Corrosion is a natural process that occurs when metals react with their environment, leading to deterioration and degradation. In tough environments, such as those found in industrial settings, the risk of corrosion is significantly heightened due to factors like moisture, chemicals, and extreme temperatures. Understanding the mechanisms of corrosion is crucial for industries that rely on metal components, as it can lead to equipment failure, increased maintenance costs, and safety hazards.
The impact of corrosion can be particularly severe in applications where precision and reliability are paramount. In many cases, corrosion can manifest in various forms, including uniform corrosion, pitting, crevice corrosion, and galvanic corrosion. Each type presents unique challenges and requires specific strategies for prevention and mitigation.
For instance, pitting corrosion can create small holes in metal surfaces, which may go unnoticed until significant damage has occurred. Therefore, industries must adopt a proactive approach to corrosion management, utilizing materials and technologies designed to withstand harsh conditions. This is where advancements in manufacturing processes, such as those offered by TorusCNC 2×72 Grinders, come into play, providing solutions that enhance the durability of metal components.
Key Takeaways
- Corrosion in tough environments can be better understood by examining the factors that contribute to it, such as moisture, temperature, and chemical exposure.
- Aluminum CNC grinders offer benefits such as lightweight construction, precision grinding, and resistance to corrosion and oxidation.
- Durability and longevity in harsh conditions can be achieved through the use of high-quality materials and advanced manufacturing techniques.
- Resistance to corrosion and oxidation is essential for industrial equipment that is exposed to challenging environments.
- Quality materials are crucial in industrial settings to ensure reliability, longevity, and performance in tough conditions.
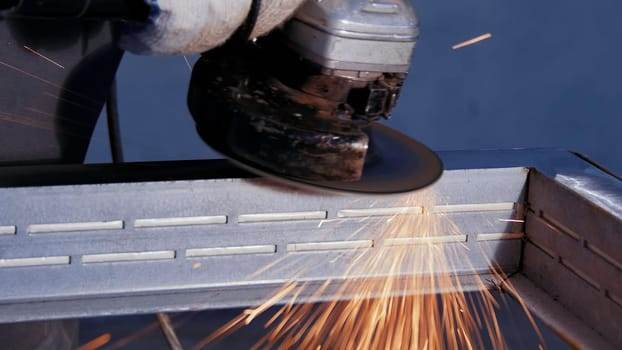
The Benefits of Aluminum CNC Grinders
Aluminum CNC grinders have gained popularity in various industrial applications due to their unique properties and advantages. One of the primary benefits of using aluminum in CNC grinding is its lightweight nature. This characteristic not only makes handling and maneuvering easier but also contributes to reduced energy consumption during operation.
The efficiency gained from using aluminum can lead to significant cost savings over time, making it an attractive option for manufacturers looking to optimize their processes. Moreover, aluminum’s excellent machinability allows for precise and intricate designs that are essential in modern manufacturing. CNC grinders made from aluminum can achieve high tolerances and surface finishes, which are critical for producing high-quality components.
The versatility of aluminum also means that it can be easily adapted for various applications, from aerospace to automotive industries. As companies like TorusCNC continue to innovate in the field of CNC grinding, the benefits of aluminum become increasingly evident, providing manufacturers with tools that enhance productivity and performance.
Durability and Longevity in Harsh Conditions
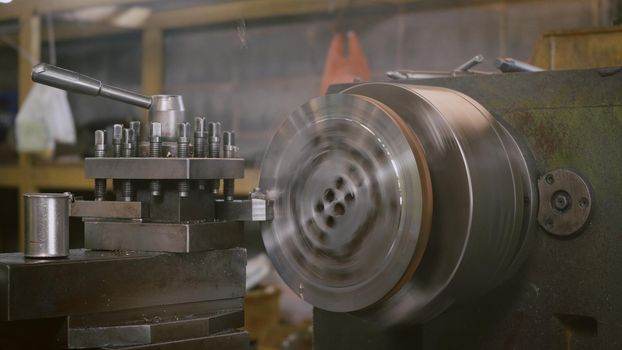
Durability is a key consideration when selecting equipment for use in harsh environments. Aluminum CNC grinders are engineered to withstand the rigors of demanding applications while maintaining their performance over time. The inherent strength of aluminum, combined with advanced manufacturing techniques employed by companies like TorusCNC, results in grinders that can endure heavy use without compromising their structural integrity.
