Nickel alloys are a unique class of materials known for their exceptional resistance to corrosion and oxidation, making them ideal for use in harsh environments. These alloys typically consist of nickel combined with other elements such as chromium, molybdenum, and iron, which enhance their mechanical properties and thermal stability. The inherent strength of nickel alloys allows them to maintain structural integrity at elevated temperatures, making them suitable for applications in aerospace, chemical processing, and marine industries.
Their ability to withstand extreme conditions is a significant factor in their widespread use. In addition to their strength and corrosion resistance, nickel alloys exhibit excellent ductility and formability. This means they can be easily shaped and machined without losing their desirable properties.
The versatility of nickel alloys also extends to their ability to be welded and fabricated, which is crucial in manufacturing processes. Understanding these properties is essential for anyone involved in machining or grinding nickel alloys, as it directly influences the choice of tools, techniques, and safety measures required during processing.
Key Takeaways
- Nickel alloys have high strength, corrosion resistance, and heat resistance, making them suitable for various applications.
- Factors to consider when selecting belts for grinding nickel alloys include material compatibility, grit size, and belt backing type.
- The importance of speed in grinding nickel alloys lies in achieving the desired surface finish and preventing overheating.
- Choosing the right grit size for grinding nickel alloys depends on the material removal rate and surface finish requirements.
- Types of belts suitable for grinding nickel alloys include ceramic, zirconia, and aluminum oxide belts.
Factors to Consider When Selecting Belts for Grinding Nickel Alloys
Abrasive Material Selection
One of the primary considerations is the type of abrasive material used in the belt. Common abrasives include aluminum oxide, zirconia alumina, and ceramic grains, each offering different levels of durability and cutting efficiency.
Belt Backing Material
For nickel alloys, which are often tough and resistant to wear, belts with ceramic abrasives are frequently recommended due to their superior cutting capabilities and longevity. Another important factor is the belt’s backing material. The backing must be robust enough to withstand the stresses of grinding while maintaining flexibility for effective contouring.
Belt Size and Compatibility
Polyester and cloth backings are popular choices for grinding applications involving nickel alloys, as they provide the necessary strength and adaptability. Additionally, the width and length of the belt should be compatible with the grinding machine being used, ensuring a proper fit that allows for smooth operation.
The Importance of Speed in Grinding Nickel Alloys
Speed plays a crucial role in the grinding process of nickel alloys, influencing both the efficiency of material removal and the quality of the finished surface. The optimal speed for grinding depends on various factors, including the type of alloy being processed, the abrasive material of the belt, and the specific grinding application. Generally, higher speeds can lead to faster material removal rates; however, they can also generate excessive heat, which may adversely affect the properties of the alloy being ground.
Maintaining an appropriate balance between speed and pressure is essential to avoid overheating and potential damage to the workpiece. Operators must be mindful of the specific characteristics of the nickel alloy they are working with, as some alloys may require slower speeds to achieve a desirable finish without compromising their structural integrity. Understanding the relationship between speed and grinding performance is vital for achieving optimal results while minimizing wear on both the belts and the workpieces.
Choosing the Right Grit Size for Grinding Nickel Alloys
Selecting the appropriate grit size for grinding nickel alloys is a critical decision that can significantly impact the efficiency of the process and the quality of the final surface finish. Grit size refers to the size of the abrasive particles on the belt; smaller grit sizes produce finer finishes but remove material more slowly, while larger grit sizes remove material quickly but may leave a rougher surface. For nickel alloys, a balanced approach is often necessary to achieve both effective material removal and a satisfactory surface finish.
Typically, a coarser grit size is recommended for initial grinding stages to quickly remove excess material or imperfections. As the process progresses, transitioning to finer grits allows for refining the surface finish and achieving the desired smoothness. It is essential to consider the specific requirements of the project when determining grit size; factors such as the alloy’s hardness, thickness, and intended application will influence this choice.
By carefully selecting grit sizes throughout the grinding process, operators can optimize performance while ensuring high-quality results.
Types of Belts Suitable for Grinding Nickel Alloys
Various types of belts are available for grinding nickel alloys, each designed to meet specific needs based on the characteristics of the material being processed. One common type is the coated abrasive belt, which features a layer of abrasive grains bonded to a flexible backing material. These belts are versatile and can be used for both rough grinding and finishing applications on nickel alloys.
Their adaptability makes them suitable for a wide range of tasks, from removing heavy stock to achieving fine surface finishes. Another option is non-woven abrasive belts, which consist of synthetic fibers impregnated with abrasive materials. These belts are particularly effective for finishing operations as they provide a consistent surface finish without altering the underlying geometry of the workpiece.
