Precision grinding is a critical process in the manufacturing of hardened dies and punches, particularly when utilizing a 2×72 grinder. This method ensures that the components achieve the necessary hardness and durability required for their intended applications. The significance of precision grinding lies in its ability to produce parts with exceptional dimensional accuracy and surface finish.
In industries where tolerances are tight and performance is paramount, the role of precision grinding cannot be overstated. It allows manufacturers to create dies and punches that not only meet but often exceed industry standards. Moreover, the process of precision grinding enhances the longevity of these tools.
Hardened dies and punches are subjected to extreme conditions during their operational life, including high pressures and abrasive materials. By employing precision grinding techniques, manufacturers can ensure that these tools maintain their integrity over time. The result is a reduction in wear and tear, leading to fewer replacements and lower overall production costs.
Thus, understanding the importance of precision grinding is essential for anyone involved in the production of hardened dies and punches.
Key Takeaways
- Precision grinding is crucial for achieving tight tolerances and uniform surface finish in hardened dies and punches for 2×72 applications.
- Selecting the right grinding wheel is essential for efficient and effective grinding of hardened dies and punches.
- Coolant plays a critical role in precision grinding by reducing heat and friction, and improving surface finish and tool life.
- Consistent grinding pressure is necessary for maintaining uniform surface finish and achieving tight tolerances in precision grinding.
- Post-grinding inspection and quality control are important steps to ensure the accuracy and quality of hardened dies and punches in 2×72 applications.
Selecting the Right Grinding Wheel for Hardened Dies & Punches
Choosing the appropriate grinding wheel is a fundamental step in the precision grinding process for hardened dies and punches. The selection process involves considering various factors, including the material composition of the die or punch, the desired finish, and the specific grinding operation being performed. Different grinding wheels are designed for different applications, and using the wrong type can lead to suboptimal results or even damage to the workpiece.
For instance, diamond wheels are often preferred for grinding hard materials due to their superior hardness and wear resistance. In addition to material compatibility, the grit size of the grinding wheel plays a crucial role in achieving the desired surface finish. Finer grits are typically used for finishing operations, while coarser grits are more suitable for stock removal.
It is also essential to consider the bond type of the wheel, as this affects its durability and performance under various conditions. A well-chosen grinding wheel not only enhances efficiency but also contributes to achieving tighter tolerances and better overall quality in hardened dies and punches.
The Role of Coolant in Precision Grinding for Hardened Dies & Punches
Coolant plays a vital role in the precision grinding process, particularly when working with hardened dies and punches. The primary function of coolant is to dissipate heat generated during grinding, which can adversely affect both the workpiece and the grinding wheel. Excessive heat can lead to thermal damage, altering the hardness of the material and potentially compromising its structural integrity.
By using an appropriate coolant, manufacturers can maintain optimal temperatures throughout the grinding process, ensuring that both the tool and workpiece remain within acceptable limits. Additionally, coolant serves to lubricate the grinding interface, reducing friction between the wheel and the workpiece. This lubrication not only enhances the efficiency of the grinding operation but also contributes to achieving a superior surface finish.
Furthermore, coolant helps to flush away debris and metal particles generated during grinding, preventing them from interfering with the process. In summary, incorporating coolant into precision grinding operations is essential for maintaining quality and extending tool life when working with hardened dies and punches.
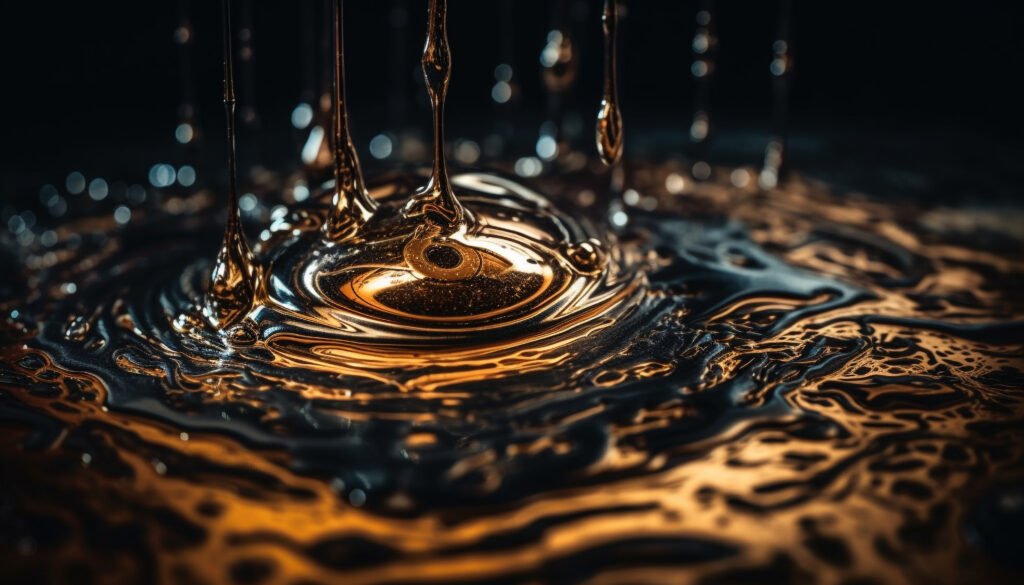
Techniques for Achieving Uniform Surface Finish in Precision Grinding
Achieving a uniform surface finish in precision grinding requires a combination of techniques and best practices tailored to the specific requirements of hardened dies and punches. One effective approach is to employ a systematic grinding strategy that includes multiple passes with varying wheel grits. Starting with a coarser grit allows for efficient material removal, while subsequent passes with finer grits refine the surface finish.