This durability translates into longer service life and reduced downtime for maintenance or replacement. In addition to their robust construction, aluminum CNC grinders are designed with features that enhance their longevity. For instance, many models incorporate advanced cooling systems that prevent overheating during extended operation.
This is particularly important in environments where high temperatures can accelerate wear and tear on equipment. By investing in durable aluminum grinders, manufacturers can ensure that their operations run smoothly even in the most challenging conditions, ultimately leading to increased productivity and profitability.
Resistance to Corrosion and Oxidation
Material | Resistance to Corrosion | Resistance to Oxidation |
---|---|---|
Stainless Steel | High | High |
Aluminum | Low | Low |
Titanium | High | High |
One of the standout features of aluminum is its natural resistance to corrosion and oxidation. When exposed to air, aluminum forms a thin layer of aluminum oxide on its surface, which acts as a protective barrier against further corrosion. This property makes aluminum an ideal choice for CNC grinders used in environments where exposure to moisture or corrosive substances is a concern.
By utilizing aluminum in their designs, companies like TorusCNC provide equipment that not only performs well but also stands up to the challenges posed by harsh conditions. The resistance to corrosion and oxidation not only extends the lifespan of aluminum CNC grinders but also reduces maintenance requirements. In industries where downtime can be costly, having equipment that requires less frequent servicing is a significant advantage.
Additionally, the aesthetic appeal of aluminum remains intact over time, as it does not suffer from unsightly rust or degradation that can occur with other materials. This combination of performance and appearance makes aluminum CNC grinders a smart investment for businesses looking to enhance their operational efficiency.
The Importance of Quality Materials in Industrial Settings
In industrial settings, the choice of materials used in manufacturing equipment can have far-reaching implications for performance and reliability. High-quality materials contribute to the overall effectiveness of machinery and tools, ensuring they can withstand the demands of rigorous applications. Companies like TorusCNC prioritize the use of premium materials in their CNC grinders, recognizing that the longevity and functionality of their products depend on it.
Using quality materials not only enhances the durability of equipment but also improves safety in industrial environments. Inferior materials can lead to equipment failure, posing risks to operators and potentially causing costly accidents. By investing in high-quality aluminum CNC grinders, manufacturers can mitigate these risks while ensuring that their operations run smoothly and efficiently.
The emphasis on quality materials is a hallmark of reputable manufacturers who understand the critical role they play in maintaining productivity and safety.
Maintaining Performance in Challenging Environments
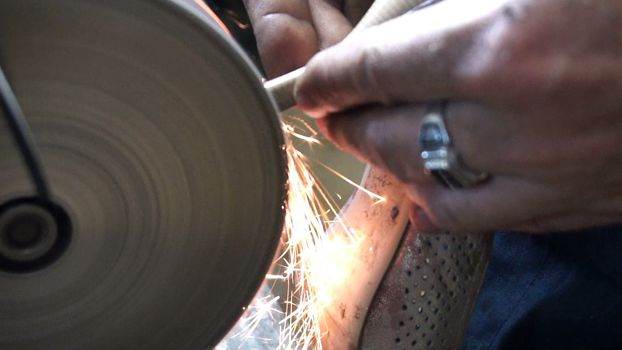
Maintaining optimal performance in challenging environments requires a combination of quality equipment and effective maintenance practices. Aluminum CNC grinders are designed with this principle in mind, offering features that facilitate ease of use and upkeep. Regular maintenance routines are essential for ensuring that these machines continue to operate at peak efficiency, even under demanding conditions.
One key aspect of maintaining performance is regular inspection and cleaning of the equipment. Dust and debris can accumulate over time, potentially affecting the grinder’s functionality. By implementing a proactive maintenance schedule that includes routine checks and cleaning procedures, operators can identify potential issues before they escalate into more significant problems.
This approach not only prolongs the life of the equipment but also ensures consistent performance levels throughout its operational lifespan.
