Introduction to 2×72 Knife Grinders
Importance of a 2×72 Knife Grinder
The significance of a 2×72 knife grinder cannot be overstated in the world of knife making and metalworking. This versatile tool is a vital investment for both amateur craftsmen and seasoned professionals. Its design allows for enhanced control and precision in creating, sharpening, and finishing blades. One of the primary benefits of the 2×72 setup is its ability to accommodate various belt grits, making it a one-stop solution for multiple tasks. From rough grinding to intricate profiling, the adaptability of a 2×72 knife grinder stands out. Here are some key aspects that highlight its importance:
- Efficiency: The wide belt and powerful motor contribute to a quicker material removal rate, significantly speeding up the grinding process.
- Versatility: With the right attachments, these grinders can perform a multitude of functions beyond knife-making, including metal shaping and polishing.
- Precision: The flat platen, contact wheel, and adjustable speed settings allow for detailed work, ensuring high-quality results.
Ultimately, investing in a 2×72 knife grinder equips the user with a robust tool that enhances creativity while saving time.
Common Applications of 2×72 Knife Grinders
The versatility of 2×72 knife grinders extends across different domains, making them invaluable in various applications. Below are some of the most common uses:
- Knife Making: This remains the primary application, where makers use it to shape and sharpen blades to exact specifications. The precise adjustments yield exceptional edge quality, a critical factor for functionality and aesthetic appeal.
- Metal Fabrication: Beyond knives, these grinders are ideal for metal projects that require shaping and finishing, such as custom tools or hardware.
- Sanding and Finishing Work: Woodworkers and furniture makers leverage the grinder for sanding curved edges and surfaces, delivering smooth finishes that are often hard to achieve with traditional tools.
- Stock Removal: In larger fabrication projects, 2×72 grinders can swiftly remove stock from materials, leading to efficient workflow management on the shop floor.
- Hollow Grinding: For those focused on creating specific blade designs, hollow grinding becomes feasible with the use of contact wheels that help shape the blade’s profile.
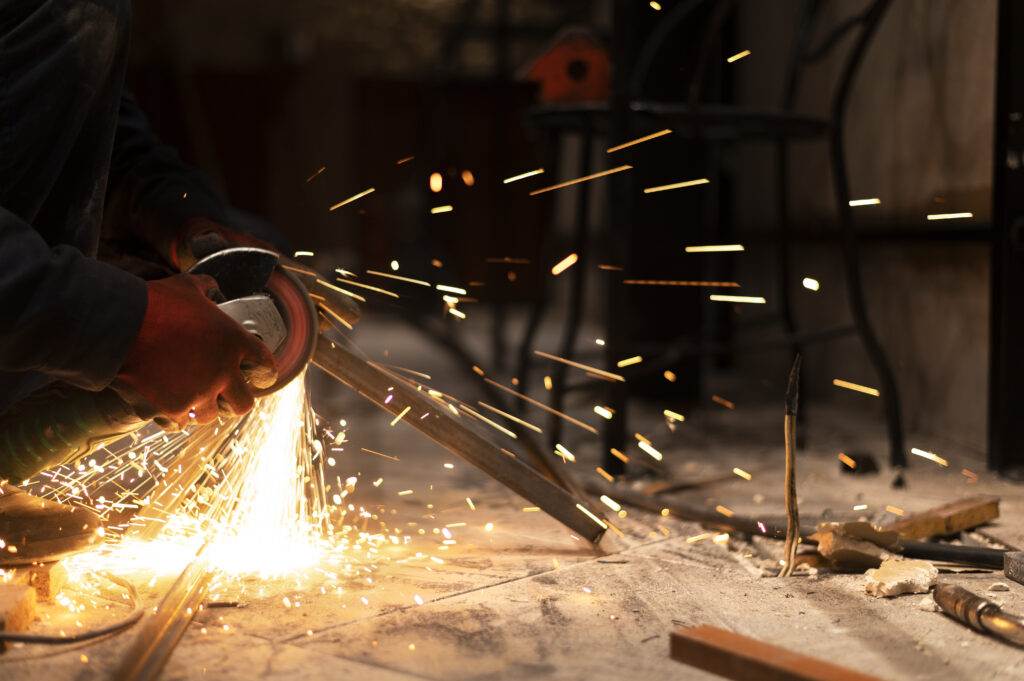
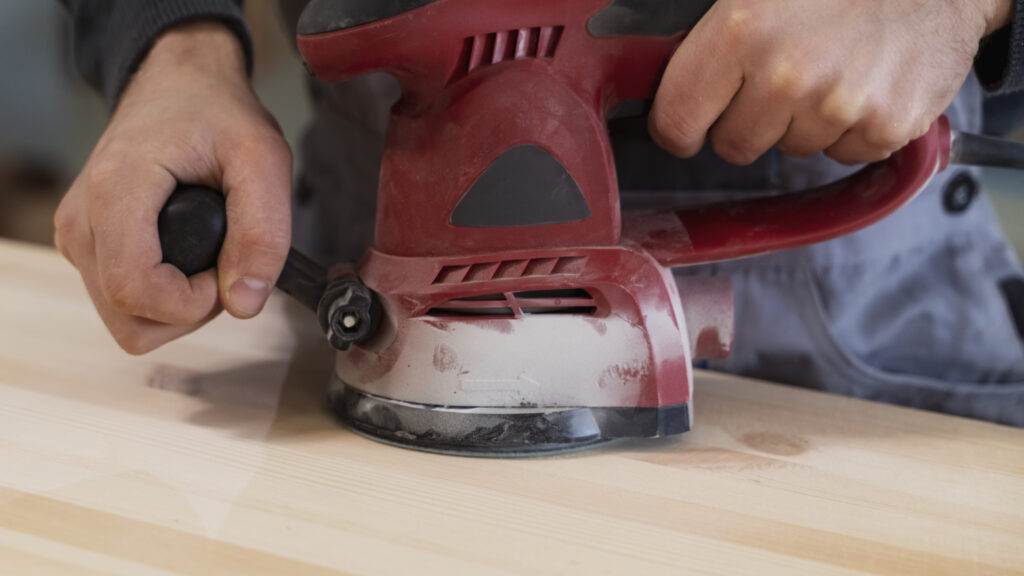
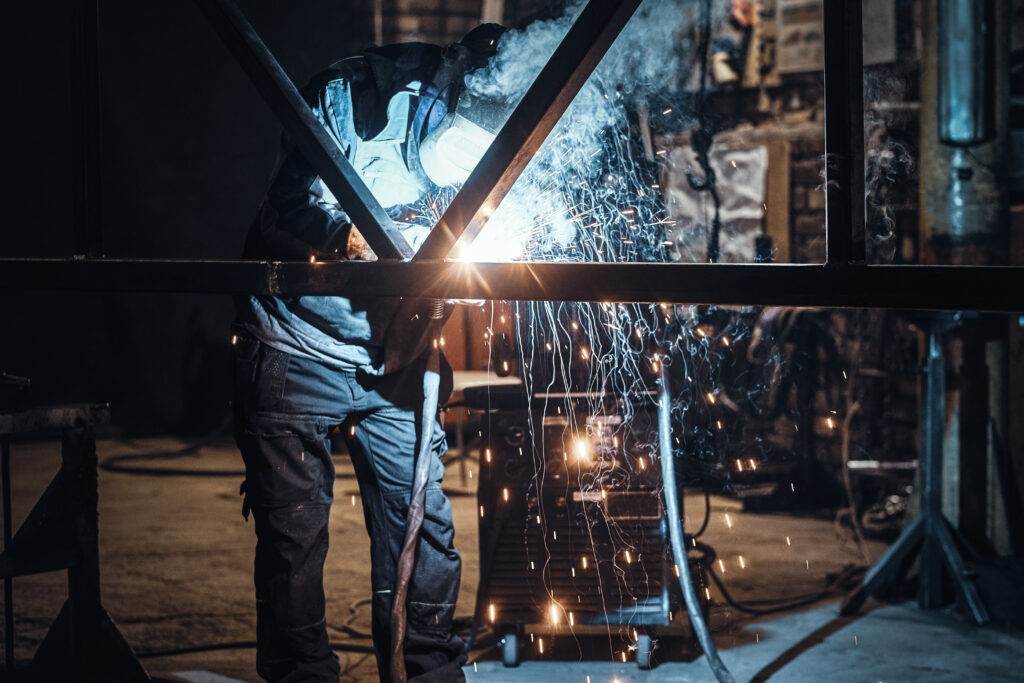
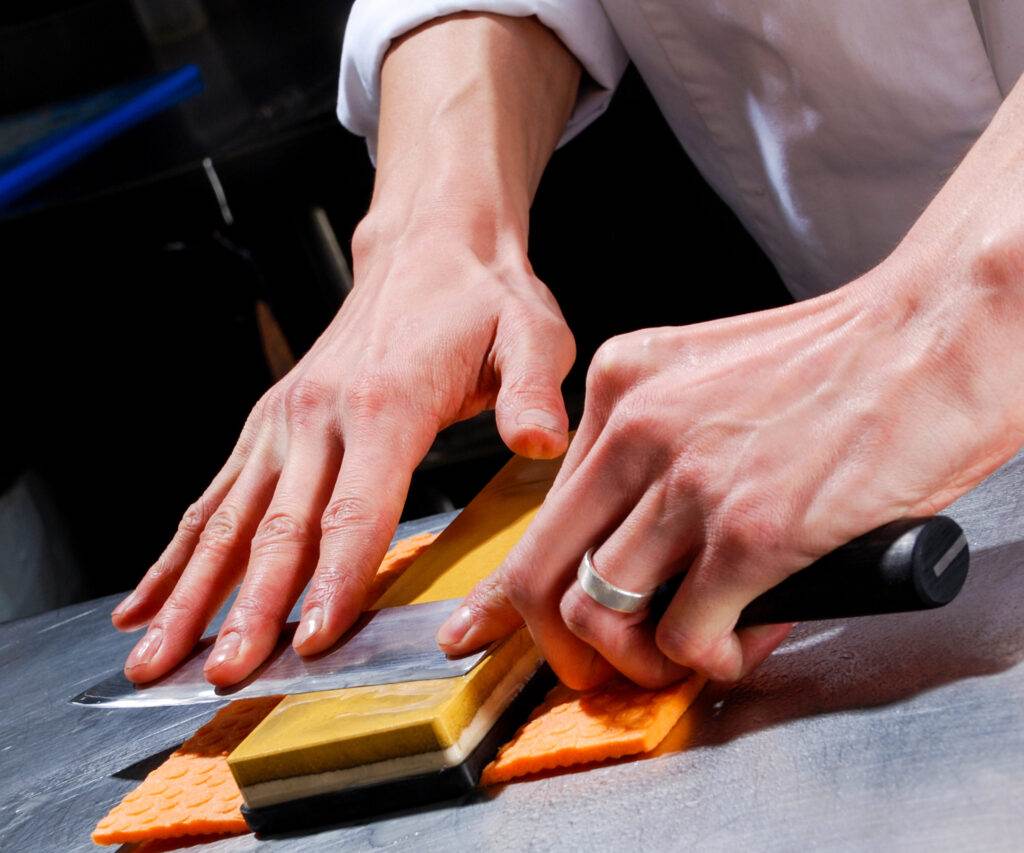
In summary, the 2×72 knife grinder is not just a utility for knife makers but a multifunctional tool that caters to a broad range of metalworking and woodworking needs. With its impressive capabilities, it demonstrates how a single piece of equipment can elevate the overall quality and efficiency of various trades. Ultimately, it is this adaptability that underscores its significance in modern workshops.
