Aluminum has emerged as a material of choice in various maintenance applications due to its unique properties. One of the most significant advantages of aluminum is its lightweight nature, which makes it easier to handle and transport. This characteristic is particularly beneficial in maintenance tasks where mobility and accessibility are crucial.
Technicians can maneuver aluminum components with greater ease, reducing the physical strain associated with heavy materials. Additionally, the lightweight quality of aluminum allows for quicker installation and replacement processes, ultimately leading to enhanced efficiency in maintenance operations. Another notable advantage of aluminum is its resistance to corrosion.
Unlike many other metals, aluminum forms a protective oxide layer when exposed to air, which helps prevent rust and degradation over time. This property is especially valuable in environments where moisture and chemicals are prevalent, such as in marine or industrial settings. By utilizing aluminum in maintenance applications, organizations can significantly extend the lifespan of their equipment and reduce the frequency of repairs.
This durability not only contributes to lower maintenance costs but also ensures that operations run smoothly without the interruptions caused by equipment failure.
Key Takeaways
- Aluminum is lightweight, corrosion-resistant, and easy to work with, making it an ideal material for maintenance tasks.
- Aluminum’s high strength-to-weight ratio and malleability contribute to increased productivity in manufacturing processes.
- The use of aluminum in equipment and machinery can decrease downtime due to its durability and resistance to wear and tear.
- Aluminum is a sustainable and recyclable material, reducing environmental impact and promoting a greener approach to maintenance and manufacturing.
- The cost savings of using aluminum in maintenance and manufacturing are significant due to its longevity and low maintenance requirements.
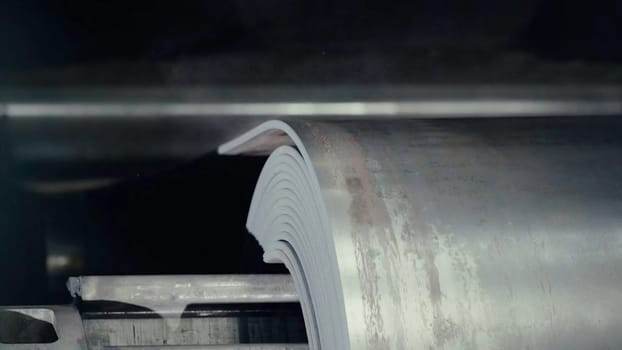
How Aluminum Increases Productivity in Manufacturing
The incorporation of aluminum into manufacturing processes has proven to be a game-changer for productivity. Its lightweight nature allows for faster assembly and disassembly of components, which is essential in a fast-paced manufacturing environment. When workers can quickly move parts and tools without the burden of heavy materials, they can focus on their tasks more effectively.
This efficiency translates into shorter production cycles and the ability to meet tight deadlines without compromising quality. Moreover, aluminum’s versatility enables manufacturers to create a wide range of products with varying specifications. This adaptability allows for customization and innovation, which are critical in today’s competitive market.
Manufacturers can experiment with different designs and applications without the constraints often associated with heavier materials. As a result, companies that leverage aluminum in their manufacturing processes can respond more swiftly to market demands, ultimately enhancing their overall productivity and profitability.
The Role of Aluminum in Decreasing Downtime
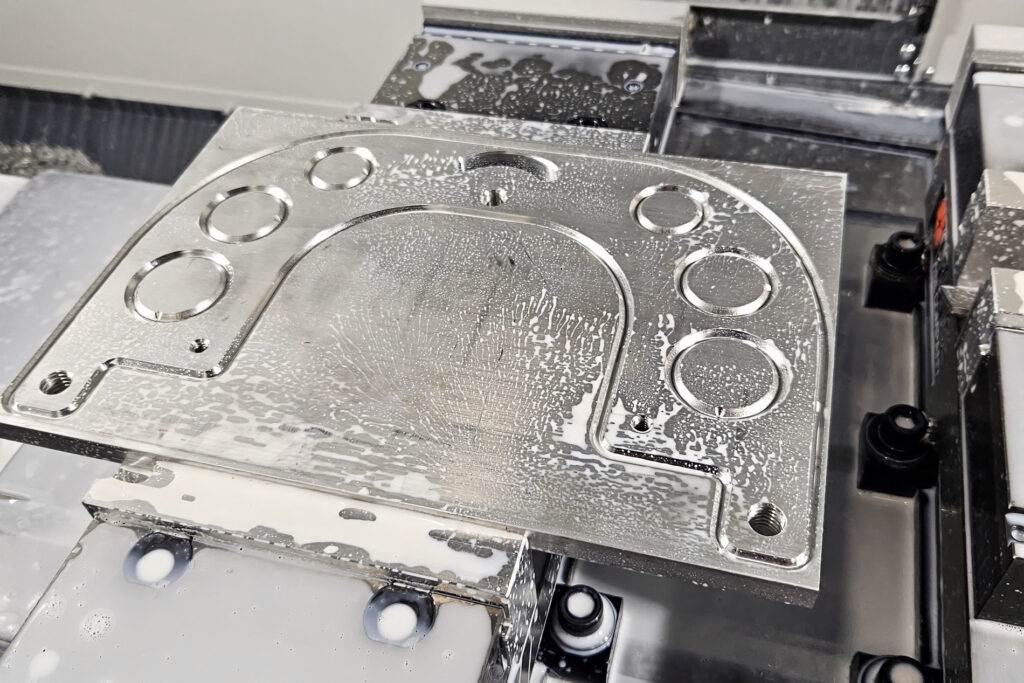
Downtime is a significant concern for any manufacturing or maintenance operation, as it directly impacts productivity and profitability. Aluminum plays a crucial role in minimizing downtime through its durability and ease of maintenance. Components made from aluminum are less prone to wear and tear compared to those made from other materials, which means they require less frequent replacement.
