CNC aluminum machining has revolutionized the way industries approach manufacturing and design. The term CNC stands for Computer Numerical Control, a technology that allows for precise and automated control of machine tools through computer programming. This method is particularly advantageous when working with aluminum, a lightweight yet durable metal that is widely used across various sectors.
The ability to create intricate designs and components with high accuracy makes CNC aluminum machining an essential process in modern manufacturing. Aluminum’s unique properties, such as its corrosion resistance, malleability, and excellent thermal conductivity, make it an ideal material for a multitude of applications. When combined with CNC technology, manufacturers can produce parts that not only meet stringent specifications but also enhance the overall functionality of the final product.
As industries continue to evolve, the demand for CNC aluminum components is expected to grow, driven by the need for efficiency, precision, and innovation.
Key Takeaways
- CNC aluminum is a versatile material used in various industries for its durability and precision.
- Sleek design of CNC aluminum offers benefits such as lightweight, corrosion resistance, and high strength-to-weight ratio.
- CNC aluminum is practically used in aerospace, automotive, medical, and electronics industries for its high precision and reliability.
- The professional appearance of CNC aluminum makes it a popular choice for high-end products and components.
- The manufacturing process of CNC aluminum involves computer-controlled machines to cut and shape the material with high accuracy and efficiency.
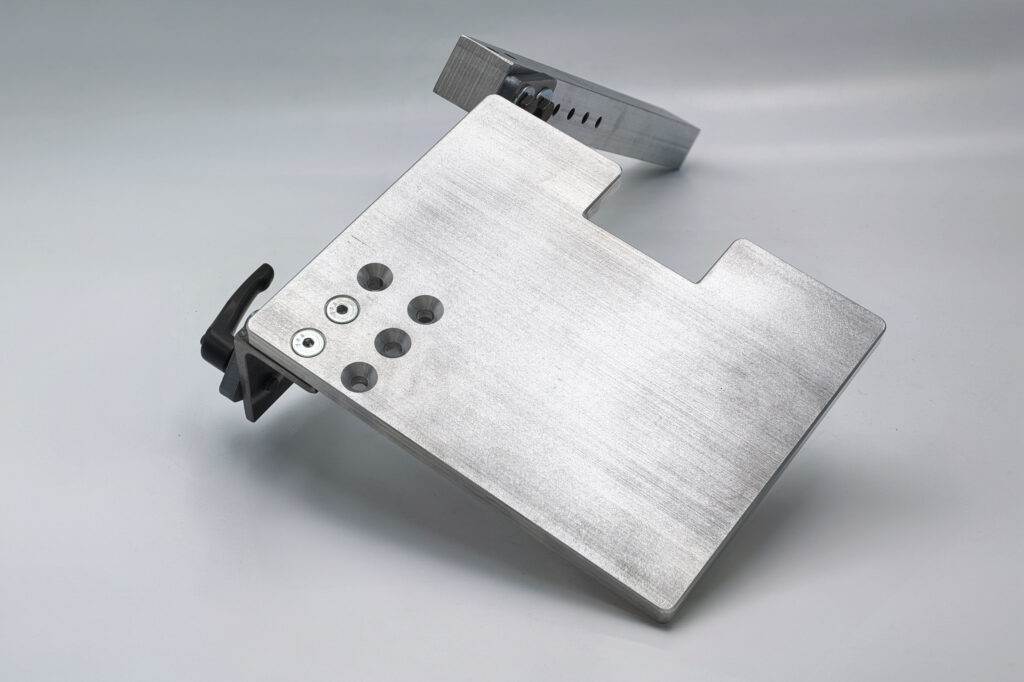
The Benefits of Sleek Design
One of the most significant advantages of CNC aluminum machining is the ability to achieve a sleek and modern design. The precision offered by CNC technology allows for the creation of complex geometries and smooth finishes that are often unattainable through traditional manufacturing methods. This capability is particularly important in industries where aesthetics play a crucial role, such as automotive, aerospace, and consumer electronics.
