Modular tooling arms are versatile mechanical systems designed to enhance the efficiency and flexibility of manufacturing processes. These arms consist of various interchangeable components that can be configured to perform a wide range of tasks, from assembly to material handling. The modular nature of these arms allows manufacturers to adapt their setups quickly, accommodating different products or production lines without the need for extensive retooling.
This adaptability is particularly beneficial in industries where product designs frequently change or where small batch production is common. The design of modular tooling arms typically incorporates lightweight materials and advanced engineering principles, enabling them to support a variety of tools and attachments. This capability allows for the integration of different functionalities, such as gripping, welding, or even inspection, all within a single arm.
As a result, manufacturers can streamline their operations, reduce downtime, and improve overall productivity. Understanding the fundamental principles behind modular tooling arms is essential for businesses looking to leverage this technology effectively.
Key Takeaways
- Understanding Modular Tooling Arms:
- Modular tooling arms are adjustable and interchangeable components used in various industrial applications for holding, positioning, and manipulating tools and equipment.
- Advantages of Using Modular Tooling Arms:
- Modular tooling arms offer flexibility, cost-effectiveness, and improved productivity by allowing quick tool changes and adjustments.
- Choosing the Right Modular Tooling Arm for Your Application:
- Consider factors such as load capacity, reach, and compatibility with existing equipment when selecting a modular tooling arm for your specific application.
- How to Install and Set Up Modular Tooling Arms:
- Proper installation and setup of modular tooling arms involve following manufacturer guidelines, ensuring secure mounting, and calibrating for optimal performance.
- Tips for Maintaining and Caring for Modular Tooling Arms:
- Regular inspection, cleaning, and lubrication are essential for maintaining modular tooling arms and preventing premature wear and damage.
Advantages of Using Modular Tooling Arms
One of the primary advantages of modular tooling arms is their flexibility. Unlike traditional fixed tooling systems, modular arms can be easily reconfigured to meet changing production needs. This adaptability not only saves time but also reduces costs associated with maintaining multiple specialized tools.
Manufacturers can quickly switch between different tasks or products, allowing for a more dynamic production environment that can respond to market demands with agility. Additionally, modular tooling arms contribute to improved efficiency in manufacturing processes. By integrating multiple functions into a single arm, businesses can minimize the number of machines and tools required on the shop floor.
This consolidation leads to a more organized workspace and reduces the likelihood of errors that can occur when transferring components between different machines. Furthermore, the ability to customize these arms with specific attachments means that manufacturers can optimize their operations for particular tasks, enhancing both speed and accuracy.
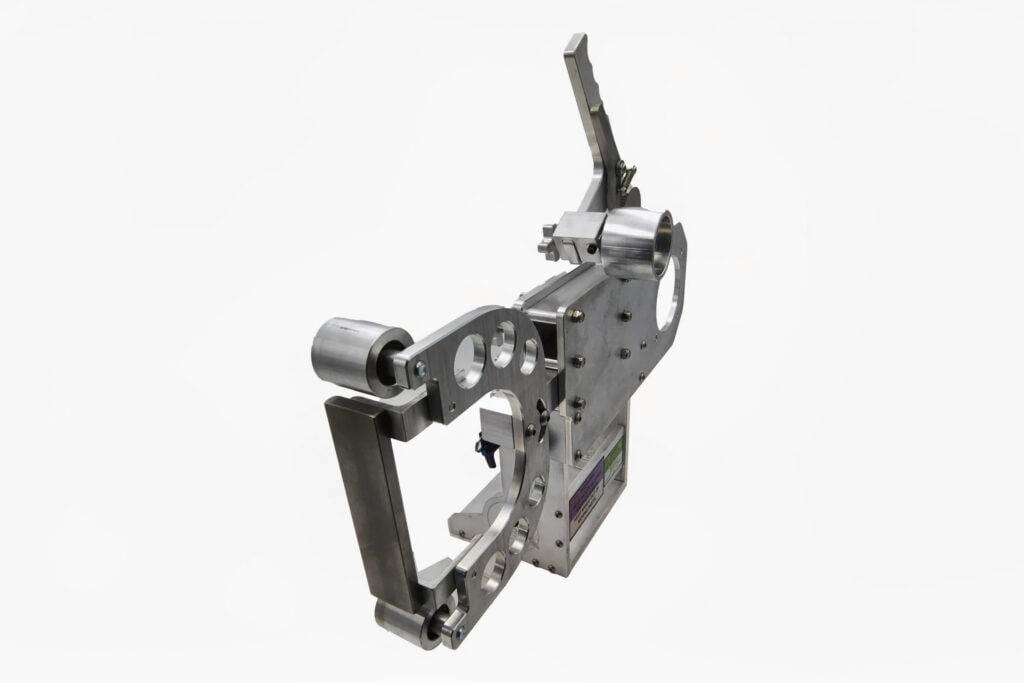
Choosing the Right Modular Tooling Arm for Your Application
Selecting the appropriate modular tooling arm for a specific application involves careful consideration of several factors. First and foremost, businesses must assess the types of tasks they intend to perform with the arm. Different applications may require varying degrees of precision, load capacity, and reach.
