CNC integration for 2×72 grinders represents a significant advancement in the world of metalworking and fabrication. At its core, CNC, or Computer Numerical Control, allows for the automation of machine tools through the use of computer programming. This technology enables operators to achieve high levels of precision and repeatability in their grinding processes.
The 2×72 grinder, a popular choice among metalworkers and knife makers, benefits immensely from this integration, as it enhances the machine’s capabilities and streamlines workflows. The fundamental principle behind CNC integration is the conversion of design specifications into machine movements. By utilizing a computer to control the grinder’s motor and other components, users can execute complex grinding tasks with minimal manual intervention.
This not only increases efficiency but also reduces the likelihood of human error. Understanding these basics is crucial for anyone looking to leverage CNC technology in their 2×72 grinder setup, as it lays the groundwork for more advanced applications and techniques.
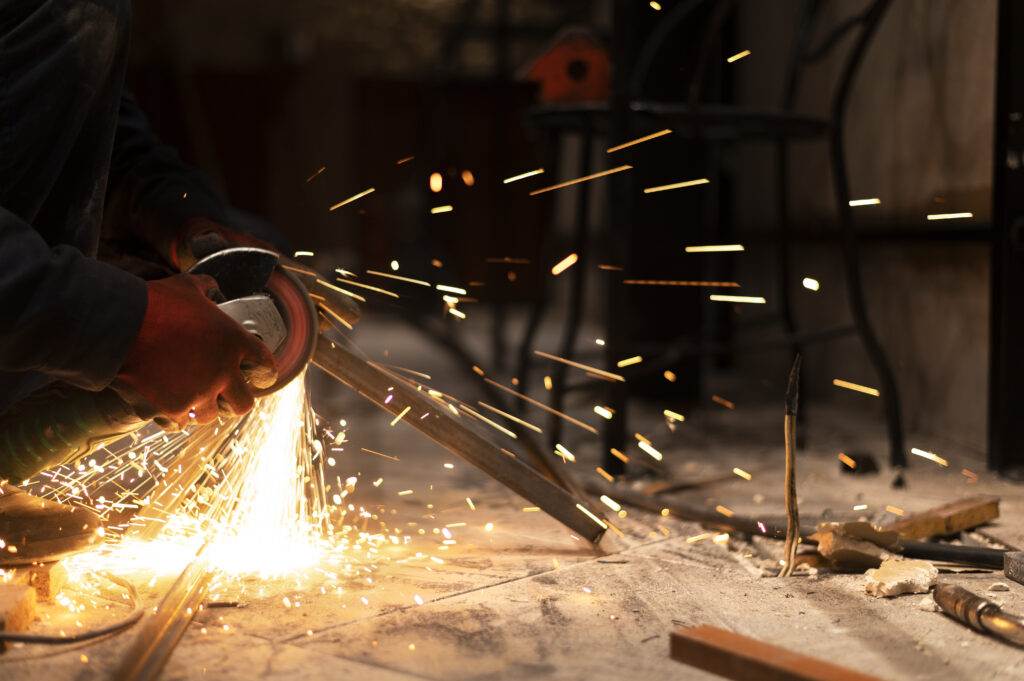
Key Takeaways
- Understanding the Basics of CNC Integration for 2×72 Grinders:
- CNC integration allows for automated control of the 2×72 grinder, increasing precision and efficiency.
- It involves the use of computer numerical control (CNC) systems to automate the grinding process.
- Choosing the Right CNC System for Your 2×72 Grinder:
- Consider factors such as budget, desired features, and compatibility with your grinder when selecting a CNC system.
- Look for a system that offers user-friendly software and reliable hardware for seamless integration.
- Setting Up and Calibrating Your CNC Integration for Optimal Performance:
- Proper installation and calibration of the CNC system are crucial for achieving optimal performance.
- Follow the manufacturer’s guidelines and perform regular maintenance to ensure consistent results.
- Programming Tips for Maximizing Efficiency and Precision:
- Utilize software features such as toolpath optimization and simulation to maximize efficiency and precision.
