Belt direction plays a crucial role in the efficiency and effectiveness of various manufacturing processes, particularly in CNC machining and material handling. The orientation of the belt can significantly influence how materials are transported, processed, and ultimately finished. When the belt direction is aligned correctly with the intended workflow, it can enhance productivity, reduce waste, and improve the overall quality of the final product.
Conversely, an incorrect belt direction can lead to complications such as material jams, uneven wear on machinery, and subpar results. Moreover, understanding belt direction is not merely about the physical movement of materials; it also encompasses the dynamics of how forces interact during processing. For instance, the direction in which a belt moves can affect the gravitational pull on materials, influencing their stability and positioning.
This understanding is essential for operators and engineers alike, as it allows them to optimize their setups for maximum efficiency and minimal disruption.
Key Takeaways
- Belt direction plays a crucial role in material throw and overall conveyor performance
- Factors such as material type, speed, and conveyor design can affect material throw
- The ideal belt direction should be determined based on material characteristics and conveyor setup
- Different materials may require adjustments in belt direction for optimal performance
- Tips for optimizing material throw include regular maintenance, proper tensioning, and using the right conveyor accessories
Factors Affecting Material Throw
Material throw is influenced by several factors, including the speed of the belt, the type of material being processed, and the angle of inclination. The speed at which a belt operates can dramatically affect how materials are projected or thrown off during processing. A faster belt may lead to increased centrifugal force, which can cause lighter materials to be ejected more forcefully than intended.
Conversely, a slower belt may not provide enough momentum for materials to reach their desired destination effectively. The type of material being handled also plays a significant role in determining how it behaves on the belt. For example, heavier materials may require a different approach compared to lighter ones.
Additionally, the surface texture of the belt can impact friction levels, which in turn affects how materials are thrown. Understanding these factors is essential for operators to make informed decisions about belt direction and speed settings.
Determining the Ideal Belt Direction
Determining the ideal belt direction involves analyzing the specific requirements of the manufacturing process and the characteristics of the materials being used. One effective method is to conduct a thorough assessment of the workflow to identify any potential bottlenecks or inefficiencies. By mapping out the entire process, operators can pinpoint where adjustments in belt direction may yield significant improvements.
Another critical aspect is to consider the end goal of the material handling process. For instance, if the objective is to transport materials to a specific location with minimal disruption, then aligning the belt direction accordingly becomes paramount. Operators should also take into account any machinery or equipment that interacts with the belt system, ensuring that all components work harmoniously together.
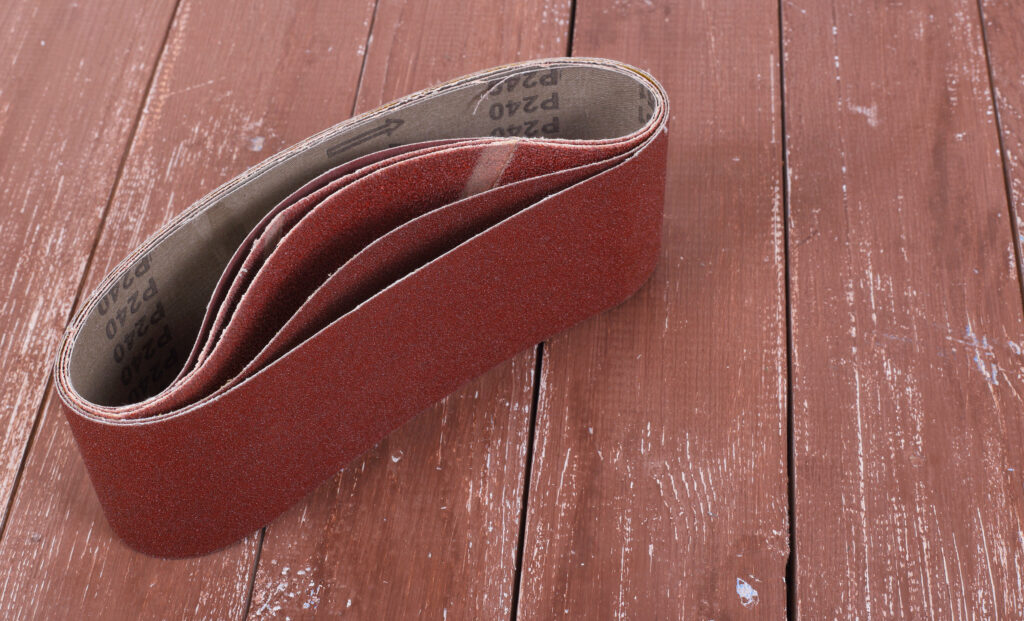
Adjusting Belt Direction for Different Materials
Adjusting belt direction for different materials requires a nuanced understanding of each material’s properties and behavior under various conditions. For instance, when working with granular materials like sand or gravel, a downward belt direction may be more effective in preventing spillage and ensuring consistent flow. On the other hand, when handling larger items such as metal sheets or wooden planks, a horizontal or upward direction might be necessary to facilitate easier loading and unloading.
