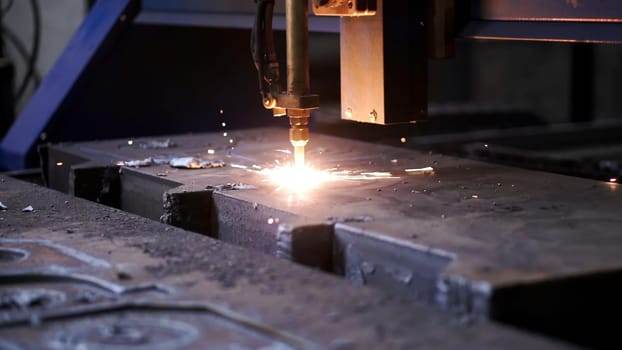
Key Takeaways
- Consistency in CNC machining is crucial for producing high-quality 2×72 grinders.
- The right CNC machine for 2×72 grinders should offer precision and reliability.
- Quality control measures are essential for ensuring consistent reproduction with CNC machines.
- CAD/CAM software can greatly improve precision and accuracy in reproducing 2×72 grinders.
- Uniformity in material selection is key to maintaining quality in 2×72 grinder production.
Choosing the Right CNC Machine for 2×72 Grinders
Selecting the appropriate CNC machine is a critical step in the production process of 2×72 grinders. The choice of machinery directly impacts the quality, efficiency, and overall output of the manufacturing process. For TorusCNC, this means evaluating various factors such as machine capabilities, tooling options, and software compatibility.
A well-chosen CNC machine can significantly enhance production capabilities, allowing for intricate designs and precise cuts that are essential for high-performance grinders. Additionally, the right CNC machine should be versatile enough to accommodate different materials and designs. The 2×72 grinder requires specific tolerances and finishes that can only be achieved with advanced machinery.
TorusCNC must consider machines that offer robust features such as high-speed spindles, multi-axis capabilities, and advanced cooling systems. These features not only improve the quality of the final product but also streamline the manufacturing process, enabling faster turnaround times without compromising on precision.
Implementing Quality Control Measures for CNC Reproduction
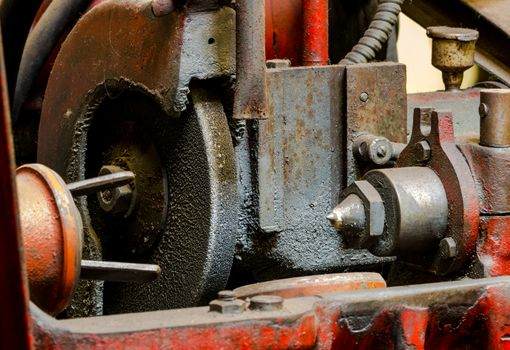
Quality control is an integral part of the CNC manufacturing process, especially when producing specialized equipment like 2×72 grinders. Implementing rigorous quality control measures ensures that each grinder meets the established specifications and performance standards. For TorusCNC, this involves a systematic approach to monitoring every stage of production, from initial design to final assembly.
Regular inspections and testing are crucial to identify any deviations from quality standards early in the process. Moreover, employing statistical process control (SPC) techniques can help TorusCNC track production metrics and identify trends that may indicate potential issues. By analyzing data collected during production, the company can make informed decisions about adjustments needed to maintain quality.
This proactive approach not only enhances product reliability but also fosters a culture of continuous improvement within the organization.
Utilizing CAD/CAM Software for Precision Reproduction
Metrics | Results |
---|---|
Accuracy | 0.001mm |
Time Savings | 30% |
Material Waste Reduction | 25% |
Production Efficiency | 40% |
The integration of CAD (Computer-Aided Design) and CAM (Computer-Aided Manufacturing) software is essential for achieving precision in CNC reproduction. For TorusCNC, utilizing advanced CAD/CAM software allows for detailed design modeling and efficient programming of CNC machines. This technology enables designers to create intricate designs for 2×72 grinders that can be easily translated into machine instructions, ensuring that every detail is captured accurately.
Furthermore, CAD/CAM software facilitates rapid prototyping and testing, allowing TorusCNC to refine designs before full-scale production begins. This iterative process helps identify potential design flaws early on, reducing the risk of costly errors during manufacturing. By leveraging these software tools, TorusCNC can enhance its production capabilities while maintaining a high level of precision and quality in its 2×72 grinders.
