Batch grinding is a crucial process in the small-scale knife production industry, where efficiency and precision are paramount. This method involves processing multiple knives simultaneously, allowing manufacturers to optimize their time and resources. In a world where customization and quality are increasingly demanded by consumers, batch grinding offers a practical solution for small knife producers looking to maintain high standards while managing production costs.
By understanding the intricacies of batch grinding, manufacturers can enhance their production capabilities and deliver superior products to their customers. The significance of batch grinding extends beyond mere efficiency; it also plays a vital role in ensuring uniformity across products. In small knife production, where each piece may be handcrafted or tailored to specific customer requirements, achieving consistency in blade sharpness and finish is essential.
This article will explore the various aspects of batch grinding, from selecting the right equipment to implementing effective quality control measures, providing a comprehensive guide for small knife manufacturers aiming to refine their production processes.
Key Takeaways
- Batch grinding is essential for small knife production to ensure consistency and efficiency in the manufacturing process.
- Choosing the right grinding equipment is crucial for small batch production to achieve the desired results and maintain quality standards.
- Consistency in batch grinding is important for producing uniform and high-quality knife products.
- Setting up an efficient batch grinding process requires careful planning and consideration of various factors such as equipment, workflow, and organization.
- Proper blade sharpening techniques and the use of cooling and lubrication are key to maximizing efficiency in batch grinding for small knife production.
Choosing the Right Grinding Equipment for Small Batch Production
Selecting the appropriate grinding equipment is fundamental to the success of batch grinding in small knife production. The right machinery not only enhances productivity but also ensures that the knives produced meet the desired specifications. When evaluating grinding equipment, manufacturers should consider factors such as the type of material being processed, the desired finish, and the scale of production.
For instance, belt grinders are often favored for their versatility and ability to handle various materials, while surface grinders may be preferred for achieving a precise finish on flat surfaces. In addition to the type of grinder, manufacturers must also assess the power and speed of the equipment. High-speed grinders can significantly reduce processing time, but they may also generate excessive heat, which can affect the integrity of the blade material.
Therefore, it is essential to strike a balance between speed and control. Investing in high-quality grinding equipment that offers adjustable settings can provide manufacturers with the flexibility needed to adapt to different production requirements while maintaining optimal performance.
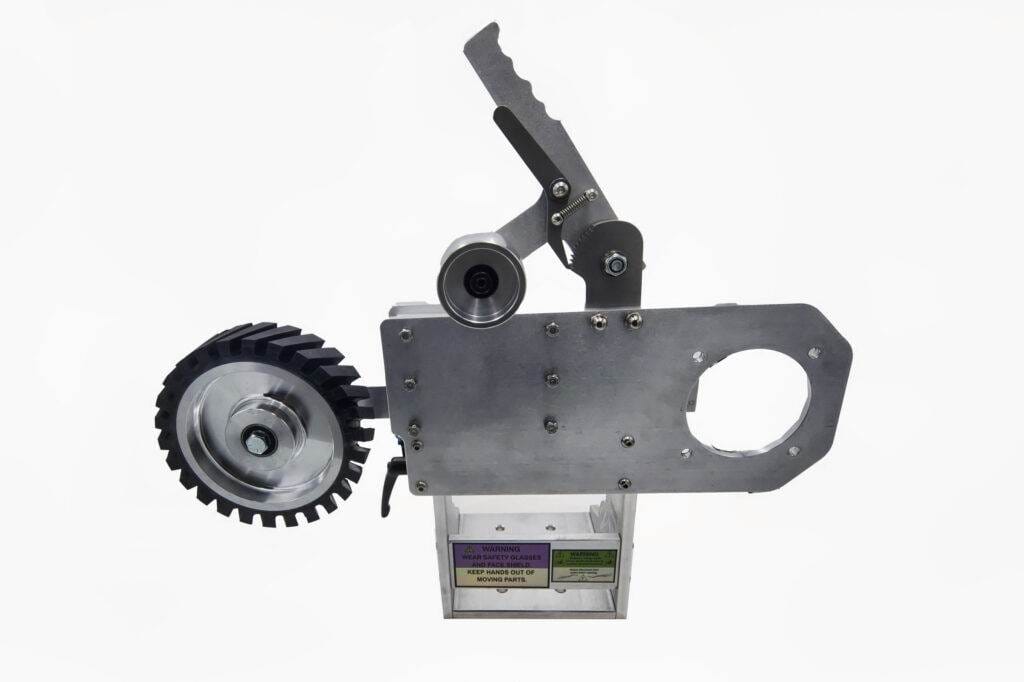
Understanding the Importance of Consistency in Batch Grinding
Consistency is a cornerstone of successful batch grinding in small knife production. When producing knives in batches, it is imperative that each blade exhibits uniform sharpness and finish. Inconsistent results can lead to customer dissatisfaction and damage a brand’s reputation.