Non-woven belts are ideal for applications where a delicate touch is required, such as polishing or blending surfaces on nickel alloys. Understanding the different types of belts available allows operators to select the most appropriate option based on their specific grinding requirements.
Tips for Extending the Lifespan of Belts When Grinding Nickel Alloys
Extending the lifespan of grinding belts when working with nickel alloys requires careful attention to several factors that can influence wear and tear. One effective strategy is to maintain proper tension on the belt during operation. A well-tensioned belt ensures consistent contact with the workpiece while minimizing slippage or excessive wear on one side.
Regularly checking and adjusting belt tension can significantly enhance performance and prolong belt life. Additionally, operators should monitor the grinding pressure applied during use. Excessive pressure can lead to premature wear on both the belt and the workpiece, while insufficient pressure may result in ineffective material removal.
Finding an optimal balance is key; operators should adjust pressure based on the specific characteristics of the nickel alloy being processed. Furthermore, keeping belts clean from debris and contaminants can prevent clogging and maintain cutting efficiency over time.
Safety Precautions When Grinding Nickel Alloys
Safety should always be a top priority when grinding nickel alloys due to potential hazards associated with dust generation, noise levels, and equipment operation. Operators should wear appropriate personal protective equipment (PPE), including safety goggles or face shields to protect against flying debris, hearing protection to guard against excessive noise levels, and gloves designed for handling abrasive materials. Ensuring that all PPE fits properly is essential for maximizing protection during grinding operations.
In addition to personal safety measures, it is crucial to maintain a clean and organized workspace. Dust generated during grinding can pose respiratory hazards; therefore, using proper ventilation systems or dust extraction equipment can help mitigate these risks. Regularly inspecting equipment for wear or malfunction is also vital; any damaged components should be repaired or replaced immediately to prevent accidents during operation.
By adhering to these safety precautions, operators can create a safer working environment while effectively processing nickel alloys.
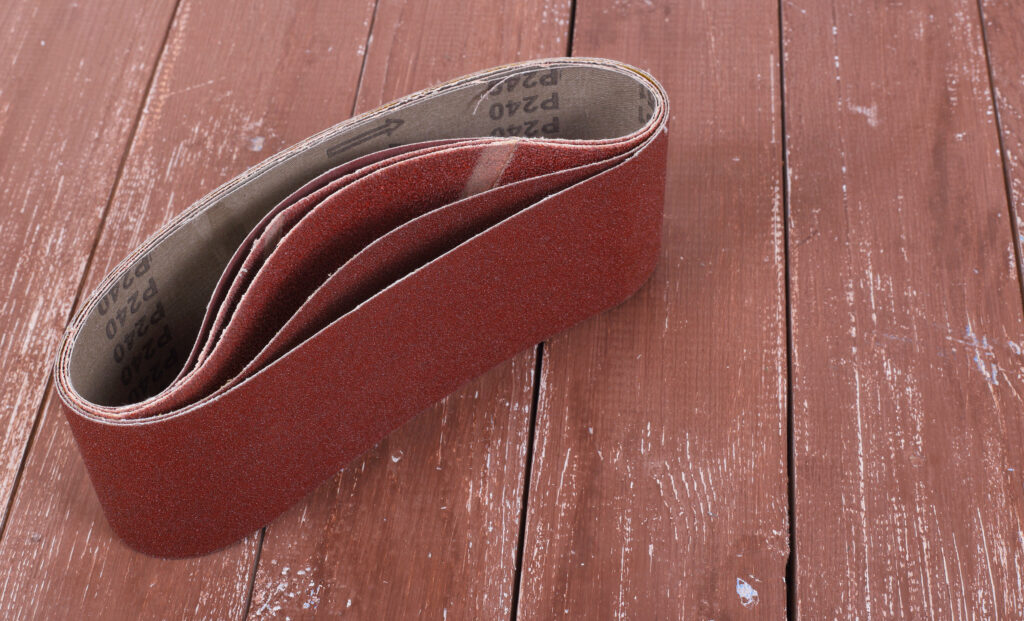
Common Mistakes to Avoid When Grinding Nickel Alloys
When grinding nickel alloys, several common mistakes can hinder performance and lead to suboptimal results. One frequent error is using inappropriate belt speeds or pressures that do not align with the specific characteristics of the alloy being processed. This can result in excessive heat generation or inadequate material removal rates, ultimately affecting both productivity and surface quality.
Operators should take time to understand their materials and adjust settings accordingly. Another mistake often made is neglecting regular maintenance checks on equipment and belts. Failing to inspect belts for signs of wear or damage can lead to unexpected failures during operation, resulting in downtime and increased costs.