A well-designed aluminum component not only enhances the visual appeal of a product but also contributes to its overall performance. Moreover, the lightweight nature of aluminum complements its sleek design. Products made from CNC aluminum can be both visually striking and functional, providing manufacturers with the opportunity to create items that are easy to handle without compromising strength.
This balance between form and function is essential in today’s competitive market, where consumers are increasingly looking for products that are not only effective but also stylish. The seamless integration of design and engineering in CNC aluminum components sets a new standard for quality and innovation.
The Practical Uses of CNC Aluminum
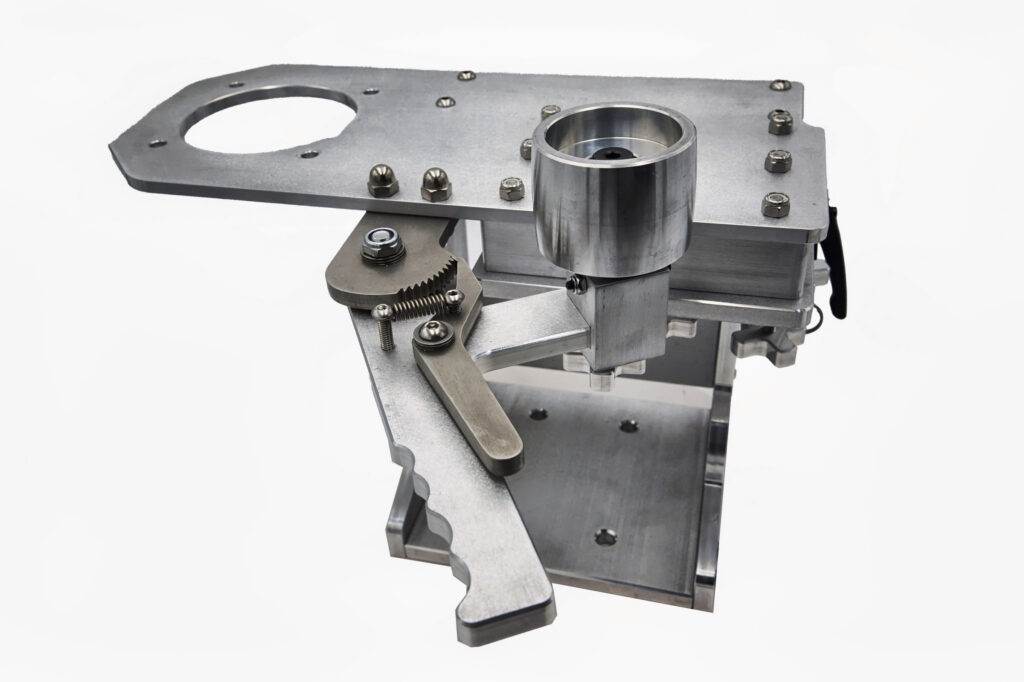
CNC aluminum machining finds practical applications across a wide range of industries. In the automotive sector, for instance, manufacturers utilize CNC aluminum components to produce lightweight parts that improve fuel efficiency without sacrificing performance. From engine components to body panels, the use of aluminum helps reduce overall vehicle weight, which is a critical factor in meeting environmental regulations and consumer demands for sustainability.
In addition to automotive applications, CNC aluminum is extensively used in the aerospace industry. Aircraft components require materials that are both lightweight and strong, making aluminum an ideal choice. CNC machining allows for the production of intricate parts that meet strict safety standards while optimizing performance.
Furthermore, the versatility of CNC aluminum extends to consumer products, where it is used in everything from kitchen appliances to electronic devices. The ability to customize designs and create unique features makes CNC aluminum an invaluable resource in product development.