- Take the time to learn and understand the programming capabilities of your CNC system for better results.
- Expanding Your 2×72 Grinder’s Capabilities with CNC Integration:
- CNC integration opens up possibilities for complex grinding operations and customization.
- Explore additional attachments and accessories that can further enhance the capabilities of your CNC-integrated grinder.
Choosing the Right CNC System for Your 2×72 Grinder
Selecting the appropriate CNC system for your 2×72 grinder is a critical step that can significantly impact your machining capabilities. Various factors come into play when making this decision, including the specific applications you intend to pursue, your budget, and the level of technical expertise available. A well-chosen CNC system can enhance your grinder’s performance, allowing for intricate designs and consistent results.
When evaluating different CNC systems, consider the compatibility with your existing 2×72 grinder setup. Some systems are designed specifically for certain models or brands, while others offer universal compatibility. Additionally, assess the software that accompanies the CNC system.
User-friendly software can make a substantial difference in how easily you can program and operate your grinder. Look for systems that provide robust support and resources, as this can be invaluable when troubleshooting or seeking to expand your capabilities in the future.
Setting Up and Calibrating Your CNC Integration for Optimal Performance
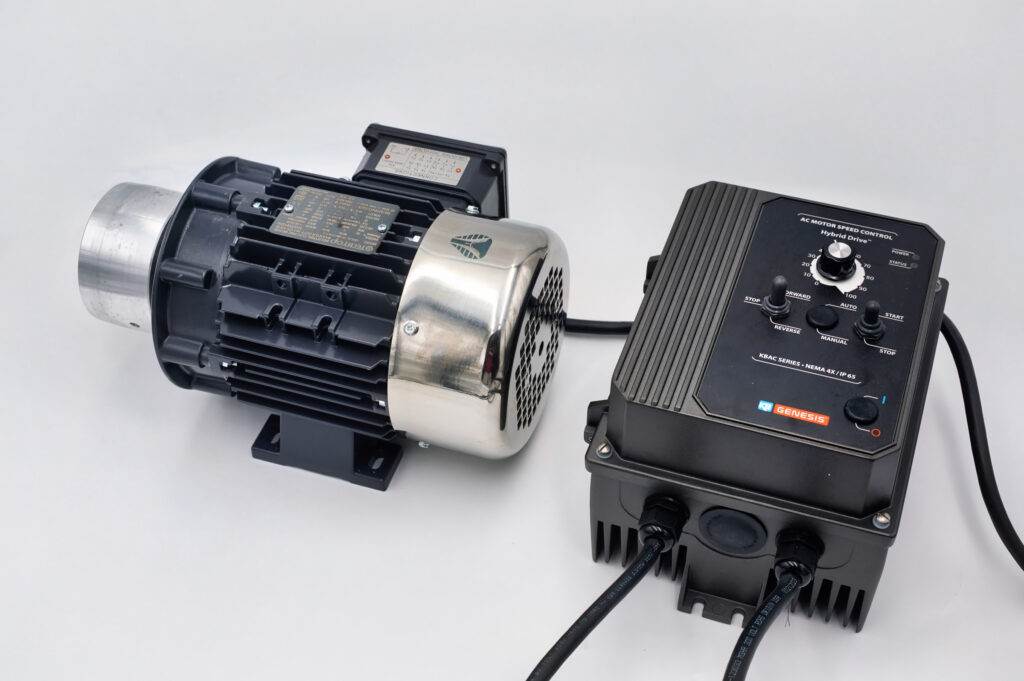
Once you have selected a suitable CNC system for your 2×72 grinder, the next step is to set it up and calibrate it for optimal performance. This process involves several key steps, including mounting the CNC components securely to your grinder and ensuring that all electrical connections are properly established. A meticulous setup is essential to prevent any operational issues that could arise from loose connections or misaligned components.
Calibration is equally important in achieving precise results. This typically involves adjusting parameters such as speed, feed rate, and depth of cut to match the specific materials you will be working with. Many CNC systems come with calibration tools or software that guide you through this process.
Taking the time to calibrate your system correctly will pay off in terms of improved accuracy and consistency in your grinding operations.