Additionally, not cleaning workpieces or belts regularly can cause contamination that affects grinding efficiency. By avoiding these common pitfalls and implementing best practices in maintenance and operation, operators can enhance their grinding processes significantly.
How to Achieve the Desired Surface Finish When Grinding Nickel Alloys
Achieving a desired surface finish when grinding nickel alloys involves a combination of technique, equipment selection, and process control. The initial step is selecting an appropriate grit size based on the desired finish; coarser grits are typically used for initial stock removal while finer grits are employed for finishing stages. Operators should also consider using non-woven abrasive belts during final passes to achieve a smoother surface without altering part geometry.
In addition to grit selection, controlling variables such as speed, pressure, and cooling methods plays a significant role in surface finish quality. Maintaining consistent pressure throughout the grinding process helps ensure uniformity in material removal while preventing overheating that could damage the workpiece’s surface integrity. Implementing cooling techniques such as using lubricants or coolant systems can further enhance surface quality by reducing friction and heat generation during grinding operations.
Advantages and Disadvantages of Different Speeds for Grinding Nickel Alloys
The choice of speed during grinding operations has both advantages and disadvantages that must be carefully weighed when working with nickel alloys. Higher speeds often lead to increased material removal rates, allowing operators to complete tasks more quickly. However, this advantage comes with potential drawbacks; excessive speeds can generate significant heat that may compromise the integrity of sensitive nickel alloys or lead to premature wear on abrasive belts.
Conversely, lower speeds may provide better control over heat generation and surface finish quality but can result in slower material removal rates. This trade-off necessitates a thorough understanding of both the specific alloy being processed and the desired outcomes of the grinding operation. By evaluating these factors carefully, operators can select speeds that optimize performance while minimizing risks associated with overheating or excessive wear.
The Role of Cooling and Lubrication in Grinding Nickel Alloys
Cooling and lubrication are critical components in effectively grinding nickel alloys due to their tendency to generate heat during processing. The application of coolants or lubricants helps dissipate heat generated by friction between the abrasive belt and workpiece, reducing thermal stress on both materials involved in the operation. This not only protects the integrity of nickel alloys but also extends belt life by minimizing wear caused by excessive heat.
There are various methods for applying cooling agents during grinding operations; flood cooling systems provide continuous coolant flow over the workpiece while misting systems deliver fine droplets directly onto contact points between belts and materials. Selecting an appropriate cooling method depends on factors such as machine design, workpiece geometry, and specific alloy characteristics. By effectively managing cooling and lubrication during grinding processes, operators can achieve better results while ensuring longevity in both their tools and workpieces.
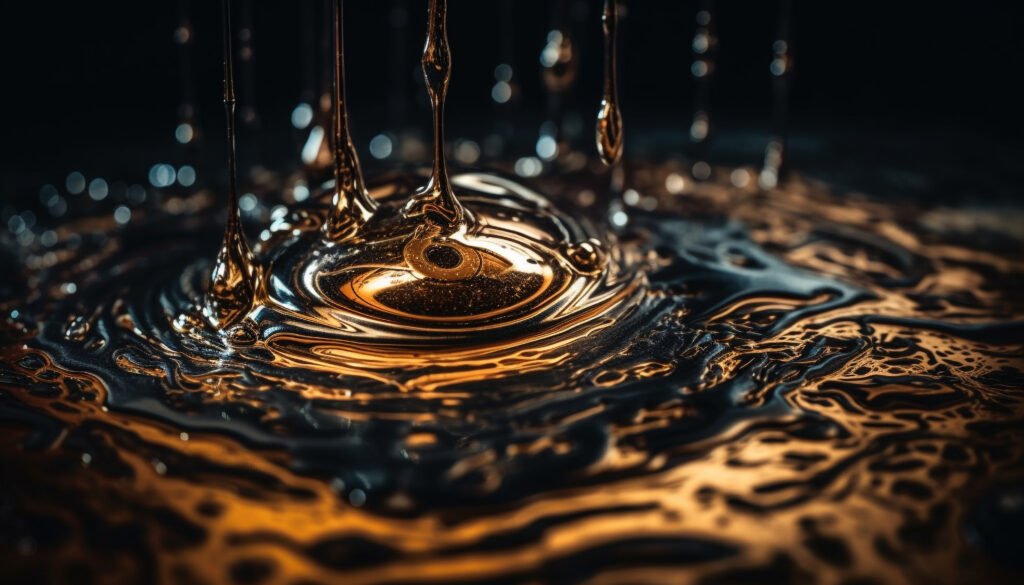
FAQs
What are nickel alloys?
