Precision in aluminum fabrication is a critical aspect that influences the overall quality and performance of the final product. Aluminum, known for its lightweight and corrosion-resistant properties, is widely used in various industries, including aerospace, automotive, and construction. The need for precision arises from the fact that even the slightest deviation in measurements can lead to significant issues in functionality and aesthetics.
When working with aluminum, achieving exact dimensions and tolerances is essential to ensure that components fit together seamlessly and perform as intended. Moreover, precision in aluminum fabrication extends beyond mere measurements. It encompasses the entire process, from design to production.
Advanced techniques and technologies are employed to ensure that every cut, bend, and weld is executed with meticulous attention to detail. This level of precision not only enhances the structural integrity of the aluminum frames but also contributes to their overall longevity. As industries continue to evolve and demand higher standards, understanding the nuances of precision in aluminum becomes increasingly important for manufacturers and consumers alike.
Key Takeaways
- Precision in aluminum fabrication is crucial for achieving high-quality results and ensuring the durability of the final product.
- CNC-cut frames offer advantages such as increased accuracy, consistency, and the ability to create complex designs with ease.
- CNC-cut aluminum frames deliver superior results in terms of precision, quality, and overall performance compared to traditional fabrication methods.
- The importance of precision in aluminum fabrication cannot be overstated, as it directly impacts the durability and longevity of the frames.
- CNC technology plays a crucial role in aluminum frame manufacturing by enabling precise and efficient production processes.
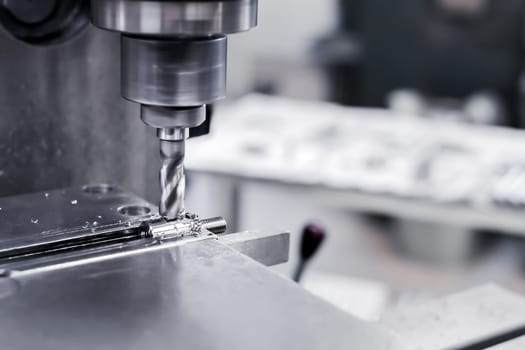
The Advantages of CNC-Cut Frames
CNC-cut frames offer a multitude of advantages that set them apart from traditional manufacturing methods. One of the most significant benefits is the ability to achieve high levels of accuracy and repeatability. Computer Numerical Control (CNC) technology allows for precise programming of cutting tools, ensuring that each frame is produced with consistent dimensions and specifications.
This level of accuracy is particularly crucial in applications where components must fit together perfectly, such as in machinery or structural assemblies. In addition to accuracy, CNC-cut frames also provide enhanced efficiency in the manufacturing process. The automation involved in CNC machining reduces the time required for production while minimizing human error.
This efficiency translates into cost savings for manufacturers, as they can produce more frames in less time without compromising quality. Furthermore, CNC technology allows for complex designs to be executed with ease, enabling manufacturers to push the boundaries of creativity while maintaining precision.
The Superior Results of CNC-Cut Aluminum Frames
The results achieved through CNC-cut aluminum frames are often superior to those produced by traditional methods. The precision offered by CNC machining ensures that each frame meets stringent quality standards, resulting in products that are not only visually appealing but also structurally sound. The smooth finishes and clean edges characteristic of CNC-cut frames enhance their aesthetic value, making them suitable for a wide range of applications, from architectural elements to custom furniture.
Additionally, the superior results of CNC-cut aluminum frames extend to their performance characteristics. The consistent quality achieved through CNC machining contributes to improved strength and durability. When components are manufactured with precision, they are less likely to experience issues such as warping or misalignment over time.
This reliability is particularly important in industries where safety and performance are paramount, as it ensures that the frames can withstand the rigors of their intended use without compromising integrity.
The Importance of Precision in Aluminum Fabrication
Aspect | Importance |
---|---|
Accuracy | Ensures the final product meets specifications |
Quality | Impacts the strength and durability of the fabricated aluminum |
Cost-effectiveness | Reduces material waste and rework |
Customer satisfaction | Delivers products that meet or exceed customer expectations |
Precision plays a pivotal role in aluminum fabrication, influencing not only the quality of the final product but also the efficiency of the manufacturing process. In industries where aluminum components are used, such as aerospace and automotive, even minor inaccuracies can lead to catastrophic failures. Therefore, manufacturers must prioritize precision at every stage of production, from initial design through to final assembly.
Moreover, precision in aluminum fabrication is essential for meeting regulatory standards and customer expectations. Many industries have strict guidelines regarding tolerances and specifications that must be adhered to in order to ensure safety and functionality. By focusing on precision, manufacturers can not only comply with these regulations but also build a reputation for quality and reliability in their products.
This commitment to precision ultimately fosters trust among customers and partners, leading to long-term business success.
The Role of CNC Technology in Aluminum Frame Manufacturing
CNC technology has revolutionized aluminum frame manufacturing by introducing a level of automation and precision previously unattainable with manual methods. The ability to program machines with exact specifications allows manufacturers to produce complex shapes and designs with ease. This technological advancement has opened up new possibilities for innovation in aluminum frame design, enabling manufacturers to create products that meet the evolving needs of various industries.