For instance, an arm designed for heavy lifting may not be suitable for delicate assembly tasks, so understanding the specific requirements of each application is crucial. Another important aspect to consider is the compatibility of the modular tooling arm with existing equipment and systems. Manufacturers should evaluate how well the arm integrates with their current production setup, including any software or control systems in use.
Additionally, it is essential to consider the availability of attachments and accessories that can enhance the arm’s functionality. By choosing a modular tooling arm that aligns with both current and future needs, businesses can ensure a more sustainable investment in their manufacturing capabilities.
How to Install and Set Up Modular Tooling Arms
The installation and setup of modular tooling arms require careful planning and execution to ensure optimal performance. Initially, it is vital to review the manufacturer’s guidelines and specifications for the specific arm being installed. This documentation typically includes detailed instructions on assembly, calibration, and integration with other systems.
Following these guidelines closely can help prevent common pitfalls during installation. Once the arm is assembled, it is essential to conduct thorough testing before full-scale operation begins. This testing phase should include verifying that all components function correctly and that the arm operates smoothly within its designated range of motion.
Calibration may also be necessary to ensure that the arm performs tasks with the required precision. By taking the time to properly install and set up modular tooling arms, manufacturers can avoid potential issues down the line and maximize their investment in this technology.
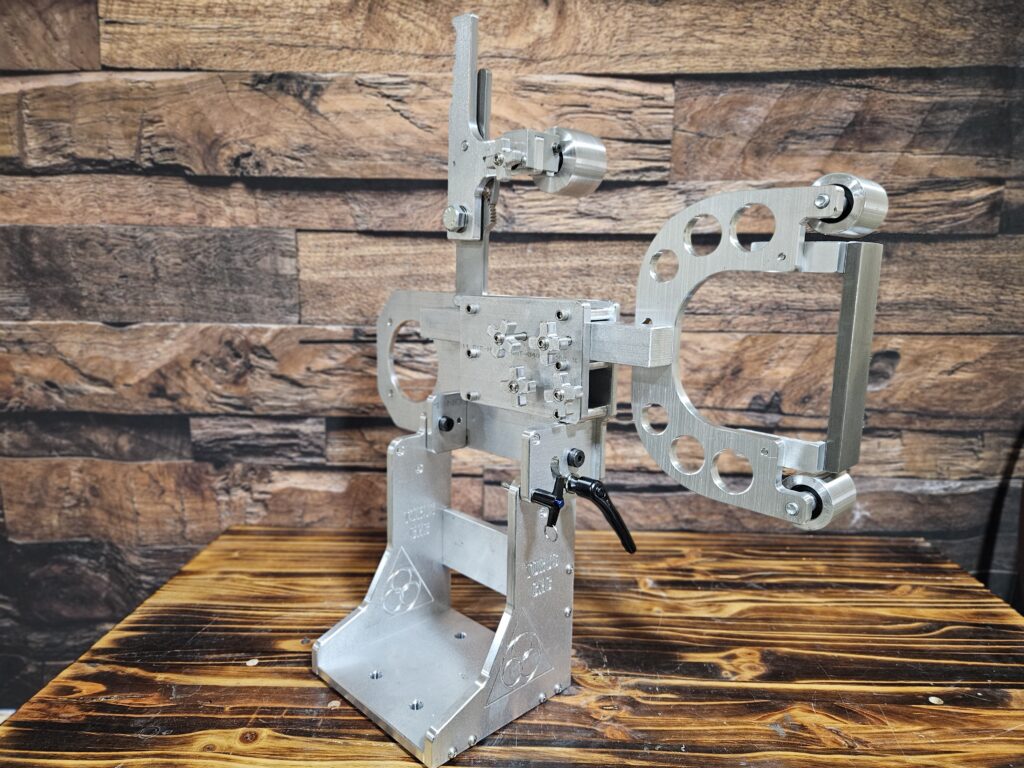
Tips for Maintaining and Caring for Modular Tooling Arms
Regular maintenance is crucial for ensuring the longevity and reliability of modular tooling arms. One key aspect of maintenance involves routine inspections to identify any signs of wear or damage. Components such as joints, bearings, and motors should be checked periodically to ensure they are functioning correctly.
Addressing minor issues promptly can prevent more significant problems from developing and extend the lifespan of the equipment. In addition to inspections, proper cleaning is essential for maintaining modular tooling arms. Dust and debris can accumulate on moving parts, leading to decreased performance or even mechanical failure over time.
Manufacturers should establish a cleaning schedule that includes wiping down surfaces and lubricating moving parts as needed. By prioritizing maintenance and care, businesses can keep their modular tooling arms operating at peak efficiency.
Maximizing Efficiency and Productivity with Modular Tooling Arms
To fully leverage the potential of modular tooling arms, manufacturers must focus on maximizing efficiency and productivity within their operations. One effective strategy involves analyzing workflow processes to identify areas where modular arms can be integrated for optimal performance. By mapping out production steps and pinpointing bottlenecks, businesses can determine how best to deploy these arms to streamline operations.