Programming Tips for Maximizing Efficiency and Precision
Tip Number | Tip Description | Efficiency Rating | Precision Rating |
---|---|---|---|
1 | Use meaningful variable names | 4.5 | 4.0 |
2 | Break down complex tasks into smaller functions | 4.0 | 4.5 |
3 | Utilize version control systems | 4.5 | 4.0 |
4 | Write clear and concise comments | 4.0 | 4.5 |
5 | Regularly refactor and optimize code | 4.5 | 4.0 |
Programming your CNC-integrated 2×72 grinder effectively is key to maximizing both efficiency and precision in your projects. Familiarizing yourself with the programming language used by your CNC system is essential; this knowledge will enable you to create complex grinding paths and optimize tool movements. Start with simple programs to build your confidence before progressing to more intricate designs.
In addition to understanding the programming language, consider implementing strategies such as using loops and conditional statements to streamline your code. These techniques can help reduce programming time and enhance the overall efficiency of your grinding operations. Furthermore, always test your programs on scrap material before applying them to your actual workpieces.
This practice allows you to identify any potential issues without risking valuable materials.
Expanding Your 2×72 Grinder’s Capabilities with CNC Integration
CNC integration opens up a world of possibilities for expanding the capabilities of your 2×72 grinder. With the right setup, you can explore various applications beyond traditional grinding tasks. For instance, you can incorporate features such as contouring, profiling, and even engraving into your workflow.
This versatility allows you to take on a broader range of projects and cater to diverse customer needs. Moreover, integrating additional attachments or accessories can further enhance your grinder’s functionality. For example, adding a rotary axis can enable you to perform cylindrical grinding operations, while specialized tooling can facilitate unique grinding techniques.
By continuously exploring new ways to utilize your CNC-integrated 2×72 grinder, you can stay ahead of industry trends and maintain a competitive edge in your field.
Troubleshooting Common Issues with CNC Integration on 2×72 Grinders
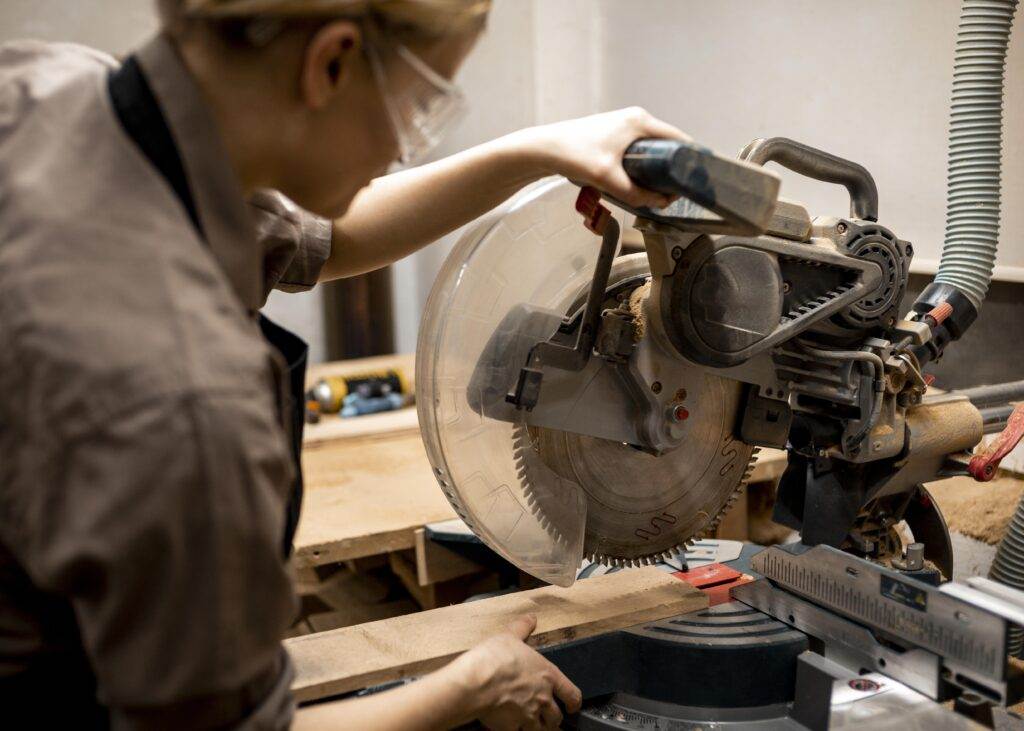
Despite the advantages of CNC integration, users may encounter common issues that can hinder performance. One frequent problem is misalignment between the grinder’s components and the CNC system. This misalignment can lead to inaccurate grinding results or even damage to both the workpiece and the machine itself.
