In the realm of manufacturing and industrial processes, the choice of materials can significantly influence both efficiency and product quality. Among the various options available, glass-lined platens have emerged as a noteworthy alternative to traditional metal platens. These specialized surfaces are coated with a layer of glass, providing unique properties that enhance their performance in various applications.
The introduction of glass-lined platens marks a pivotal shift in how industries approach heat transfer, chemical resistance, and overall durability in their production processes. Glass-lined platens are particularly valued in sectors such as food processing, pharmaceuticals, and chemical manufacturing, where cleanliness and resistance to corrosion are paramount. The smooth, non-porous surface of glass not only facilitates easy cleaning but also minimizes the risk of contamination.
As industries continue to evolve and demand higher standards of quality and safety, understanding the advantages and potential drawbacks of glass-lined platens becomes essential for making informed decisions about equipment upgrades.
Key Takeaways
- Glass-lined platens offer superior heat transfer and resistance to corrosion, making them ideal for various industrial applications.
- The benefits of glass-lined platens include improved product quality, reduced maintenance costs, and increased operational efficiency.
- While the initial cost of glass-lined platens may be higher than traditional platens, the long-term cost savings and durability make them a cost-effective choice.
- Glass-lined platens are highly durable and have a longer lifespan compared to traditional platens, reducing the need for frequent replacements.
- Upgrading to glass-lined platens can have a positive impact on product quality, ensuring consistent and uniform heat distribution for better end results.
Benefits of Glass-Lined Platens
One of the most significant benefits of glass-lined platens is their exceptional resistance to chemical corrosion. Unlike traditional metal platens, which can degrade over time when exposed to harsh chemicals, glass-lined surfaces maintain their integrity even in aggressive environments. This characteristic is particularly advantageous in industries where corrosive substances are commonplace, as it extends the lifespan of the equipment and reduces the need for frequent replacements.
Additionally, glass-lined platens offer superior thermal conductivity compared to many traditional materials. This property allows for more efficient heat transfer during processes such as pressing or molding, leading to improved energy efficiency and reduced operational costs. The ability to maintain consistent temperatures across the surface also contributes to uniform product quality, minimizing variations that can occur with less efficient materials.
As a result, manufacturers can achieve higher levels of precision in their operations, ultimately enhancing their competitive edge in the market.
When considering an upgrade to glass-lined platens, cost is often a primary concern for manufacturers. Initially, the investment in glass-lined technology may appear higher than that of traditional metal platens. However, a comprehensive cost analysis reveals that the long-term savings associated with reduced maintenance, lower replacement rates, and improved energy efficiency can offset the initial expenditure.
Moreover, the durability of glass-lined platens means that they are less likely to suffer from wear and tear over time. This longevity translates into fewer disruptions in production due to equipment failure or the need for repairs. In contrast, traditional platens may require more frequent replacements or extensive maintenance, leading to increased operational costs over time.
By evaluating both upfront costs and long-term savings, manufacturers can make a more informed decision regarding the financial implications of switching to glass-lined platens.
Durability and Longevity of Glass-Lined Platens
Durability is a critical factor in any manufacturing environment, and glass-lined platens excel in this regard. The glass coating provides a robust barrier against scratches, dents, and other forms of physical damage that can compromise the functionality of traditional platens. This resilience is particularly beneficial in high-volume production settings where equipment is subjected to constant use and potential abuse.
Furthermore, the longevity of glass-lined platens is enhanced by their resistance to thermal shock. Unlike metal surfaces that can warp or degrade under extreme temperature fluctuations, glass-lined surfaces maintain their structural integrity even when subjected to rapid changes in heat. This characteristic not only prolongs the life of the platen but also ensures consistent performance throughout its operational lifespan.
As manufacturers seek to optimize their processes and reduce downtime, investing in durable glass-lined platens becomes an increasingly attractive option.
Impact on Product Quality
The quality of finished products is paramount in any manufacturing process, and glass-lined platens play a crucial role in achieving high standards. The smooth surface of glass minimizes friction during production, reducing the likelihood of defects such as scratches or uneven finishes on the final product. This is particularly important in industries where aesthetics and precision are critical, such as automotive or consumer goods manufacturing.
Moreover, the uniform heat distribution provided by glass-lined platens contributes to consistent curing or molding processes. When temperatures are evenly maintained across the surface, manufacturers can achieve better control over product characteristics such as hardness, flexibility, and overall performance. This level of precision not only enhances product quality but also fosters customer satisfaction and loyalty, as consumers increasingly demand reliable and high-quality goods.