This longevity reduces the likelihood of unexpected breakdowns that can halt production lines and disrupt workflows. Additionally, when repairs are necessary, aluminum components are often easier to work with due to their lightweight nature. Technicians can quickly access and replace parts without extensive disassembly or heavy lifting.
This streamlined process not only saves time but also allows for quicker return-to-service for equipment. By reducing both the frequency and duration of downtime, organizations can maintain higher levels of productivity and ensure that their operations run smoothly.
The Environmental Benefits of Aluminum Use
Environmental Benefit | Explanation |
---|---|
Recyclability | Aluminum is 100% recyclable and can be recycled indefinitely without losing its quality. |
Energy Efficiency | Producing aluminum from recycled materials requires 95% less energy compared to using raw materials. |
Reduced Emissions | Aluminum production from recycled materials emits 95% less greenhouse gases compared to using raw materials. |
Resource Conservation | Recycling aluminum helps conserve natural resources and reduces the need for mining and extraction. |
The environmental impact of materials used in manufacturing and maintenance is becoming increasingly important in today’s world. Aluminum stands out as an environmentally friendly option due to its recyclability and lower energy consumption during production compared to other metals. The recycling process for aluminum requires only a fraction of the energy needed to produce new aluminum from raw materials, making it a sustainable choice for businesses looking to reduce their carbon footprint.
Furthermore, aluminum’s lightweight properties contribute to energy efficiency in transportation and logistics. When products are lighter, they require less fuel for transportation, leading to lower greenhouse gas emissions. By choosing aluminum for various applications, companies not only benefit from its performance characteristics but also contribute positively to environmental sustainability efforts.
This dual advantage positions aluminum as a responsible choice for organizations committed to reducing their ecological impact.
The Cost Savings of Using Aluminum in Maintenance
Cost efficiency is a primary concern for any organization, and aluminum offers significant savings in maintenance operations. While the initial investment in aluminum components may be higher than some alternatives, the long-term savings are substantial. The durability and corrosion resistance of aluminum lead to fewer replacements and repairs over time, which translates into lower overall maintenance costs.
Organizations can allocate their resources more effectively when they are not constantly addressing equipment failures or replacing worn-out parts. Additionally, the lightweight nature of aluminum reduces labor costs associated with handling and installation. Workers can complete tasks more quickly and with less physical strain, leading to increased productivity and reduced labor expenses.
The combination of lower material costs and decreased labor requirements makes aluminum an economically advantageous choice for maintenance applications, allowing organizations to maximize their budgets while maintaining high operational standards.