Additionally, operators should consider environmental factors such as humidity and temperature, which can affect material consistency and behavior on the belt. For example, wet materials may stick to surfaces more readily, necessitating adjustments in both speed and direction to maintain optimal flow. By tailoring belt direction to suit specific materials and conditions, operators can enhance efficiency and reduce waste.
Tips for Optimizing Material Throw
To optimize material throw effectively, operators should focus on several key strategies. First and foremost, maintaining an appropriate speed is essential. Operators should experiment with different speeds to find the sweet spot that maximizes material throw without causing excessive wear on equipment or risking material loss.
Regular monitoring and adjustments based on real-time observations can lead to significant improvements in performance. Another important tip is to ensure that the belt surface is clean and free from debris. Accumulated dirt or residue can create friction that alters how materials behave on the belt.
Regular maintenance checks should be conducted to keep belts in optimal condition. Additionally, using belts with appropriate surface textures can enhance grip and control over material movement, further optimizing throw dynamics.
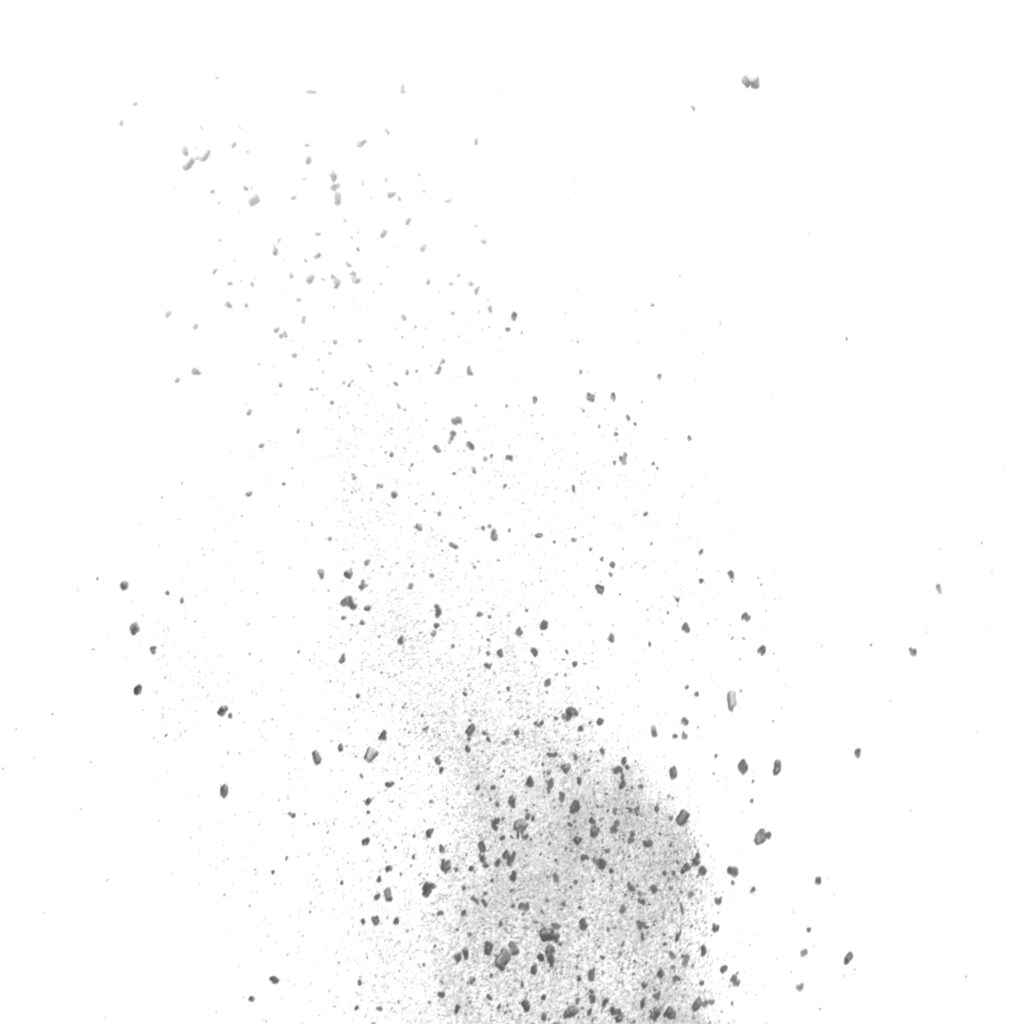
Common Mistakes in Setting Belt Direction
Setting belt direction is not without its pitfalls; several common mistakes can hinder performance and lead to inefficiencies. One prevalent error is failing to account for material characteristics when determining belt direction. Operators may assume that all materials behave similarly, leading to miscalculations that result in jams or improper handling.
Another mistake involves neglecting to adjust for changes in environmental conditions. Factors such as temperature fluctuations or humidity levels can significantly impact material behavior on belts. Operators who do not regularly reassess their settings may find themselves facing unexpected challenges that could have been easily mitigated with proactive adjustments.
Tools and Equipment for Adjusting Belt Direction
To effectively adjust belt direction, operators need access to specialized tools and equipment designed for precision and ease of use. One essential tool is a belt tension gauge, which helps ensure that belts are properly tensioned for optimal performance. Incorrect tension can lead to slippage or excessive wear, making it vital for operators to monitor this aspect regularly.
Additionally, adjustable pulleys and rollers can facilitate quick changes in belt direction as needed. These components allow for fine-tuning of angles and positions without requiring extensive downtime or reconfiguration of entire systems. Investing in high-quality tools not only enhances efficiency but also contributes to longer equipment lifespan.