Comparing Aluminum CNC Grinders to Other Materials
While there are various materials available for CNC grinders, aluminum stands out due to its unique combination of properties that cater specifically to industrial needs. Unlike steel or other metals that may be heavier or more prone to rusting, aluminum offers a lightweight alternative without sacrificing strength or durability. This makes it particularly advantageous for applications where mobility and ease of handling are essential.
Furthermore, aluminum’s resistance to corrosion sets it apart from many other materials commonly used in industrial settings. While steel may require additional coatings or treatments to protect against rust, aluminum’s natural oxide layer provides inherent protection without the need for extra measures. This not only simplifies maintenance but also enhances the overall reliability of aluminum CNC grinders in tough environments.
Ensuring Reliability and Confidence in Tough Environments
Reliability is paramount in industrial operations where equipment failure can lead to significant downtime and financial losses. Aluminum CNC grinders from manufacturers like TorusCNC are engineered with reliability in mind, incorporating advanced design features that ensure consistent performance even under challenging conditions. The confidence that comes from using reliable equipment allows operators to focus on their tasks without worrying about unexpected breakdowns.
Moreover, investing in high-quality aluminum CNC grinders instills confidence among operators regarding safety and efficiency. Knowing that their tools are built to withstand harsh environments enables workers to perform their duties with assurance, ultimately contributing to a more productive workplace. As industries continue to evolve and face new challenges, the importance of reliable equipment cannot be overstated; it is a cornerstone of operational success in any demanding environment.
In conclusion, understanding corrosion in tough environments is essential for industries reliant on metal components. The benefits of aluminum CNC grinders are numerous, including their lightweight nature, durability, resistance to corrosion, and overall performance in challenging conditions. By prioritizing quality materials and effective maintenance practices, manufacturers can ensure that their operations remain efficient and reliable over time.
As companies like TorusCNC continue to innovate within this space, the future looks promising for those seeking dependable solutions for their industrial needs.
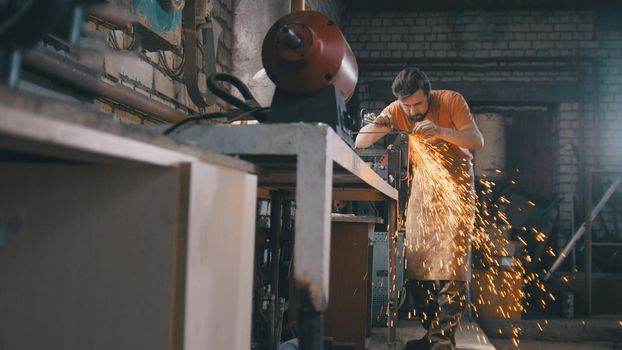
FAQs
What are the benefits of owning an aluminum CNC grinder in humid or harsh environments?
Owning an aluminum CNC grinder in humid or harsh environments offers the benefit of corrosion resistance, ensuring the longevity and durability of the equipment. Aluminum is known for its resistance to rust and corrosion, making it an ideal choice for use in challenging environmental conditions.
How does aluminum compare to other materials in terms of corrosion resistance?
Aluminum is highly resistant to corrosion compared to other materials such as steel or iron. It forms a protective oxide layer on its surface, which helps prevent rust and corrosion, making it a preferred choice for equipment used in humid or harsh environments.
What maintenance is required for an aluminum CNC grinder in humid or harsh environments?
While aluminum is highly resistant to corrosion, regular cleaning and maintenance are still important to ensure the optimal performance and longevity of the CNC grinder. This may include wiping down the equipment to remove any buildup of dirt or debris, as well as applying protective coatings or lubricants as needed.
Are there any specific considerations for using an aluminum CNC grinder in humid or harsh environments?
When using an aluminum CNC grinder in humid or harsh environments, it is important to ensure that the equipment is properly sealed and protected from moisture and other environmental factors. Additionally, regular inspections and maintenance should be conducted to identify and address any potential issues before they escalate.
What industries or applications can benefit from owning an aluminum CNC grinder in humid or harsh environments?
Industries and applications that operate in humid or harsh environments, such as marine, aerospace, automotive, and outdoor manufacturing, can benefit from owning an aluminum CNC grinder. The corrosion resistance of aluminum makes it well-suited for use in these challenging conditions, ensuring reliable performance and longevity.