This method not only enhances uniformity but also minimizes the risk of introducing defects such as chatter marks or uneven surfaces. Another critical technique involves controlling the grinding parameters, including speed, feed rate, and depth of cut. By carefully adjusting these variables, operators can optimize the grinding process to achieve a consistent finish across the entire surface area of the workpiece.
Additionally, maintaining a stable setup with minimal vibration is essential for preventing inconsistencies in surface quality. Implementing these techniques ensures that hardened dies and punches meet stringent quality standards while maximizing productivity.
Maintaining Consistent Grinding Pressure for Hardened Dies & Punches
Consistent grinding pressure is crucial for achieving optimal results in precision grinding operations involving hardened dies and punches. Variations in pressure can lead to uneven wear on the grinding wheel and inconsistent material removal rates, ultimately affecting the quality of the finished product. To maintain consistent pressure, operators must monitor several factors, including wheel wear, workpiece characteristics, and machine settings.
Regularly checking these parameters helps ensure that pressure remains within an acceptable range throughout the grinding process. Moreover, employing automated systems or feedback mechanisms can significantly enhance pressure consistency. These systems can adjust parameters in real-time based on feedback from sensors monitoring pressure levels during grinding.
By implementing such technologies, manufacturers can achieve greater precision and reliability in their operations. Ultimately, maintaining consistent grinding pressure is essential for producing high-quality hardened dies and punches that meet demanding specifications.
Achieving Tight Tolerances in Precision Grinding for Hardened Dies & Punches
Achieving tight tolerances in precision grinding is a fundamental requirement when working with hardened dies and punches. Tolerances refer to the allowable variations in dimensions that ensure parts fit together correctly and function as intended. In many applications, especially those involving intricate designs or complex assemblies, even minor deviations can lead to significant issues down the line.
Therefore, it is imperative that manufacturers employ precise techniques to meet these stringent requirements. One effective method for achieving tight tolerances is through careful planning of the grinding process. This includes selecting appropriate tools, optimizing machine settings, and implementing rigorous inspection protocols throughout production.
Additionally, utilizing advanced technologies such as CNC (Computer Numerical Control) systems can enhance precision by automating movements and reducing human error. By focusing on these aspects, manufacturers can consistently produce hardened dies and punches that adhere to tight tolerances while maintaining high levels of efficiency.
Dressing the Grinding Wheel for Optimal Performance in Precision Grinding
Dressing the grinding wheel is an essential practice that significantly impacts its performance during precision grinding operations for hardened dies and punches. Over time, grinding wheels can become glazed or loaded with material, which diminishes their cutting efficiency and affects surface finish quality. Dressing involves removing this buildup and reshaping the wheel’s surface to restore its cutting capabilities.
This process not only enhances performance but also prolongs the life of the wheel. There are various methods for dressing grinding wheels, including mechanical dressing tools and diamond dressers. Each method has its advantages depending on factors such as wheel type and desired finish.
Regularly dressing wheels ensures that they maintain optimal sharpness and cutting action, which is particularly important when working with hard materials like those used in dies and punches. By incorporating dressing into routine maintenance practices, manufacturers can achieve consistent results in their precision grinding operations.