The Professional Appearance of CNC Aluminum
Aspect | Metric |
---|---|
Surface Finish | Ra value of 0.8 micrometers |
Tolerance | ±0.005 inches |
Appearance | Smooth and uniform |
Color | Depends on anodizing or coating |
The professional appearance of CNC aluminum components cannot be overstated. The precision machining process results in parts that exhibit a high level of craftsmanship, which is essential for businesses aiming to project a polished image. Whether it’s a custom enclosure for electronic equipment or a decorative element in architectural design, the aesthetic quality of CNC aluminum enhances the overall perception of a brand.
Additionally, the surface finish achievable through CNC machining can be tailored to meet specific requirements. Options such as anodizing or powder coating not only improve the visual appeal but also provide added protection against wear and corrosion. This attention to detail in both design and finish contributes to a professional look that resonates with consumers and clients alike.
In industries where first impressions matter, investing in high-quality CNC aluminum components can significantly elevate a company’s reputation.
The Manufacturing Process of CNC Aluminum
The manufacturing process of CNC aluminum involves several key steps that ensure precision and quality throughout production. Initially, a digital design is created using computer-aided design (CAD) software, which serves as the blueprint for the machining process. This design is then converted into a format that can be read by CNC machines, allowing for automated cutting and shaping of the aluminum material.
Once the design is finalized, the selected aluminum stock is secured in the CNC machine. The machine utilizes various cutting tools to remove material according to the programmed specifications. This process can include milling, turning, drilling, and grinding, depending on the complexity of the part being produced.
The result is a highly accurate component that meets exact tolerances and specifications. Quality control measures are often implemented throughout this process to ensure that each part adheres to industry standards.
Customization Options for CNC Aluminum
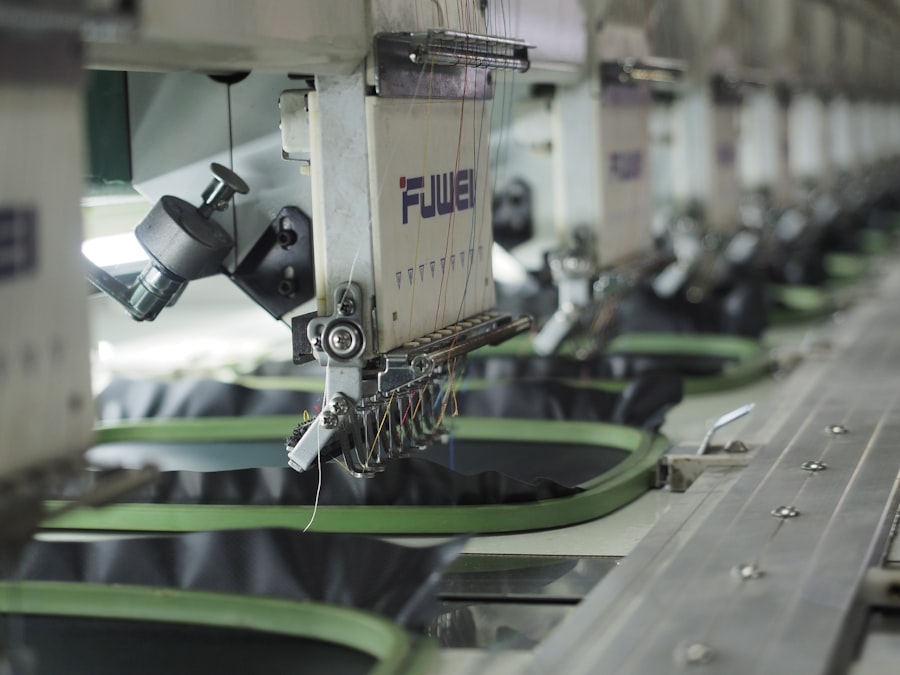
One of the standout features of CNC aluminum machining is the extensive customization options available to manufacturers. With advanced software and machinery, companies can create bespoke designs tailored to specific needs and preferences. This flexibility allows businesses to differentiate their products in a crowded marketplace by offering unique features or designs that cater to their target audience.