Safety Considerations when Changing Belt Direction
Safety should always be a top priority when changing belt direction or making adjustments to machinery. Operators must ensure that all equipment is powered down before making any modifications to prevent accidental injuries. Additionally, wearing appropriate personal protective equipment (PPE) such as gloves and safety goggles is essential during these processes.
Furthermore, it is crucial to communicate clearly with team members when making adjustments. Establishing a protocol for signaling when changes are being made can help prevent accidents and ensure that everyone is aware of ongoing operations. Regular safety training sessions can also reinforce best practices and keep safety at the forefront of daily operations.
Benefits of Properly Setting Belt Direction
Properly setting belt direction offers numerous benefits that extend beyond mere efficiency gains. One significant advantage is improved product quality; when materials are handled correctly throughout the manufacturing process, there is a lower likelihood of defects or inconsistencies in the final output. This not only enhances customer satisfaction but also strengthens brand reputation.
Additionally, optimizing belt direction can lead to cost savings over time. By reducing waste and minimizing equipment wear, companies can lower operational costs while maximizing productivity. Furthermore, a well-optimized system often requires less maintenance intervention, allowing teams to focus on other critical areas of production.
Case Studies: Successful Applications of Optimized Belt Direction
Several industries have successfully implemented optimized belt direction strategies with remarkable results. In one case study involving a large-scale food processing plant, adjustments in belt direction led to a 20% increase in throughput while simultaneously reducing material spillage by 15%. This improvement not only enhanced operational efficiency but also contributed to significant cost savings over time.
Another example comes from an automotive manufacturing facility where optimizing belt direction reduced cycle times by 30%. By carefully analyzing workflow patterns and adjusting belt orientations accordingly, the facility was able to streamline operations while maintaining high-quality standards in production.
Future Trends in Belt Direction Technology
As technology continues to evolve, so too does the potential for advancements in belt direction systems. One emerging trend is the integration of smart sensors that monitor material flow in real-time. These sensors can provide valuable data on how materials behave under different conditions, allowing operators to make informed adjustments dynamically.