Ensuring Uniformity in Material Selection for 2×72 Grinders
Material selection plays a crucial role in the performance and durability of 2×72 grinders. For TorusCNC, ensuring uniformity in material selection is vital to producing high-quality products that meet customer expectations. The choice of materials affects not only the grinder’s performance but also its longevity and resistance to wear and tear.
Therefore, it is essential to establish strict guidelines for material sourcing and testing. By working closely with trusted suppliers and conducting thorough material evaluations, TorusCNC can ensure that only the best materials are used in its grinders. This uniformity in material selection contributes to consistent performance across all units produced.
Additionally, implementing standardized testing procedures for incoming materials helps identify any inconsistencies or defects before they enter the production line, further enhancing product quality.
Fine-tuning CNC Parameters for Reproducing 2×72 Grinders
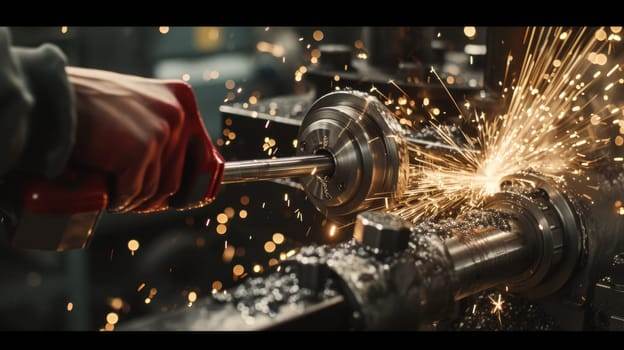
Fine-tuning CNC parameters is a critical aspect of achieving optimal performance in the production of 2×72 grinders. Each machine has specific settings that must be adjusted based on factors such as material type, thickness, and desired finish. For TorusCNC, this means carefully calibrating feed rates, spindle speeds, and tool paths to ensure that each grinder is produced with precision and efficiency.
Moreover, continuous monitoring of CNC parameters during production allows for real-time adjustments that can enhance output quality. By analyzing performance data and making necessary tweaks to machine settings, TorusCNC can maintain consistency across all units produced. This attention to detail not only improves product quality but also contributes to overall operational efficiency.
Training and Skill Development for CNC Operators
The success of any CNC manufacturing operation hinges on the skills and expertise of its operators. For TorusCNC, investing in training and skill development for CNC operators is essential to maintaining high standards of quality and efficiency in the production of 2×72 grinders. Comprehensive training programs should cover not only machine operation but also troubleshooting techniques and best practices for quality control.
Furthermore, fostering a culture of continuous learning encourages operators to stay updated on the latest advancements in CNC technology and manufacturing processes. By providing opportunities for professional development, TorusCNC can ensure that its workforce remains skilled and knowledgeable, ultimately leading to improved product quality and operational performance.
Monitoring and Adjusting CNC Processes for Continuous Improvement
Continuous improvement is a fundamental principle in modern manufacturing practices, particularly in CNC operations. For TorusCNC, monitoring and adjusting CNC processes is crucial to enhancing productivity and product quality over time. By implementing performance metrics and regularly reviewing production data, the company can identify areas for improvement and make informed decisions about process adjustments.
Additionally, fostering an environment where feedback from operators is valued can lead to innovative solutions for optimizing CNC processes. Encouraging open communication allows team members to share insights based on their experiences, which can lead to significant improvements in efficiency and product quality. By embracing a culture of continuous improvement, TorusCNC can ensure that its 2×72 grinders remain at the forefront of industry standards while meeting the evolving needs of its customers.
FAQs
What is quality control at scale?
Quality control at scale refers to the process of ensuring consistent quality and standards across a large volume of products or components. It involves implementing systems and processes to monitor and maintain quality at every stage of production.
What are 2×72 grinders?
2×72 grinders are industrial-grade belt grinders commonly used in metalworking and fabrication. They are designed for precision grinding, shaping, and finishing of metal components.
What is CNC consistency?
CNC consistency refers to the use of computer numerical control (CNC) technology to ensure precise and consistent manufacturing processes. CNC machines are programmed to perform tasks with a high level of accuracy and repeatability.
How is quality control at scale applied to reproducing 2×72 grinders?
Quality control at scale in reproducing 2×72 grinders involves implementing standardized production processes, rigorous testing and inspection procedures, and utilizing CNC technology to ensure consistent and precise manufacturing of each grinder.
Why is quality control at scale important in manufacturing 2×72 grinders?
Quality control at scale is important in manufacturing 2×72 grinders to ensure that each grinder meets the required specifications, performance standards, and safety regulations. Consistent quality control also helps to build trust with customers and maintain a strong reputation in the industry.