Customization can extend beyond just shape and size; surface finishes can also be tailored to enhance both aesthetics and functionality. Options such as anodizing provide not only color choices but also increased durability against environmental factors. Additionally, engraving or etching can be employed to add branding elements or intricate designs directly onto the aluminum surface.
This level of customization ensures that manufacturers can meet diverse customer demands while maintaining high standards of quality.
Maintenance and Care for CNC Aluminum
Maintaining CNC aluminum components is essential for ensuring their longevity and performance over time. While aluminum is known for its resistance to corrosion, it is still important to implement proper care practices to preserve its appearance and functionality. Regular cleaning with mild detergents and soft cloths can help remove dirt and grime without damaging the surface finish.
In addition to routine cleaning, it is advisable to inspect CNC aluminum parts periodically for any signs of wear or damage. Addressing minor issues promptly can prevent more significant problems down the line. For components exposed to harsh environments or heavy use, applying protective coatings can further enhance durability and resistance to corrosion.
By investing time in maintenance, businesses can maximize the lifespan of their CNC aluminum products while ensuring they continue to perform at optimal levels.
The Versatility of CNC Aluminum
In conclusion, CNC aluminum machining stands out as a versatile solution for modern manufacturing needs. Its ability to combine precision engineering with aesthetic appeal makes it an invaluable resource across various industries. From automotive and aerospace applications to consumer products, the benefits of using CNC aluminum are evident in both functionality and design.
As technology continues to advance, the potential for innovation within CNC aluminum machining will only expand further. Companies like TorusCNC 2×72 Grinders exemplify this commitment to quality and precision in their offerings, enabling manufacturers to harness the full potential of this remarkable material. Ultimately, the versatility of CNC aluminum ensures its place as a cornerstone in contemporary manufacturing practices, paving the way for future developments in design and engineering excellence.
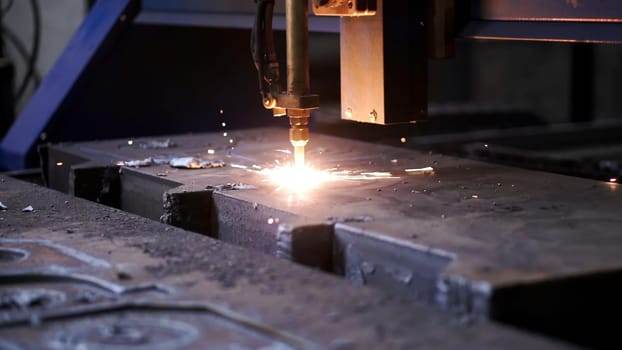
FAQs
What is CNC aluminum?
CNC aluminum refers to aluminum that has been machined using a computer numerical control (CNC) machine. This process allows for precise and complex shapes to be created from aluminum material.
What are the advantages of using CNC aluminum?
Using CNC aluminum offers several advantages, including high precision, excellent surface finish, and the ability to create complex shapes and designs. It is also lightweight, durable, and has good thermal and electrical conductivity.
How is CNC aluminum used in professional appearance and practical utility?
CNC aluminum is often used in industries where both professional appearance and practical utility are important, such as aerospace, automotive, and consumer electronics. Its sleek look and high precision make it ideal for creating components and products that require both aesthetic appeal and functional performance.
What are some common applications of CNC aluminum?
CNC aluminum is commonly used in the production of components for electronic devices, automotive parts, aerospace components, and architectural elements. It is also used in the manufacturing of consumer products such as smartphone cases, laptop enclosures, and high-end kitchenware.
What are the considerations when choosing CNC aluminum for a project?
When choosing CNC aluminum for a project, factors such as the desired surface finish, mechanical properties, and cost should be taken into consideration. It is also important to consider the specific requirements of the application and the capabilities of the CNC machining process.