Furthermore, CNC technology enhances the overall efficiency of the manufacturing process. With automated cutting and shaping, production times are significantly reduced, allowing manufacturers to respond quickly to market demands. This agility is particularly beneficial in industries where trends change rapidly or where custom orders are common.
By leveraging CNC technology, manufacturers can maintain a competitive edge while ensuring that their aluminum frames meet the highest standards of quality and precision.
The Impact of Precision on Aluminum Frame Durability
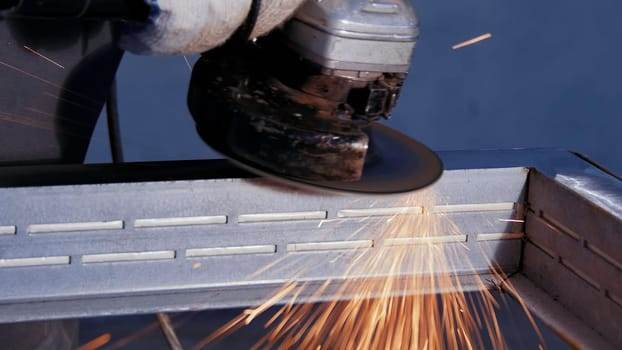
The impact of precision on the durability of aluminum frames cannot be overstated. When frames are manufactured with high levels of accuracy, they exhibit improved structural integrity and resistance to wear and tear over time. Precision ensures that joints are properly aligned and that materials are cut to exact specifications, reducing the likelihood of stress points that could lead to failure under load.
Additionally, precise fabrication techniques contribute to better surface finishes, which play a crucial role in protecting aluminum from environmental factors such as moisture and corrosion. A well-finished frame is less susceptible to damage from external elements, thereby extending its lifespan. In applications where durability is critical—such as in outdoor structures or high-stress environments—precision becomes a key factor in ensuring that aluminum frames perform reliably over time.
Comparing CNC-Cut Aluminum Frames to Traditional Methods
When comparing CNC-cut aluminum frames to those produced through traditional methods, the differences become apparent in terms of quality, efficiency, and versatility. Traditional manufacturing techniques often rely on manual labor for cutting and shaping materials, which can introduce variability and inconsistencies in the final product. In contrast, CNC-cut frames benefit from automated processes that ensure uniformity and precision across all units produced.
Moreover, CNC technology allows for greater design flexibility compared to traditional methods. Manufacturers can easily modify designs or create intricate patterns without significant retooling or downtime. This adaptability is particularly advantageous in today’s fast-paced market, where customization is increasingly demanded by consumers.
As a result, CNC-cut aluminum frames not only meet high standards of quality but also cater to diverse customer needs more effectively than their traditionally manufactured counterparts.
The Future of Precision in Aluminum Fabrication
The future of precision in aluminum fabrication looks promising as advancements in technology continue to reshape the industry landscape. Innovations such as artificial intelligence and machine learning are beginning to play a role in optimizing manufacturing processes further. These technologies can analyze data from production runs to identify areas for improvement, leading to even greater levels of precision and efficiency.
Additionally, as sustainability becomes a more pressing concern across industries, precision fabrication techniques will be essential in minimizing waste and maximizing resource utilization. By ensuring that materials are cut and shaped with exactness, manufacturers can reduce scrap rates and lower their environmental impact. As the demand for high-quality aluminum products continues to grow, embracing precision will be key for manufacturers looking to thrive in an increasingly competitive market.
In conclusion, understanding precision in aluminum fabrication is vital for achieving superior results in manufacturing processes. The advantages offered by CNC-cut frames highlight the importance of accuracy and efficiency in producing high-quality products that meet industry standards. As technology continues to evolve, the role of precision will only become more significant, shaping the future of aluminum fabrication for years to come.
FAQs
What are CNC-cut aluminum frames?
CNC-cut aluminum frames are frames that are manufactured using computer numerical control (CNC) machines to precisely cut and shape aluminum material according to specific design specifications.
Why are CNC-cut aluminum frames preferred for holding tight tolerances?
CNC-cut aluminum frames are preferred for holding tight tolerances because the precision and accuracy of CNC machines allow for consistent and exact cutting of the aluminum material, resulting in frames that meet strict dimensional requirements.
How do CNC-cut aluminum frames lead to superior results?
CNC-cut aluminum frames lead to superior results due to their ability to maintain tight tolerances, which ensures that the frames are structurally sound, have uniform dimensions, and provide a high-quality finish.
What industries benefit from using CNC-cut aluminum frames?
Industries such as aerospace, automotive, electronics, and manufacturing benefit from using CNC-cut aluminum frames due to their ability to meet stringent quality and performance standards.
What are the advantages of using CNC-cut aluminum frames over other materials?
The advantages of using CNC-cut aluminum frames over other materials include their lightweight yet durable nature, corrosion resistance, and the ability to be easily machined to precise specifications, making them ideal for a wide range of applications.