Motor Power and Speed Capabilities
Various Motor Options for 2×72 Knife Grinders
When selecting a 2×72 knife grinder, one of the first considerations is the type of motor it employs. The motor is the heart of the grinder, dictating its efficiency and effectiveness across different tasks. Here’s a look at the most common motor options available:
- Single Phase Motors: These are the most common and are suitable for home workshops. With power ratings ranging from 1 to 3 horsepower, they are adequate for general knife-making and light metal work.
- Three Phase Motors: Ideal for more intensive industrial use, three-phase motors boast higher horsepower ratings, typically between 3 and 10 horsepower. These provide continuous, sustained power, making them perfect for professional environments.
- Direct Drive Motors: As the name suggests, these motors connect directly to the grinding wheel without the need for pulleys or belts. This means less maintenance and increased efficiency in transferring power, but it might be harder to adjust the speed.
- Variable Speed Motors: The flexibility of variable speed motors allows users to adjust the motor speed based on the task at hand. This is particularly beneficial during different phases of knife making, as it can accommodate both aggressive grinding and gentle polishing.
Choosing the right motor involves understanding your work environment and the necessary power requirements. For hobbyists, a 1-2 HP motor usually suffices, while professionals and high-volume users might lean towards the 3 HP and above options.
Understanding Speed Settings of 2×72 Knife Grinders
Speed settings play a crucial role in how effectively a 2×72 knife grinder performs various tasks. Understanding these settings can provide craftsmen with the ability to achieve precise results tailored to their specific projects. Most 2×72 grinders feature adjustable speed settings, typically measured in surface feet per minute (SFPM). Here’s what you need to know:
- Low Speed (1,800-3,600 SFPM): Ideal for detailed grinding tasks and finishing work. At these lower speeds, the tool is less aggressive, allowing for more delicate operations without damaging the material.
- Medium Speed (4,000-6,000 SFPM): This range strikes a balance between aggressiveness and precision. It is useful for general knife shaping, where efficiency is required but damage must still be minimized.
- High Speed (7,000+ SFPM): High-speed settings are intended for rapid stock removal. While they significantly speed up the grinding process, caution is needed, as excessive heat can warp or alter the temper of the metal.
Many modern 2×72 grinders include features such as variable speed control, enabling users to transition smoothly between settings depending on the task. This flexibility can greatly enhance the overall quality of the finished product. In conclusion, understanding the motor power and speed settings available on a 2×72 knife grinder can significantly influence the effectiveness of your craftsmanship. By selecting the appropriate motor type and mastering the speed settings, you can ensure that your projects benefit from precision, efficiency, and adaptability. This ultimately leads to an improved quality of work and greater satisfaction in the result.
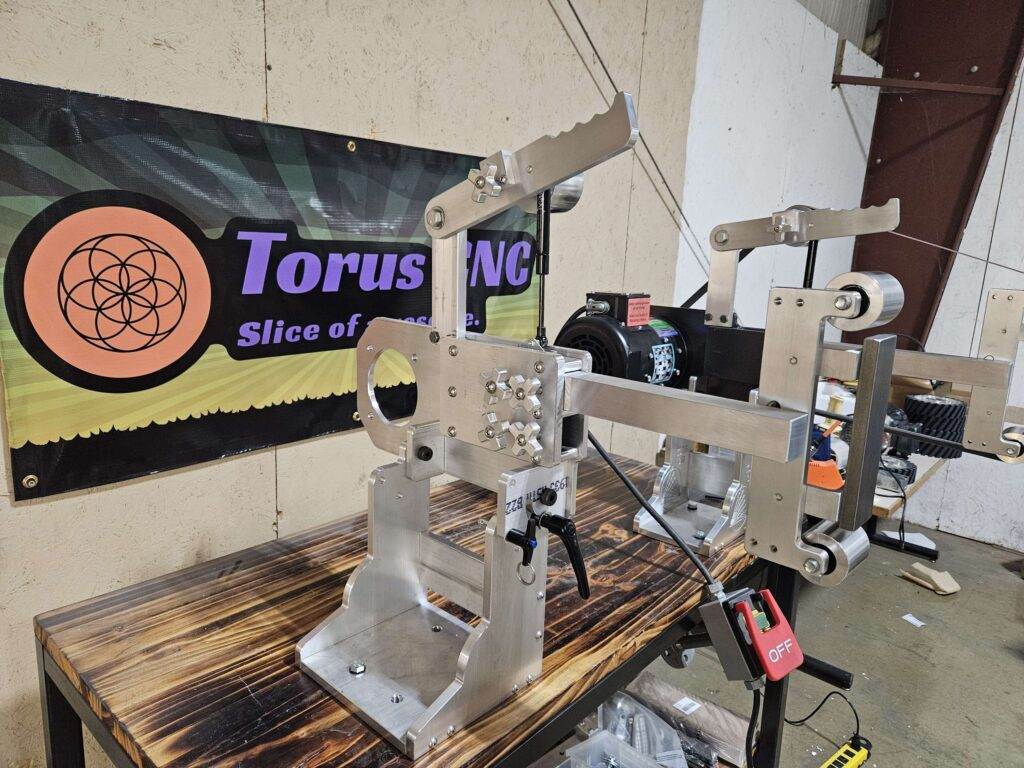
Belt Size and Compatibility
Different Belt Size Options Available
When working with a 2×72 knife grinder, one of the crucial attributes to consider is the belt size. The dimensions of the grinding belt directly influence the efficiency and capabilities of the tool. The most common belt size for these grinders is indeed 2 inches wide by 72 inches long, but there are several thickness and grit options to consider:
- Belt Thickness:
- Typically, belts come in varying thicknesses such as 1/16”, 1/8”, and even thicker options for specialized tasks. Thicker belts tend to offer more durability, making them ideal for heavy stock removal.
- Grit Options:
- Coarse Grit (36-80): Perfect for initial shaping and rapid material removal, coarse grit belts are the go-to for removing large amounts of material quickly.
- Medium Grit (120-240): These belts are ideal for general grinding and smoothing out the surface post rough grinding.
- Fine Grit (400 and above): Used for polishing and achieving a mirror-like finish, fine grit belts are essential for the final touches on blades.