Training employees on how to use modular tooling arms effectively is another critical factor in maximizing productivity. Ensuring that staff members are well-versed in operating these systems can lead to smoother workflows and reduced downtime. Additionally, encouraging feedback from operators can provide valuable insights into potential improvements or adjustments that could enhance overall efficiency.
Integrating Modular Tooling Arms into Your Production Process
Integrating modular tooling arms into an existing production process requires a strategic approach to ensure seamless operation. Initially, it is essential to assess how these arms will fit into current workflows and identify any necessary adjustments to accommodate their use. This may involve reconfiguring workstations or modifying processes to optimize the benefits offered by modular tooling arms.
Collaboration between different departments—such as engineering, production, and maintenance—is vital during this integration phase. By fostering open communication among teams, businesses can address any challenges that arise during implementation and ensure that everyone is aligned on goals and expectations. A well-planned integration process will ultimately lead to smoother operations and enhanced productivity.
Common Challenges and Solutions when Using Modular Tooling Arms
While modular tooling arms offer numerous benefits, they are not without challenges. One common issue is ensuring compatibility with existing equipment and systems. Businesses may encounter difficulties when trying to integrate new arms into older production lines or machinery that lacks modern interfaces.
To address this challenge, manufacturers should conduct thorough compatibility assessments before purchasing new equipment. Another challenge involves training personnel on how to operate modular tooling arms effectively. Employees may require additional training to adapt to new technologies or workflows introduced by these systems.
Providing comprehensive training programs that include hands-on experience can help mitigate this issue and empower staff members to utilize modular tooling arms confidently.
Enhancing Safety and Ergonomics with Modular Tooling Arms
Safety is a paramount concern in any manufacturing environment, and modular tooling arms can play a significant role in enhancing workplace safety. These systems are often designed with safety features such as sensors and emergency stop functions that help prevent accidents during operation. By incorporating these safety measures into their design, manufacturers can create a safer working environment for employees.
Moreover, modular tooling arms contribute to improved ergonomics in the workplace. By automating repetitive tasks or heavy lifting, these systems reduce physical strain on workers, minimizing the risk of injuries related to overexertion or improper lifting techniques. Investing in ergonomic solutions not only benefits employee well-being but also leads to increased productivity as workers can focus on higher-value tasks without physical limitations.
Case Studies: Successful Implementations of Modular Tooling Arms
Examining case studies of successful implementations of modular tooling arms provides valuable insights into their practical applications across various industries. For instance, a leading automotive manufacturer integrated modular tooling arms into its assembly line to enhance flexibility in producing different vehicle models. By utilizing these systems, the company was able to reduce changeover times significantly while maintaining high-quality standards.
Another example comes from the electronics industry, where a manufacturer adopted modular tooling arms for precision assembly tasks involving delicate components. The ability to customize attachments allowed them to optimize their processes for specific products while ensuring consistent quality control throughout production. These case studies illustrate how modular tooling arms can drive innovation and efficiency across diverse manufacturing sectors.
Future Trends and Innovations in Modular Tooling Arm Technology
As technology continues to evolve, so too does the landscape of modular tooling arms. One emerging trend is the integration of advanced robotics and artificial intelligence into these systems. By incorporating smart technologies, manufacturers can enhance automation capabilities, allowing for more sophisticated operations that adapt in real-time based on production demands.
Additionally, advancements in materials science are leading to lighter yet stronger components for modular tooling arms. This development not only improves performance but also enhances energy efficiency during operation. As manufacturers seek ways to reduce their environmental impact while maintaining productivity levels, innovations in modular tooling arm technology will play a crucial role in shaping the future of manufacturing processes.
In conclusion, understanding modular tooling arms is essential for manufacturers looking to enhance their operational efficiency and flexibility. By recognizing their advantages, choosing the right systems for specific applications, and implementing best practices for installation and maintenance, businesses can maximize productivity while addressing common challenges effectively. As technology continues to advance, staying informed about future trends will be vital for leveraging modular tooling arms as a key component in modern manufacturing strategies.
FAQs
What are modular tooling arms?
Modular tooling arms are adjustable and interchangeable components used in manufacturing and industrial settings to hold tools, fixtures, and other equipment. They are designed to be easily reconfigured and adapted to different workflow needs.
How do modular tooling arms help with rapid workflow changes?
Modular tooling arms allow for quick and easy reconfiguration of workstations and equipment, enabling rapid changes to the workflow. This flexibility can help improve efficiency and productivity in dynamic manufacturing environments.
What are the benefits of using modular tooling arms?
Some benefits of using modular tooling arms include increased flexibility, reduced downtime for reconfiguration, improved organization, and the ability to adapt to changing production needs. They can also help optimize space utilization and enhance worker safety.
What industries can benefit from using modular tooling arms?
Industries such as automotive manufacturing, aerospace, electronics, and general metalworking can benefit from using modular tooling arms. Any industry that requires frequent workflow changes and adaptable workstations can find value in this type of tooling system.
Are there different types of modular tooling arms available?
Yes, there are various types of modular tooling arms available, including adjustable arms, swivel arms, telescoping arms, and custom-configured arms. These options allow for a wide range of applications and customization to meet specific workflow requirements.