In the realm of construction and manufacturing, the choice of materials plays a pivotal role in determining the overall performance and suitability of a product. Among the most popular options are aluminum frames and steel tube frames, each offering distinct advantages and disadvantages. Aluminum frames are renowned for their lightweight properties and resistance to corrosion, making them an ideal choice for applications where weight savings are critical.
On the other hand, steel tube frames are celebrated for their strength and durability, often preferred in situations where structural integrity is paramount. The decision between aluminum and steel tube frames often hinges on the specific requirements of a project. For instance, industries such as automotive and aerospace frequently lean towards aluminum due to its favorable strength-to-weight ratio.
Conversely, sectors that demand robust structural support, such as construction and heavy machinery, may opt for steel tube frames. Understanding the characteristics of these materials is essential for making informed choices that align with project goals and operational needs.
Key Takeaways
- Aluminum frames are lightweight and resistant to corrosion, while steel tube frames are heavier but offer greater strength and durability.
- The cost of materials for aluminum frames is generally higher than steel tube frames, but the manufacturing process for aluminum is more cost-effective.
- Aluminum frames have a longer lifespan and require less maintenance compared to steel tube frames, which may be prone to rust and corrosion.
- Aluminum frames are lighter and easier to transport, resulting in lower transportation costs compared to steel tube frames.
- Maintenance and repair costs for aluminum frames are generally lower due to their resistance to corrosion, while steel tube frames may require more frequent maintenance and repairs.
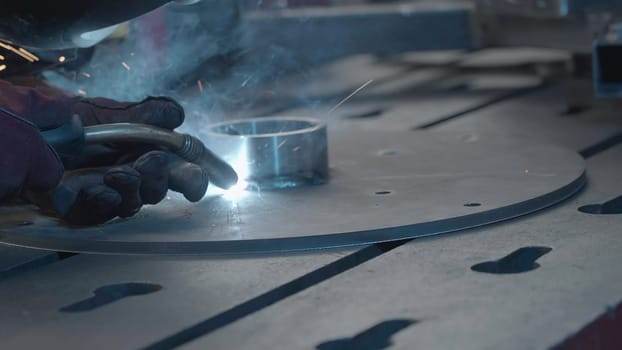
Cost of Materials and Manufacturing Process
When evaluating aluminum frames versus steel tube frames, one of the most significant factors to consider is the cost of materials and the manufacturing process involved. Aluminum, while lightweight and resistant to corrosion, tends to be more expensive than steel. The price of aluminum can fluctuate based on market demand and availability, which can impact overall project budgets.
Additionally, the manufacturing process for aluminum often requires specialized techniques such as extrusion or casting, which can further increase production costs. In contrast, steel is generally more affordable and widely available, making it a cost-effective option for many applications. The manufacturing process for steel tube frames typically involves welding or bending, which can be less complex than aluminum fabrication.
This simplicity can lead to lower labor costs and faster production times. However, it is essential to weigh these cost considerations against the specific performance requirements of a project, as the initial investment may be offset by long-term benefits in durability and maintenance.
Durability is a critical factor when comparing aluminum frames to steel tube frames. Aluminum is naturally resistant to rust and corrosion, which makes it an excellent choice for environments exposed to moisture or harsh weather conditions. This inherent resistance allows aluminum frames to maintain their structural integrity over time, often resulting in a longer lifespan with minimal degradation.
However, while aluminum is durable in terms of corrosion resistance, it may not withstand heavy impacts as well as steel. Steel tube frames, on the other hand, are known for their exceptional strength and ability to bear heavy loads. This makes them particularly suitable for applications requiring high structural integrity, such as bridges or industrial buildings.
However, steel is susceptible to rust if not properly treated or maintained, which can compromise its longevity. To mitigate this risk, protective coatings or galvanization processes are often employed. Ultimately, the choice between aluminum and steel will depend on the specific demands of the application and the environmental conditions they will face.
Weight and Transportation Costs

The weight of a material significantly influences transportation costs and logistics in any project. Aluminum frames are considerably lighter than their steel counterparts, which can lead to substantial savings in shipping costs and ease of handling during installation. This lightweight nature allows for more efficient transportation methods and can reduce fuel consumption during transit.
Additionally, lighter materials can simplify the design of supporting structures, potentially lowering overall project costs. Conversely, steel tube frames are heavier, which can increase transportation expenses and complicate logistics. The added weight may require more robust handling equipment during installation, potentially leading to higher labor costs.
However, the strength of steel can sometimes offset these transportation challenges by allowing for fewer structural supports in certain applications. Ultimately, when considering weight and transportation costs, it is crucial to evaluate how these factors align with the overall project budget and timeline.