Moreover, variations in blade quality can result in increased returns and warranty claims, ultimately affecting profitability. Therefore, establishing a consistent grinding process is essential for maintaining product quality and ensuring customer loyalty. To achieve consistency, manufacturers should implement standardized operating procedures (SOPs) that outline each step of the grinding process.
This includes specifying the grinding angles, feed rates, and cooling methods used during production. By adhering to these guidelines, manufacturers can minimize variability and ensure that each batch of knives meets the same high standards. Additionally, regular training for operators on these SOPs can further enhance consistency by ensuring that all team members are equipped with the knowledge and skills necessary to produce quality knives.
Tips for Setting Up an Efficient Batch Grinding Process
Setting up an efficient batch grinding process requires careful planning and organization. One of the first steps is to create a dedicated workspace that minimizes distractions and allows for smooth workflow. This includes arranging equipment in a logical sequence that facilitates easy access and movement between different stages of production.
For example, placing the grinder near the workbench where knives are assembled can reduce unnecessary handling and transportation time. Another critical aspect of an efficient batch grinding process is time management. Manufacturers should establish a clear timeline for each stage of production, from initial grinding to final inspection.
Utilizing tools such as timers or production schedules can help keep track of progress and ensure that deadlines are met. Additionally, incorporating regular breaks for maintenance and operator rest can prevent burnout and maintain productivity levels throughout the grinding process.
Maximizing Efficiency through Proper Blade Sharpening Techniques
Proper blade sharpening techniques are essential for maximizing efficiency in batch grinding. A well-sharpened blade not only enhances cutting performance but also reduces wear on grinding equipment, leading to longer tool life and less frequent maintenance. To achieve optimal sharpening results, manufacturers should consider using a combination of techniques tailored to the specific type of knife being produced.
One effective method is to employ a multi-step sharpening process that gradually refines the blade edge. Starting with a coarse grit to establish the primary bevel, followed by progressively finer grits can yield a razor-sharp edge while minimizing material removal. Additionally, incorporating honing or stropping techniques at the end of the sharpening process can further enhance edge retention and performance.
By investing time in proper sharpening techniques, manufacturers can improve overall efficiency and produce knives that meet or exceed customer expectations.
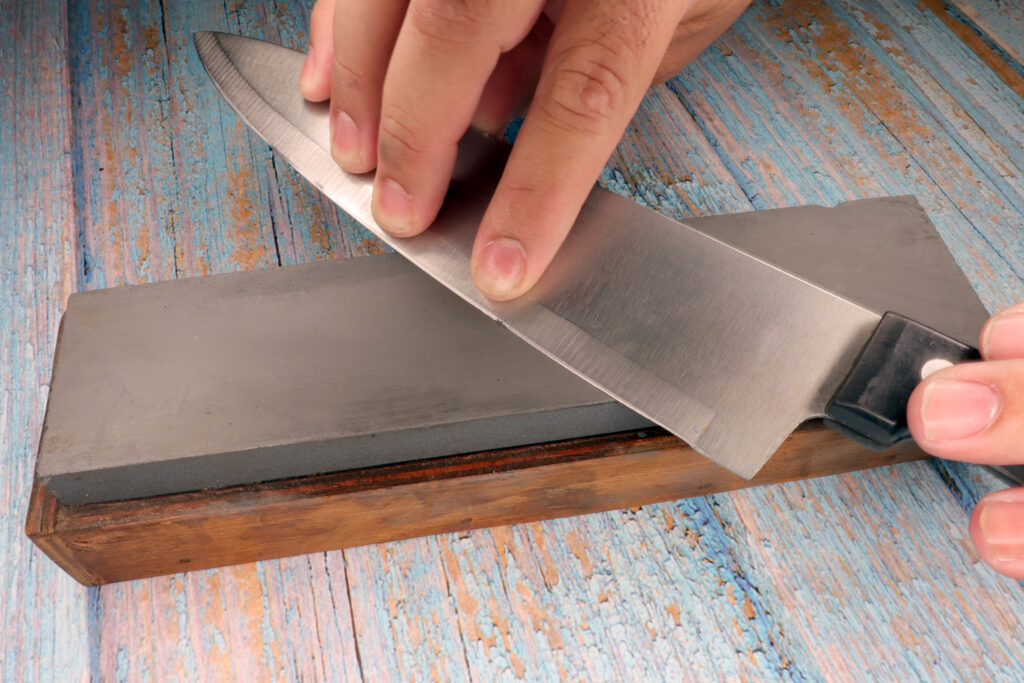
The Role of Cooling and Lubrication in Batch Grinding
Cooling and lubrication are critical components of the batch grinding process that often go overlooked. During grinding, friction generates heat, which can adversely affect both the blade material and the grinding equipment itself. Excessive heat can lead to warping or loss of temper in steel blades, compromising their performance and durability.
Therefore, implementing effective cooling strategies is essential for maintaining product quality. Using coolant fluids during grinding operations can significantly reduce heat buildup and prolong tool life. Coolants not only dissipate heat but also help remove debris from the grinding surface, ensuring a cleaner working environment.