Having a variety of belt sizes and grits on hand allows you to switch gears quickly and efficiently depending on your task, whether it’s rough shaping or finishing a blade to perfection.
Factors to Consider for Belt Compatibility
Selecting the correct belt for your 2×72 knife grinder is not solely about size; compatibility is vital to ensure optimal performance. Here are several factors to take into account:
- Belt Material:
- Different materials are designed for various applications. For instance, ceramic belts provide excellent heat resistance, making them suitable for high-output grinding tasks. Conversely, aluminum oxide belts are more common for general-purpose grinding due to their versatility and affordability.
- Joining Method:
- Most belts are either butt-jointed or overlapped. Butt-jointed belts tend to fit snugly around pulleys and are less prone to damage during use. Overlapped belts, while effective, may create a bump that can affect your grinding finish.
- Belt Speed Compatibility:
- Different belts have varying tolerances for speed. Higher speed settings can lead to increased heat, which may affect the longevity of some belts. Always check the manufacturer’s specifications for optimal speed ratings.
- Pulley Width:
- Ensure that your grinder has the correct pulley width to accommodate the belt size you choose, as insufficient width can lead to misalignment and premature wear.
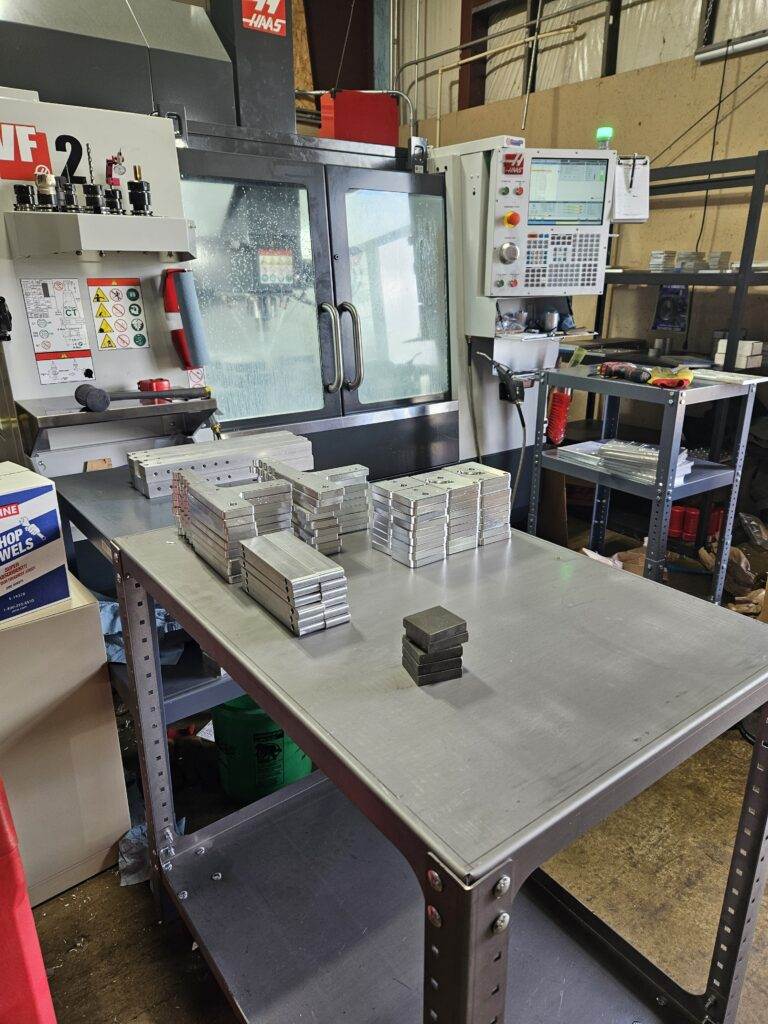
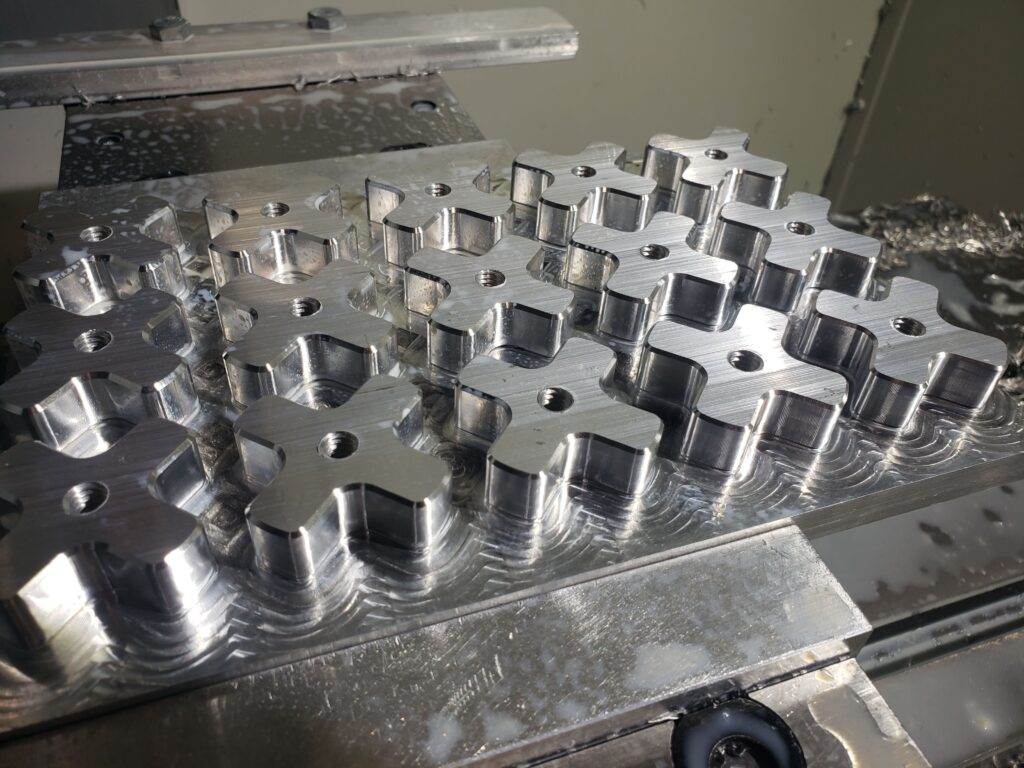
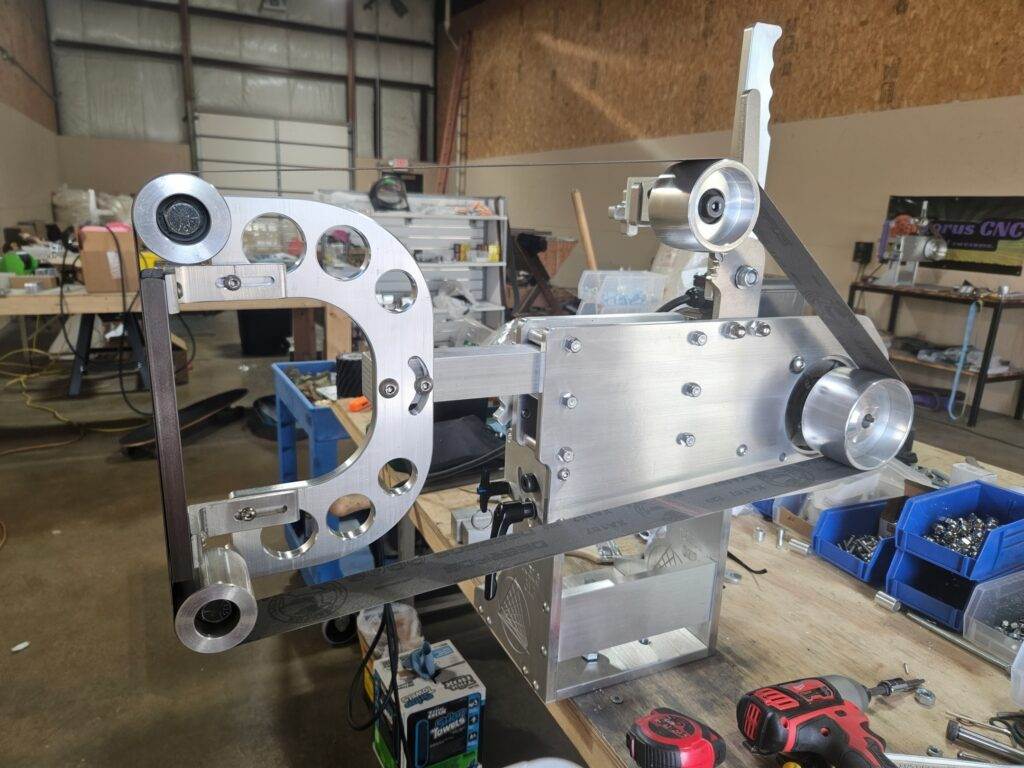
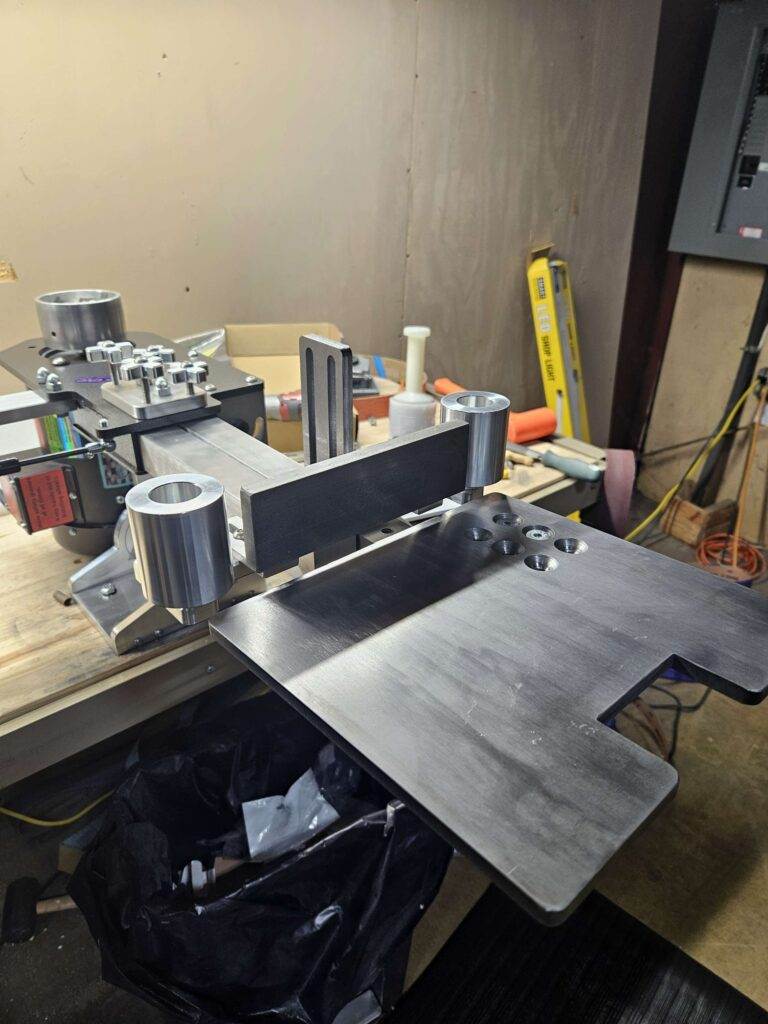
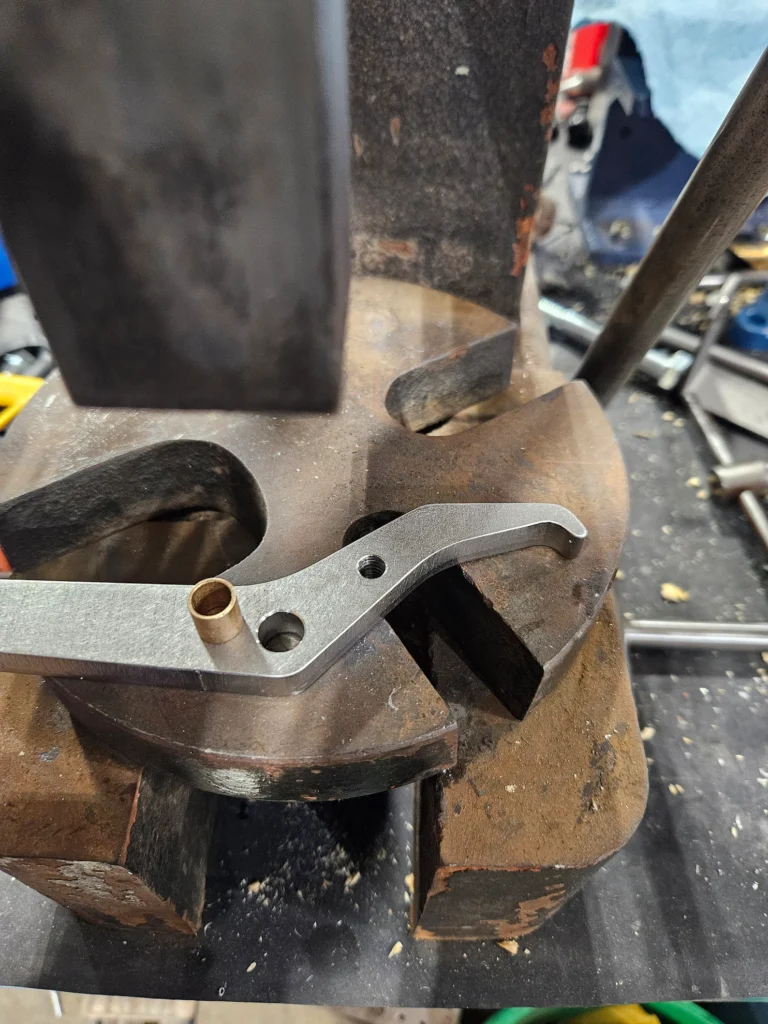
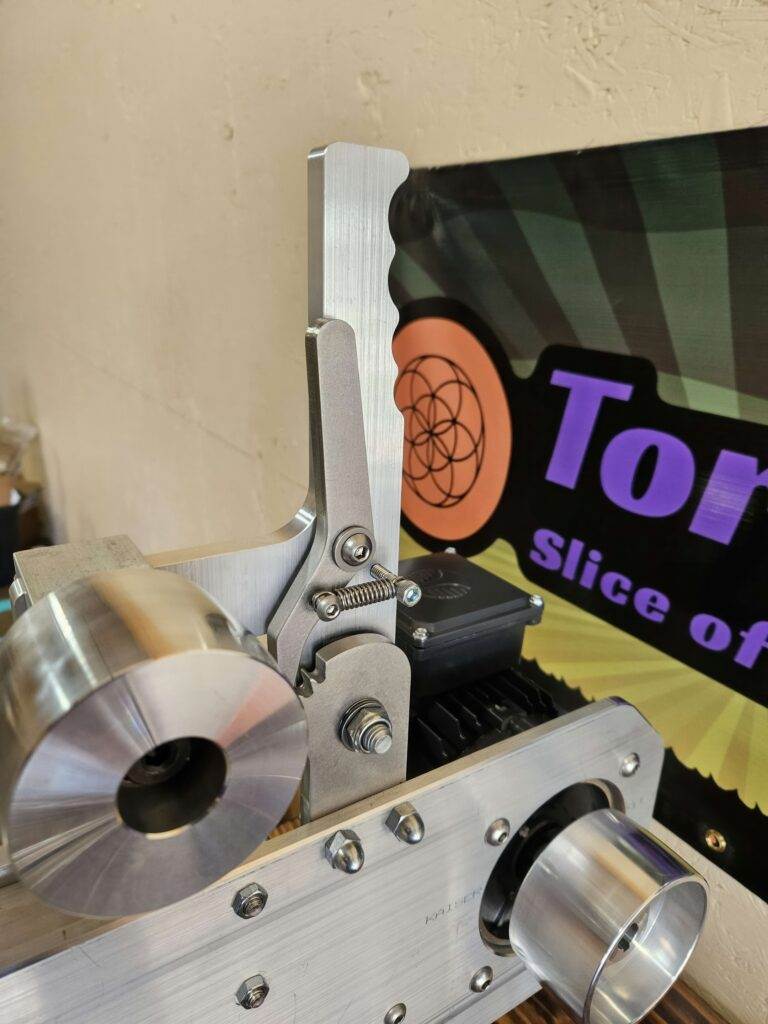
By paying careful attention to these factors, you can ensure that you select the most suitable belts for your grinder, maximizing both efficiency and output quality. In summary, understanding the different belt size options available and the factors that impact belt compatibility will help enhance your 2×72 knife grinder’s performance. A thoughtful selection of belts can lead to better results, making the grinding process not only more effective but also more enjoyable. Whether you’re crafting a new knife or refreshing an old favorite, the right belts make all the difference.
Construction Materials and Durability
Importance of Sturdy Construction
In the world of knife making and metalworking, the construction materials used in tools like the 2×72 knife grinder are crucial to their performance and longevity. Sturdy construction not only impacts the grinder’s durability but also its effectiveness in handling various tasks. A well-constructed grinder can withstand heavy use without compromising precision or leading to premature wear. Here are several reasons why sturdy construction is essential:
- Vibration Reduction: High-quality materials minimize vibration during operation. This is important, as excessive vibration can affect the grinding process, lead to inaccurate results, and even cause operator fatigue over time.
- Heat Resistance: Grinding generates heat, and a well-built grinder will resist warping or damage from heat exposure. A machine that can effectively dissipate heat is crucial for maintaining blade temper and ensuring longevity.