Additionally, advancements in automation are likely to play a significant role in future belt direction technologies. Automated systems equipped with machine learning algorithms could analyze historical data to predict optimal settings based on specific material types and environmental conditions. This level of sophistication could revolutionize how industries approach material handling and processing in the years to come.
In conclusion, understanding and optimizing belt direction is essential for enhancing efficiency and productivity across various manufacturing processes. By considering factors such as material characteristics, environmental conditions, and employing appropriate tools and safety measures, operators can significantly improve their operations while minimizing risks and costs associated with improper handling techniques. As technology continues to advance, embracing these changes will be crucial for staying competitive in an ever-evolving landscape.
FAQs
What is the purpose of setting belt direction for optimal material throw?
Setting the belt direction for optimal material throw helps to ensure that the material being conveyed is thrown in the desired direction, maximizing efficiency and reducing the risk of material spillage.
How does setting belt direction affect material throw?
The direction of the belt can impact the trajectory and distance at which the material is thrown. By setting the belt direction appropriately, the material can be directed to the desired location with precision.
What factors should be considered when setting belt direction for optimal material throw?
When setting the belt direction, factors such as the type and size of the material being conveyed, the speed of the conveyor belt, and the desired trajectory of the material should be taken into consideration.
What are the benefits of setting belt direction for optimal material throw?
Setting the belt direction for optimal material throw can result in improved efficiency, reduced material spillage, and better control over the material handling process. This can ultimately lead to cost savings and a safer working environment.
How can the belt direction be adjusted for optimal material throw?
The belt direction can be adjusted by changing the orientation of the conveyor pulleys or by using a reversible conveyor belt system. It is important to follow the manufacturer’s guidelines and safety procedures when making adjustments.
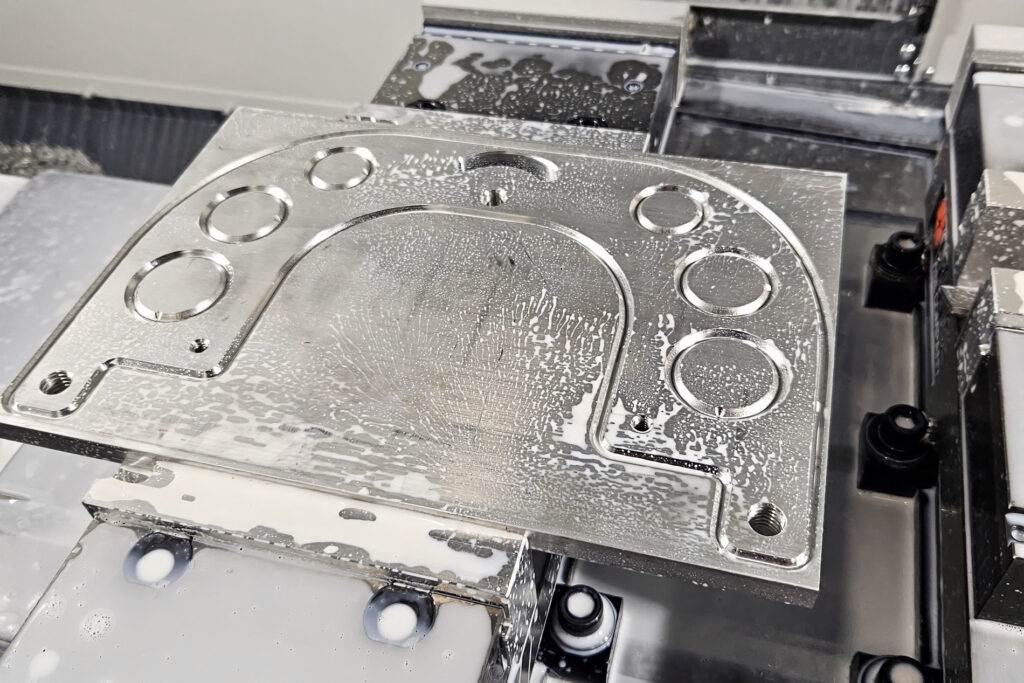