Manufacturers should select coolants that are compatible with their specific materials and processes to achieve optimal results. Additionally, regular monitoring of coolant levels and properties is necessary to ensure consistent performance throughout production runs.
Managing Waste and Recycling in Small Knife Production
In any manufacturing process, waste management is an important consideration that can impact both profitability and environmental sustainability. In small knife production, waste can arise from various sources, including metal shavings from grinding operations and defective blades that do not meet quality standards. Implementing effective waste management strategies can help minimize these losses while promoting responsible practices.
One approach is to establish a recycling program for metal shavings generated during batch grinding. Many scrap metal dealers accept these materials for recycling, providing manufacturers with an opportunity to recoup some costs while reducing their environmental footprint. Additionally, manufacturers should consider implementing quality control measures to minimize defects during production, thereby reducing waste associated with rework or disposal of unsatisfactory products.
Quality Control Measures for Batch Grinding in Small-Scale Production
Quality control is an integral part of any manufacturing process, particularly in small-scale knife production where precision is paramount. Establishing robust quality control measures ensures that each batch of knives meets established standards for performance and safety. This involves implementing inspection protocols at various stages of production, from initial material selection to final product evaluation.
One effective quality control measure is to conduct regular inspections using calibrated measuring tools to assess blade dimensions and sharpness. By comparing these measurements against predetermined specifications, manufacturers can identify any deviations early in the process and take corrective action as needed. Additionally, maintaining detailed records of inspections can help track trends over time and inform future production decisions.
Optimizing Workflows and Organization for Batch Grinding
Optimizing workflows and organization is essential for enhancing productivity in batch grinding operations. A well-structured workflow minimizes bottlenecks and ensures that each stage of production flows smoothly into the next. To achieve this, manufacturers should analyze their current processes and identify areas for improvement.
One strategy is to implement lean manufacturing principles that focus on eliminating waste and maximizing value at every step of production. This may involve reorganizing workstations for better accessibility or cross-training employees to perform multiple tasks within the workflow. By fostering a culture of continuous improvement, manufacturers can create an environment where efficiency thrives and productivity increases.
Preventing Common Issues and Troubleshooting in Batch Grinding
Despite careful planning and execution, common issues may arise during batch grinding operations that can disrupt production or compromise product quality. Identifying potential problems early on is crucial for minimizing downtime and maintaining efficiency. Some common issues include uneven grinding results, excessive heat generation, or equipment malfunctions.
To prevent these issues, manufacturers should establish routine maintenance schedules for their grinding equipment to ensure optimal performance. Regularly checking for wear on grinding wheels or belts can help identify potential problems before they escalate into more significant issues. Additionally, training operators on troubleshooting techniques can empower them to address minor problems independently, reducing reliance on external support and keeping production on track.