- User Safety: A durable grinder is more rigid and stable, which enhances the safety of the user. A wobbly or poorly constructed machine increases the risk of accidents and injuries.
- Long-Term Investment: While sturdy grinders may come with a higher initial cost, they tend to require less maintenance and replacement parts over time, making them more cost-effective in the long run.
Choosing a grinder built for durability pays off. Not only does it improve the quality of work, but it also enhances the overall experience of crafting custom blades.
Common Materials used in High-Quality Knife Grinders
When shopping for a 2×72 knife grinder, it’s vital to understand the materials used in its construction. Several materials are commonly found in high-quality grinders:
- Steel:
- Most commonly used for the frame, steel offers a robust structure that can handle substantial stress and offers long-lasting durability.
- Some grinders also feature carbon steel components that resist wear during grinding, giving the user reliability.
- Aluminum:
- Lightweight and corrosion-resistant, aluminum is sometimes used for parts where weight reduction is advantageous, such as on the motor mount or certain framework elements.
- Its excellent heat dissipation properties make aluminum a smart choice for specific applications in 2×72 grinders.
- Cast Iron:
- Known for its incredible stability and weight, cast iron is often used for the bases of grinder models. This material absorbs vibrations effectively, allowing for smoother operation during grinding tasks.
- However, due to its weight, cast iron can make the grinder more cumbersome to move.
- Rubber and Composite Materials:
- Used for feet or isolation mounts, these materials help further reduce vibrations. This isolation contributes to a more stable and accurate grinding process.
- Plastic or Nylon Components:
- Found in various non-load-bearing parts, high-grade plastics and nylon help keep the weight down while providing sufficient structural integrity.
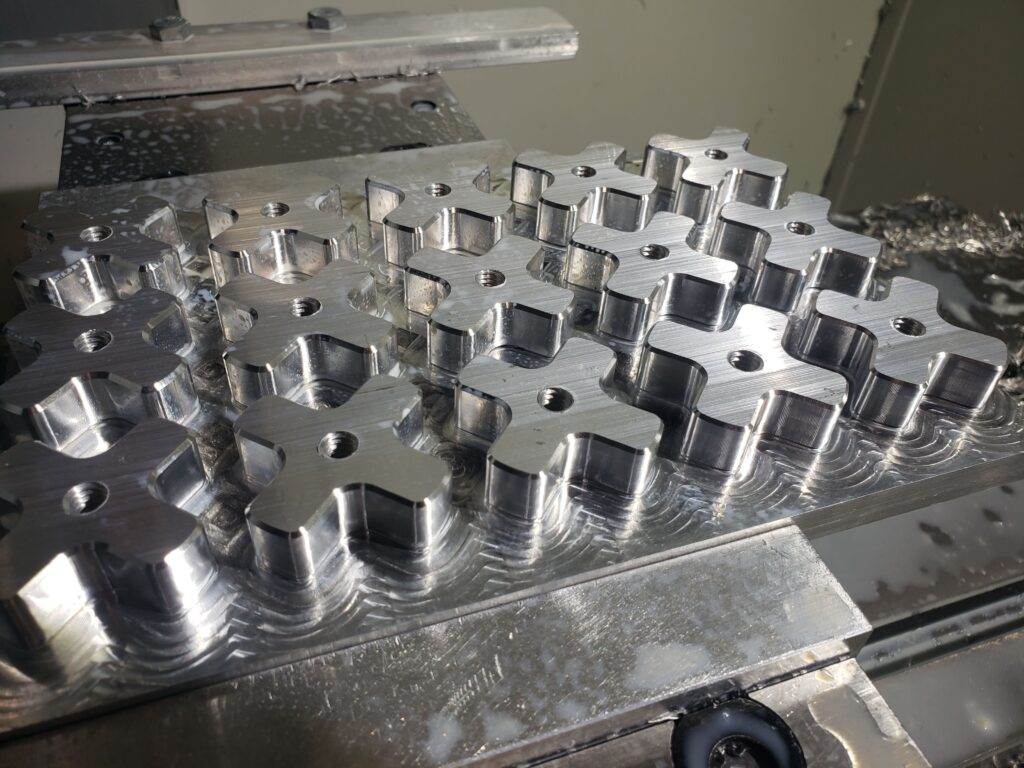
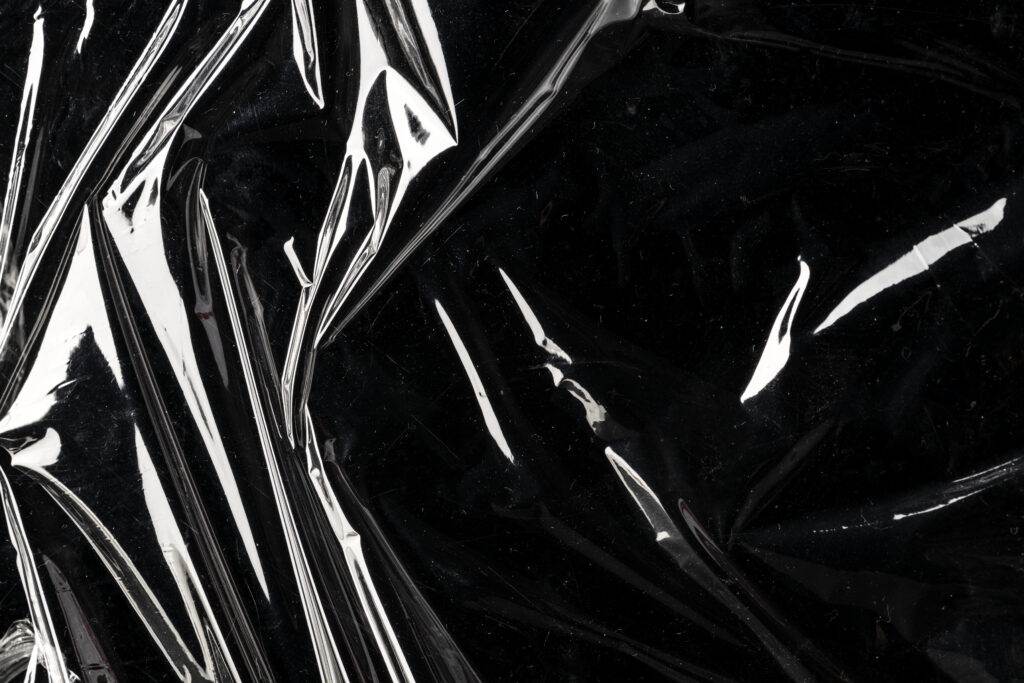
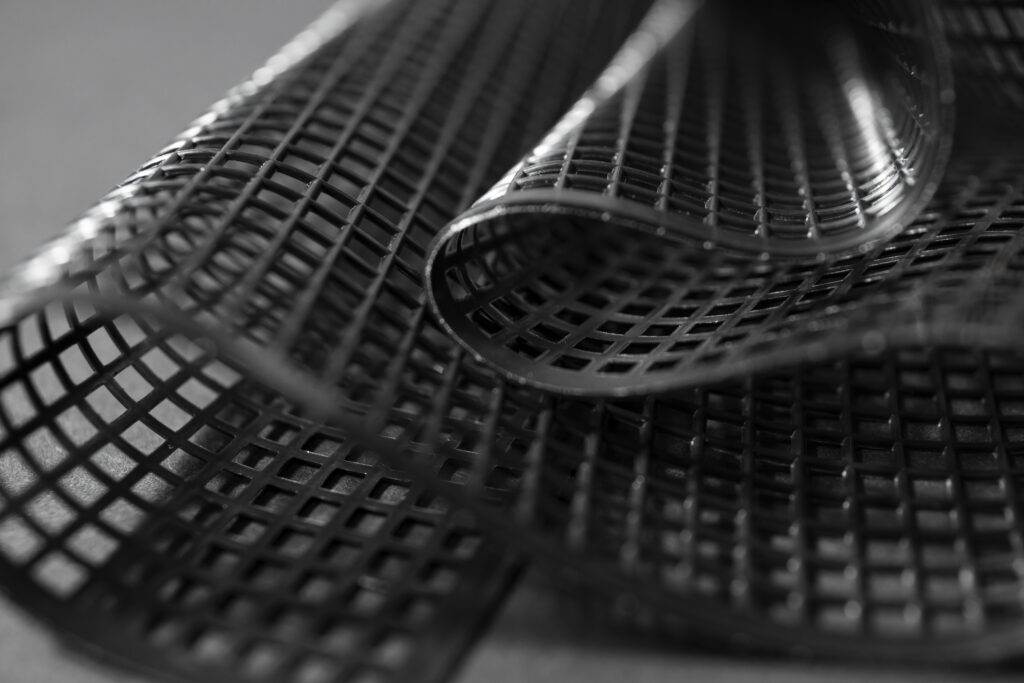
Understanding the materials used in constructing a 2×72 knife grinder helps buyers make informed decisions. By opting for a well-built machine made from quality materials, they can enhance their craftsmanship and ensure that their tools withstand the test of time. A durable grinder not only improves the quality of the work but also enhances the overall experience of honing one’s skills in the art of blade making.
Additional Features and Accessories
Variable Speed Control Features
When it comes to operating a 2×72 knife grinder, one of the standout features that many users appreciate is the variable speed control. Having the ability to adjust the speed of the grinder offers a multitude of benefits that can enhance both the ease of use and the quality of work. The significance of variable speed control lies in its adaptability. Depending on the task—whether it’s aggressive stock removal or delicate finishing work—different speeds are optimal. Here are some key advantages of variable speed features:
- Customization: Users can fine-tune the rate of grinding specific to the needs of the material. For instance, softer metals like aluminum can be ground at higher speeds without fear of damaging the material or altering its properties.
- Versatility: With adjustable speed, a single grinder can be employed for various applications, from shaping blades to polishing them to a mirror finish. This makes it a central tool for any metalworker.
- Increased Control: Slow speeds allow for intricate detail work, which is vital for a custom finish on knives. Meanwhile, higher speeds can accelerate the grinding process when working with tougher materials.
Many modern grinders feature digital displays that provide accurate speed settings, making it easy for users to select the preferred RPM. This capability not only maximizes efficiency but also enhances the overall craftsmanship, leading to better results.
Optional Attachments for Enhanced Functionality
To further augment the capabilities of a 2×72 knife grinder, various optional attachments can be incorporated, making the grinder even more versatile. These attachments enable users to tackle a wider range of tasks with greater efficiency. Below are some popular attachments worth considering:
- Contact Wheels:
- These wheels come in different diameters and curvature styles, making them perfect for hollow grinding and profiling blades. They help create distinct blade shapes with precision.
- Flat Platens:
- Ideal for flat grinding applications, flat platens help produce a consistent surface finish, ensuring accuracy in blade edges.
- Crown Wheels:
- These are designed for contouring and better handling of curve edges, allowing for creative blade designs while maintaining a secure grip on the material.
- Slack Belt Attachments:
- This modification allows for more flexible movement and access to hard-to-reach areas, particularly useful for shaping and finishing rounded blades.
- Dust Collection Systems:
- For the health-conscious craftsman, integrating a dust collection system helps manage the mess and keep the workspace clean, plummeting the risk of respiratory hazards from metal and particulate exposure.
- Variable Speed Controllers:
- While many grinders come equipped with speed controls, an upgraded external controller may offer more granularity, lifting the quality of the grinding process.
By opting for the right attachments, users can significantly enhance the functional potential of their 2×72 knife grinder. These features not only open up new possibilities for creativity and efficiency in projects but also boost overall satisfaction in the craftsmanship journey. Ultimately, the combination of variable speed control and specialized attachments transforms a 2×72 knife grinder into an indispensable asset in any workshop, enabling artisans to create exceptional work with impressive precision and ease.