Nickel alloys are metals that contain nickel as the primary component, along with other elements such as iron, copper, chromium, and molybdenum. These alloys are known for their high strength, corrosion resistance, and heat resistance, making them suitable for a wide range of applications in industries such as aerospace, automotive, and chemical processing.
What is grinding in the context of nickel alloys?
Grinding is a machining process that involves the use of an abrasive material to remove small amounts of material from a workpiece. In the context of nickel alloys, grinding is often used to achieve precise dimensions, smooth surface finishes, and tight tolerances on components such as turbine blades, engine components, and medical implants.
What are the considerations for choosing the right grinding belt for nickel alloys?
When grinding nickel alloys, it is important to choose the right grinding belt that can effectively remove material without causing excessive heat buildup or surface damage. Factors to consider include the type of abrasive material, the backing material, the grit size, and the bonding agent. Additionally, the compatibility of the grinding belt with the specific nickel alloy being machined should be taken into account.
What are the recommended speed settings for grinding nickel alloys?
The recommended speed settings for grinding nickel alloys depend on factors such as the type of grinding machine, the size and type of grinding belt, and the specific nickel alloy being machined. Generally, lower speeds are preferred to minimize heat generation and prevent workpiece damage. It is important to consult the manufacturer’s guidelines and conduct test runs to determine the optimal speed settings for a given application.
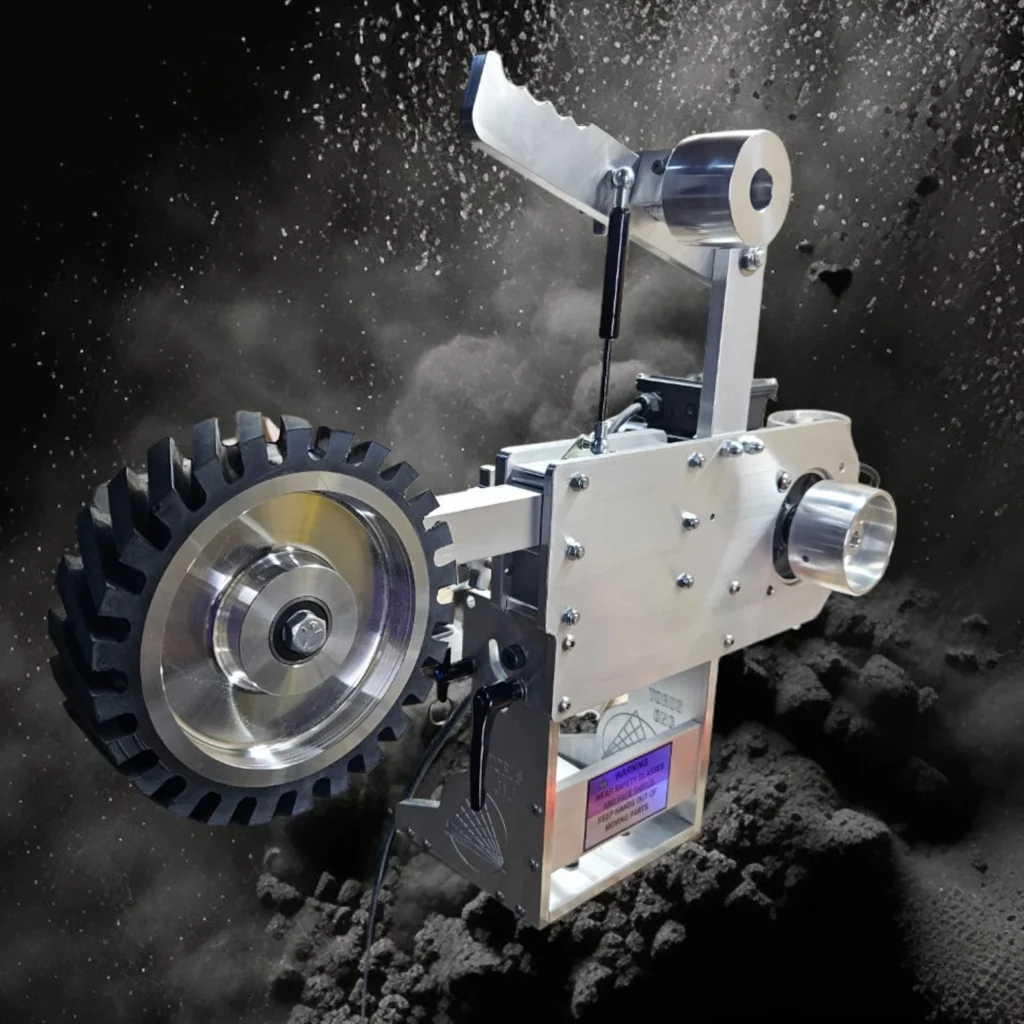