Implementing Batch Grinding Tips for Small Knife Production
In conclusion, batch grinding presents an invaluable opportunity for small knife producers seeking to enhance their efficiency while maintaining high-quality standards. By carefully selecting appropriate equipment, establishing consistent processes, and implementing effective quality control measures, manufacturers can optimize their production capabilities significantly. Furthermore, attention to detail in areas such as cooling, lubrication, waste management, and workflow organization will contribute to a more streamlined operation.
As small knife producers navigate the complexities of batch grinding, embracing continuous improvement will be key to long-term success. By staying informed about best practices and adapting to evolving industry standards, manufacturers can position themselves as leaders in the competitive landscape of knife production. Ultimately, implementing these tips will not only improve operational efficiency but also elevate product quality—ensuring customer satisfaction and fostering brand loyalty in an ever-demanding market.
FAQs
What is batch grinding?
Batch grinding is the process of grinding a large quantity of material at once, typically in a single session or production run. This method is commonly used in manufacturing to efficiently produce a large number of products in a shorter amount of time.
Why is batch grinding important for small knife production runs?
Batch grinding is important for small knife production runs because it allows for consistent and efficient production of a large quantity of knife blanks or components. This method helps to maintain uniformity in the final products and can save time and labor costs.
What are some tips for batch grinding in small knife production runs?
Some tips for batch grinding in small knife production runs include using a high-quality grinding machine, ensuring proper blade sharpness and alignment, maintaining consistent pressure and speed during grinding, and regularly inspecting and cleaning the grinding equipment to ensure optimal performance.
What are the benefits of batch grinding for small knife production runs?
The benefits of batch grinding for small knife production runs include increased efficiency, consistent product quality, reduced labor costs, and the ability to meet high demand for knife products. Batch grinding also allows for better control over the production process and can lead to higher overall productivity.
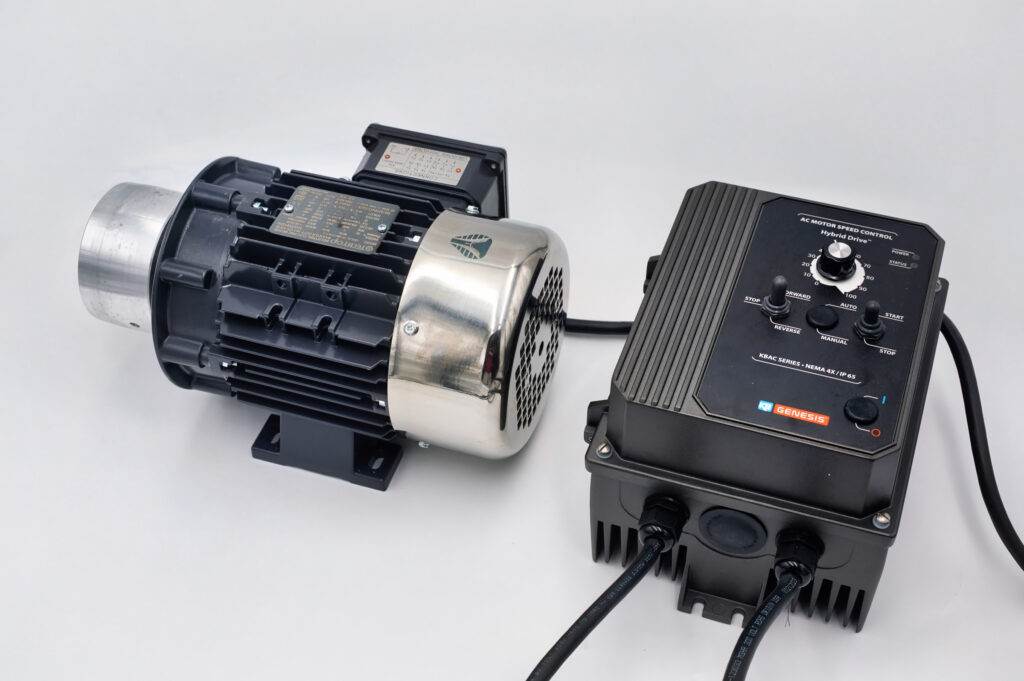