Balancing Speed and Feed Rates for Efficient Precision Grinding
Balancing speed and feed rates is crucial for achieving efficiency in precision grinding processes involving hardened dies and punches. The speed at which the grinding wheel rotates (spindle speed) must be carefully matched with the rate at which the workpiece is fed into it (feed rate). An optimal balance between these two parameters ensures effective material removal while minimizing heat generation and wear on both the tool and workpiece.
If spindle speed is too high relative to feed rate, it can lead to excessive heat buildup, resulting in thermal damage to both components. Conversely, if feed rate is too high compared to spindle speed, it may cause inefficient cutting action or even stall the machine. Therefore, operators must conduct thorough testing to determine ideal settings based on specific materials and desired outcomes.
By achieving this balance, manufacturers can enhance productivity while maintaining high-quality standards in their precision grinding operations.
Using Jigs and Fixtures for Precise Positioning in Precision Grinding
The use of jigs and fixtures is instrumental in ensuring precise positioning during precision grinding operations for hardened dies and punches. These tools provide stability and repeatability by securely holding workpieces in place throughout the grinding process. Proper positioning is essential for achieving accurate dimensions and surface finishes; any movement or misalignment can lead to defects or inconsistencies.
Jigs are typically designed for specific tasks or shapes, allowing operators to quickly set up their machines without extensive adjustments each time a new part is processed. Fixtures serve a similar purpose but may be more versatile in accommodating various workpieces. By utilizing jigs and fixtures effectively, manufacturers can streamline their operations while enhancing accuracy in producing hardened dies and punches.
Post-Grinding Inspection and Quality Control for Hardened Dies & Punches
Post-grinding inspection is a critical step in ensuring that hardened dies and punches meet quality standards after precision grinding operations are completed. This phase involves thorough examination using various measurement tools such as calipers, micrometers, or coordinate measuring machines (CMM). Inspecting dimensions against specified tolerances helps identify any deviations early on, allowing for corrective actions before parts are sent out for use.
Quality control processes should also include assessments of surface finish quality through visual inspections or specialized equipment like profilometers. By implementing rigorous post-grinding inspection protocols, manufacturers can maintain high levels of quality assurance while minimizing waste associated with rework or scrap parts. Ultimately, effective quality control measures contribute significantly to customer satisfaction by ensuring that only top-quality hardened dies and punches reach end-users.
Advantages of Precision Grinding for Hardened Dies & Punches in 2×72 Applications
The advantages of precision grinding for hardened dies and punches in 2×72 applications are manifold. First and foremost, this method allows for exceptional dimensional accuracy that is crucial in industries where precision is non-negotiable. The ability to achieve tight tolerances ensures that components fit together seamlessly within larger assemblies or systems, enhancing overall functionality.
Additionally, precision grinding contributes to improved surface finishes that reduce friction during operation—an essential factor when dealing with high-performance tools like dies and punches. A smoother surface not only enhances tool life but also minimizes wear on mating components during use. Furthermore, by employing advanced techniques such as CNC programming alongside traditional methods within a 2×72 framework, manufacturers can optimize their processes for greater efficiency without sacrificing quality.
In conclusion, precision grinding plays an indispensable role in producing high-quality hardened dies and punches within 2×72 applications. From selecting appropriate wheels to maintaining consistent pressure throughout operations—each aspect contributes significantly toward achieving desired outcomes while ensuring longevity in tool performance.
FAQs
What is a 2×72 grinder?
A 2×72 grinder is a type of belt grinder that uses a 2-inch by 72-inch belt for grinding, sharpening, and shaping metal and other materials. It is commonly used in metalworking and knife making.
What are hardened dies and punches?
Hardened dies and punches are metal tools used in manufacturing processes to cut, shape, or form materials such as metal, plastic, or wood. They are made from hardened steel to withstand the high pressure and wear associated with their use.
Why is grinding hardened dies and punches challenging?
Grinding hardened dies and punches is challenging because the hardened steel material is very tough and resistant to abrasion. It requires specialized grinding techniques and equipment to effectively shape and sharpen these tools without damaging them.
How is a 2×72 grinder used for grinding hardened dies and punches?
A 2×72 grinder is used for grinding hardened dies and punches by using the abrasive belt to remove material and shape the tools to the desired dimensions. The grinder allows for precise control and shaping of the hardened steel, making it suitable for this challenging task.
What are the benefits of using a 2×72 grinder for grinding hardened dies and punches?
Using a 2×72 grinder for grinding hardened dies and punches offers benefits such as precision, control, and efficiency in shaping and sharpening the tools. The grinder allows for the removal of material while maintaining the integrity and hardness of the dies and punches.