Regularly checking alignment and making necessary adjustments is crucial for maintaining optimal performance. Another common issue involves software glitches or communication errors between the computer and the CNC system. These problems can manifest as unexpected movements or failure to execute commands properly.
To troubleshoot these issues effectively, ensure that all software is up-to-date and that connections are secure. Additionally, consulting user manuals or online forums dedicated to your specific CNC system can provide valuable insights into resolving these challenges.
Safety Considerations When Using CNC Integration with Your 2×72 Grinder
Safety should always be a top priority when operating any machinery, including a CNC-integrated 2×72 grinder. The automation provided by CNC technology does not eliminate the need for vigilance; operators must remain aware of their surroundings and adhere to safety protocols at all times. Proper personal protective equipment (PPE) such as safety glasses, gloves, and hearing protection should be worn during operation.
Furthermore, it is essential to familiarize yourself with emergency stop functions and other safety features built into your CNC system. Regular maintenance checks on both the grinder and the CNC components can help prevent accidents caused by equipment failure. By cultivating a culture of safety within your workspace, you can ensure a secure environment while maximizing productivity.
Exploring Advanced Applications and Techniques for CNC Integration on 2×72 Grinders
As you become more comfortable with CNC integration on your 2×72 grinder, exploring advanced applications and techniques can further enhance your skill set and output quality. One area worth investigating is adaptive grinding, where the machine adjusts its parameters in real-time based on feedback from sensors monitoring cutting conditions. This technique can lead to improved surface finishes and reduced wear on tools.
Additionally, consider delving into multi-axis machining capabilities if your CNC system supports it. This allows for more complex geometries and intricate designs that would be challenging to achieve with traditional methods. By continuously pushing the boundaries of what is possible with your CNC-integrated 2×72 grinder, you can unlock new opportunities for creativity and innovation in your projects.
In conclusion, integrating CNC technology into a 2×72 grinder offers numerous benefits that enhance both efficiency and precision in metalworking tasks. By understanding the basics of CNC integration, choosing the right system, setting up correctly, programming effectively, troubleshooting common issues, prioritizing safety, and exploring advanced applications, users can fully leverage this powerful technology to elevate their craftsmanship and expand their capabilities in the field.
FAQs
What is CNC integration for a 2×72 grinder?
CNC integration for a 2×72 grinder refers to the incorporation of computer numerical control (CNC) technology into the grinder, allowing for automated and precise control of the grinding process.
What are the advanced features that enhance the capabilities of a CNC-integrated 2×72 grinder?
Advanced features of CNC-integrated 2×72 grinders may include automatic tool changing, programmable grinding patterns, precision depth control, and real-time monitoring and adjustment of grinding parameters.
How does CNC integration enhance the precision and efficiency of a 2×72 grinder?
CNC integration allows for precise and repeatable grinding operations, reducing human error and increasing the overall efficiency of the grinding process. It also enables the grinder to perform complex grinding tasks with high accuracy.
What are the potential benefits of CNC integration for a 2×72 grinder?
The potential benefits of CNC integration for a 2×72 grinder include improved productivity, higher quality finished products, reduced setup times, and the ability to produce intricate and custom grinding patterns.
Is CNC integration suitable for all types of 2×72 grinders?
CNC integration may be suitable for various types of 2×72 grinders, but it is important to consider the specific requirements and compatibility of the grinder with CNC technology before implementing integration.