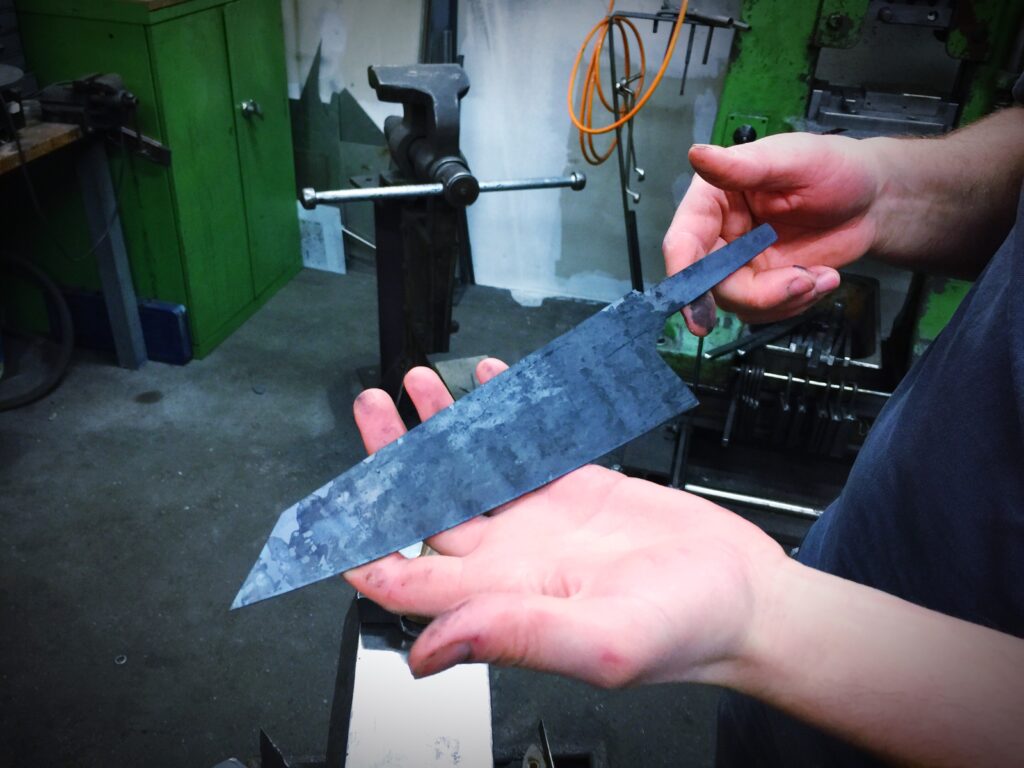
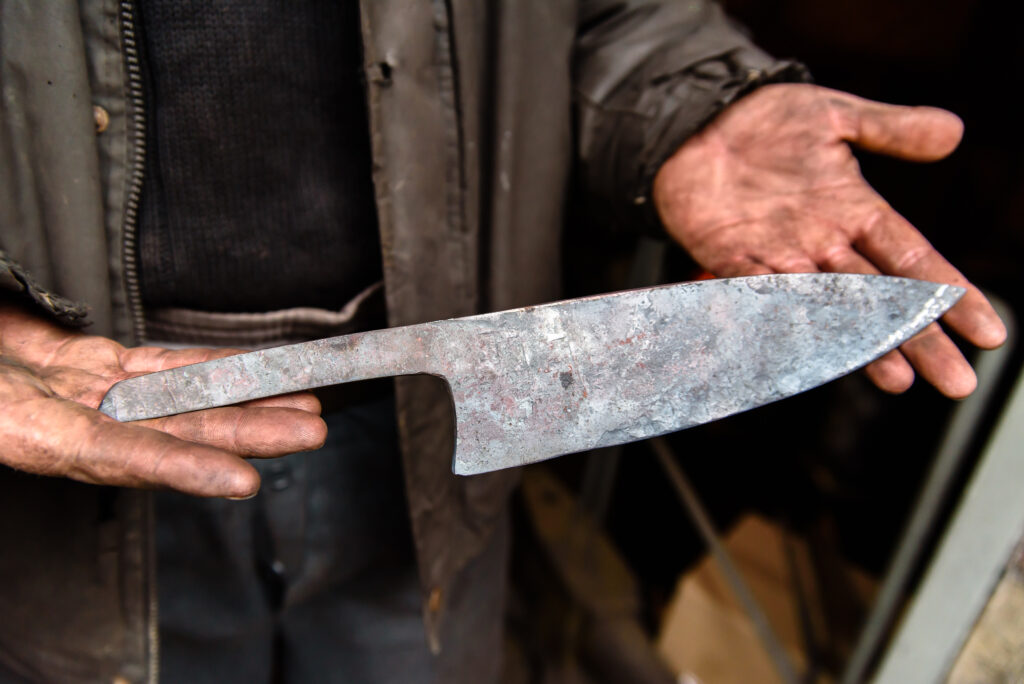
Environmental Considerations
In today’s environmentally conscious landscape, sustainability is a key consideration for manufacturers. Glass-lined platens offer several environmental benefits that align with modern sustainability goals. For instance, their durability reduces waste generated from frequent replacements of traditional platens, contributing to a lower overall environmental footprint.