Aluminum’s Role in Improving Equipment Longevity
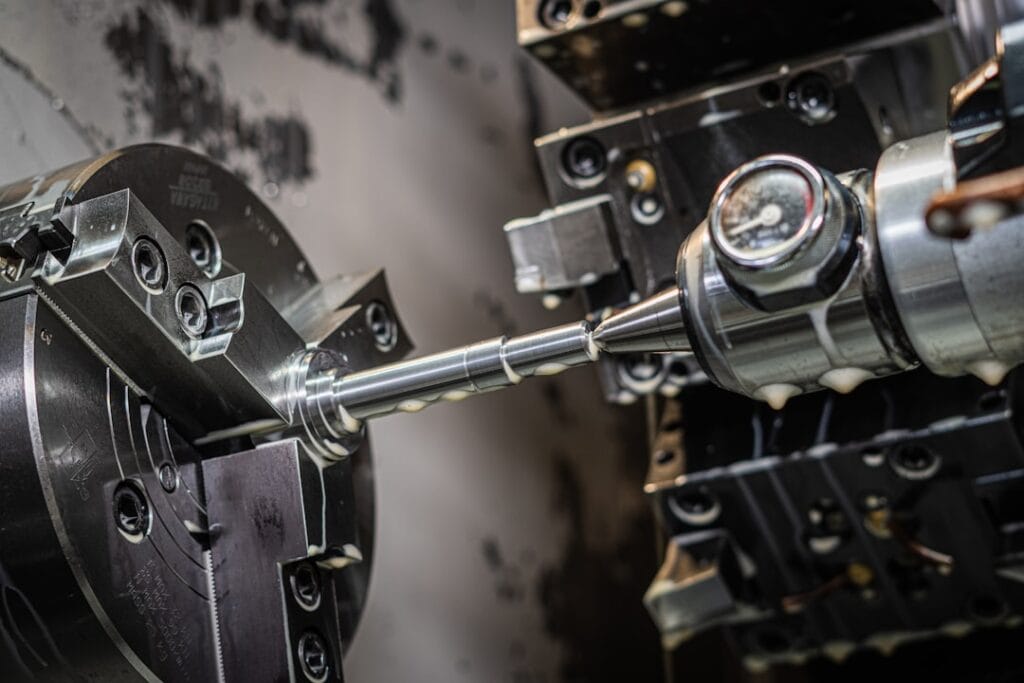
The longevity of equipment is a critical factor in maintaining operational efficiency and reducing costs over time. Aluminum contributes significantly to this aspect due to its inherent properties that resist wear and corrosion. Equipment made from aluminum tends to have a longer lifespan compared to those constructed from other materials, which means organizations can rely on their assets for extended periods without the need for frequent replacements.
Moreover, the lightweight nature of aluminum reduces stress on machinery during operation. This reduction in weight can lead to less wear on moving parts and components, further extending the life of the equipment. By investing in aluminum-based solutions, organizations not only enhance their operational capabilities but also ensure that their equipment remains functional for longer durations, ultimately leading to improved return on investment.
The Impact of Aluminum on Energy Efficiency
Energy efficiency is a critical consideration for modern manufacturing and maintenance operations, as it directly affects both costs and environmental impact. Aluminum plays a vital role in enhancing energy efficiency across various applications. Its lightweight properties contribute to reduced energy consumption during transportation and operation.
For instance, lighter machinery requires less energy to operate, leading to lower utility bills and reduced carbon emissions. In addition to its impact on transportation, aluminum’s thermal conductivity makes it an excellent choice for heat exchangers and other applications where temperature regulation is essential. Efficient heat transfer can lead to reduced energy consumption in heating and cooling processes, further enhancing overall energy efficiency within facilities.
By integrating aluminum into their operations, organizations can achieve significant energy savings while also contributing to sustainability goals.
The Future of Aluminum in Maintenance and Productivity
As industries continue to evolve, the role of aluminum in maintenance and productivity is expected to expand further. Innovations in manufacturing processes and advancements in material science are likely to enhance the properties of aluminum even more, making it an increasingly attractive option for various applications. The ongoing development of lightweight alloys and composites will open new avenues for utilizing aluminum in ways that were previously unimaginable.
Moreover, as sustainability becomes a central focus for businesses worldwide, the demand for environmentally friendly materials like aluminum will continue to rise. Companies that prioritize sustainable practices will find that aluminum aligns perfectly with their goals while also providing practical benefits such as cost savings and improved efficiency. As we look toward the future, it is clear that aluminum will play a pivotal role in shaping the landscape of maintenance and productivity across multiple industries, driving innovation while supporting environmental stewardship.
FAQs
What are the benefits of using aluminum in maintenance processes?
Aluminum is lightweight, corrosion-resistant, and durable, making it an ideal material for reducing maintenance downtime and increasing productivity.
How does aluminum contribute to decreased maintenance downtime?
Aluminum’s corrosion resistance and durability reduce the need for frequent maintenance and repairs, leading to decreased downtime and increased productivity.
What industries can benefit from using aluminum for maintenance purposes?
Various industries such as aerospace, automotive, construction, and manufacturing can benefit from using aluminum for maintenance purposes due to its lightweight and durable properties.
How does aluminum contribute to increased productivity?
By reducing maintenance downtime and the need for frequent repairs, aluminum allows for increased productivity as equipment and machinery can operate for longer periods without interruptions.