Maintenance and Repair Costs
Year | Total Maintenance Cost | Total Repair Cost |
---|---|---|
2018 | 5000 | 3000 |
2019 | 5500 | 3200 |
2020 | 6000 | 3500 |
Maintenance and repair costs are vital considerations when choosing between aluminum frames and steel tube frames. Aluminum’s resistance to corrosion means that it typically requires less maintenance over its lifespan compared to steel. This characteristic can lead to lower long-term costs associated with upkeep and repairs.
In environments where exposure to moisture or chemicals is prevalent, aluminum’s durability can significantly reduce the frequency of maintenance interventions. In contrast, steel tube frames may incur higher maintenance costs due to their susceptibility to rust and corrosion if not adequately protected. Regular inspections and maintenance routines are essential to ensure that steel structures remain safe and functional over time.
While protective coatings can extend the life of steel frames, they may require periodic reapplication, adding to overall maintenance expenses. Therefore, when evaluating maintenance considerations, it is essential to factor in both the initial costs of materials and the long-term implications for upkeep.
Environmental Impact and Sustainability
The environmental impact of materials used in construction is becoming increasingly important in today’s eco-conscious society. Aluminum is often touted as a more sustainable option due to its recyclability; it can be recycled indefinitely without losing its properties. The recycling process for aluminum requires significantly less energy compared to producing new aluminum from raw materials, making it an environmentally friendly choice for many applications.
Steel also has recycling benefits; however, its production process can be more energy-intensive than that of aluminum. The extraction and processing of iron ore into steel contribute to higher carbon emissions compared to aluminum production. Nevertheless, advancements in technology are helping to reduce the environmental footprint of steel manufacturing.
When considering sustainability, it is essential to evaluate not only the material’s recyclability but also the entire lifecycle impact from production through disposal.
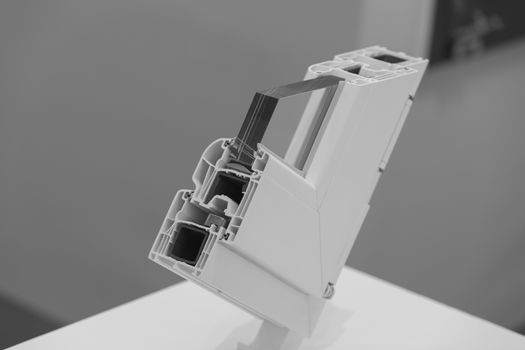
Customization and Design Options

Customization plays a crucial role in selecting between aluminum frames and steel tube frames for various applications. Aluminum offers greater flexibility in design due to its malleability and ease of fabrication. This allows manufacturers to create intricate shapes and designs that may be challenging with steel.
The ability to produce lightweight yet complex structures makes aluminum an attractive option for industries such as aerospace and automotive design. Steel tube frames also offer customization options but may be limited by their rigidity compared to aluminum. However, steel’s strength allows for larger spans without additional supports, which can be advantageous in certain architectural designs.
Both materials can be finished with various coatings or treatments to enhance aesthetics or functionality, providing further opportunities for customization. Ultimately, the choice between aluminum and steel will depend on the specific design requirements and desired outcomes of a project.
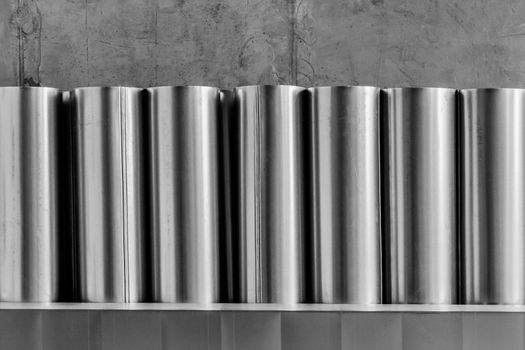
Making an Informed Decision
In conclusion, the decision between aluminum frames and steel tube frames involves a careful consideration of various factors including cost, durability, weight, maintenance requirements, environmental impact, and customization options. Each material presents unique advantages that cater to different applications and project needs. Aluminum’s lightweight nature and corrosion resistance make it ideal for projects where weight savings are critical, while steel’s strength offers unparalleled durability for heavy-duty applications.
Ultimately, making an informed decision requires a thorough understanding of the specific requirements of a project alongside an evaluation of long-term implications such as maintenance costs and environmental sustainability. By weighing these factors carefully, stakeholders can select the material that best aligns with their goals while ensuring optimal performance throughout the lifecycle of their products or structures.
FAQs
What are the hidden costs of steel tube frames?
Steel tube frames may incur hidden costs such as maintenance, corrosion protection, and potential repairs due to rust and deterioration over time. Additionally, steel frames are heavier, leading to higher transportation and installation costs.
How do aluminum frames save you money long-term?
Aluminum frames are corrosion-resistant, requiring minimal maintenance and reducing the need for costly repairs. They are also lighter in weight, resulting in lower transportation and installation expenses. Furthermore, aluminum’s durability and longevity contribute to long-term cost savings.