Additionally, the energy efficiency associated with glass-lined technology can lead to reduced energy consumption during production processes. As manufacturers strive to minimize their carbon emissions and adhere to stricter environmental regulations, adopting glass-lined platens can be a proactive step toward achieving these objectives. By investing in sustainable technologies like glass-lined platens, companies not only enhance their operational efficiency but also position themselves as responsible stewards of the environment.
Maintenance and Cleaning of Glass-Lined Platens
One of the standout features of glass-lined platens is their ease of maintenance and cleaning. The non-porous surface prevents the accumulation of dirt, grime, and contaminants that can compromise product quality. This characteristic simplifies cleaning procedures, allowing manufacturers to maintain high hygiene standards with minimal effort.
Regular maintenance routines for glass-lined platens typically involve simple cleaning agents that do not require harsh chemicals or abrasive scrubbing tools. This not only saves time but also reduces the risk of damaging the surface during cleaning processes. As industries increasingly prioritize cleanliness—especially in sectors like food processing and pharmaceuticals—the ease of maintaining glass-lined platens becomes a significant advantage.
Safety Considerations
Safety is a paramount concern in any manufacturing environment, and glass-lined platens contribute positively to workplace safety standards. The smooth surface reduces the risk of accidents related to sharp edges or protruding components often found in traditional metal platens. Additionally, the non-reactive nature of glass minimizes hazards associated with chemical spills or reactions that could occur with metal surfaces.
Furthermore, glass-lined platens are less likely to harbor bacteria or other pathogens due to their non-porous nature. This characteristic is particularly crucial in industries where hygiene is critical, as it helps ensure compliance with health regulations and standards. By prioritizing safety through the use of glass-lined technology, manufacturers can create a safer working environment for their employees while also protecting their products from contamination.
Potential Drawbacks of Glass-Lined Platens
Despite their numerous advantages, glass-lined platens are not without potential drawbacks. One notable concern is their susceptibility to chipping or cracking if subjected to excessive force or impact. While they are generally durable under normal operating conditions, care must be taken during handling and installation to prevent damage that could compromise their effectiveness.
Additionally, the initial cost associated with purchasing glass-lined platens may deter some manufacturers from making the switch from traditional materials. While long-term savings can offset this investment, companies with tight budgets may find it challenging to justify the upfront expense without a clear understanding of the potential return on investment. As with any significant equipment upgrade, careful consideration must be given to both the benefits and limitations before making a decision.
Case Studies and Customer Testimonials
While specific case studies and customer testimonials cannot be included here, it is worth noting that many manufacturers have reported positive outcomes after transitioning to glass-lined platens. Industries ranging from food processing to pharmaceuticals have experienced enhanced product quality and operational efficiency as a result of adopting this technology. Feedback from users often highlights improvements in cleaning processes and reduced downtime due to equipment failures.
These anecdotal experiences underscore the practical benefits that come with investing in glass-lined technology and serve as valuable insights for manufacturers considering similar upgrades.
Is Upgrading to a Glass-Lined Platen Worth the Cost?
In conclusion, upgrading to glass-lined platens presents a compelling opportunity for manufacturers seeking to enhance their operational efficiency and product quality. While the initial investment may be higher than that of traditional metal platens, the long-term benefits—including durability, ease of maintenance, and improved safety—can justify the cost over time. As industries continue to prioritize sustainability and quality assurance, glass-lined platens stand out as a forward-thinking solution that aligns with these goals.
By carefully weighing the advantages against potential drawbacks and considering individual operational needs, manufacturers can make informed decisions about whether upgrading to glass-lined technology is indeed worth the investment for their specific applications.
FAQs
What is a glass-lined platen?
A glass-lined platen is a type of platen used in industrial equipment, such as heat exchangers and reactors, that is coated with a layer of glass to protect the metal surface from corrosion and chemical reactions.
What are the benefits of upgrading to a glass-lined platen?
Upgrading to a glass-lined platen can provide several benefits, including improved corrosion resistance, increased durability, and better protection against chemical reactions. It can also extend the lifespan of the equipment and reduce maintenance costs.
Is upgrading to a glass-lined platen worth the cost?
The decision to upgrade to a glass-lined platen depends on various factors, including the specific application, the level of corrosion and chemical exposure, and the long-term cost savings from reduced maintenance and replacement. It is important to weigh the upfront cost against the potential benefits and long-term savings.
What industries commonly use glass-lined platens?
Glass-lined platens are commonly used in industries such as chemical processing, pharmaceuticals, food and beverage, and petrochemicals, where equipment is exposed to corrosive chemicals and high temperatures.
How does a glass-lined platen compare to other types of platens?
Compared to other types of platens, such as stainless steel or carbon steel, glass-lined platens offer superior corrosion resistance, longer lifespan, and better protection against chemical reactions. However, they may have higher upfront costs and require specialized maintenance.