Vibration reduction is a critical aspect of modern engineering and manufacturing, particularly in industries where precision and performance are paramount. Excessive vibration can lead to a myriad of issues, including decreased product quality, increased wear and tear on machinery, and even safety hazards. As technology advances, the need for effective vibration control solutions has become more pressing.
One innovative approach that has gained traction is the use of aluminum components, particularly in the context of machinery like the TorusCNC 2×72 Grinders. These grinders are designed to deliver exceptional performance while minimizing the adverse effects of vibration. The significance of vibration reduction extends beyond mere comfort; it plays a vital role in enhancing the longevity and reliability of equipment.
In high-performance applications, such as metalworking and woodworking, the ability to maintain stability during operation can significantly impact the end product’s quality. By integrating aluminum components into machinery, manufacturers can harness the material’s unique properties to create systems that not only perform better but also last longer. This article will explore the benefits of aluminum components in vibration reduction, how they function, their applications, and considerations for implementation.
Key Takeaways
- Vibration reduction is crucial for improving the performance and longevity of mechanical systems.
- Aluminum components offer benefits such as lightweight, high strength, and excellent vibration damping properties.
- Aluminum components reduce vibration by absorbing and dissipating energy through their material properties.
- Smooth Grind Technology can be applied to various applications such as automotive, aerospace, and industrial machinery.
- Compared to other vibration reduction methods, aluminum components offer a combination of lightweight, strength, and vibration damping properties.
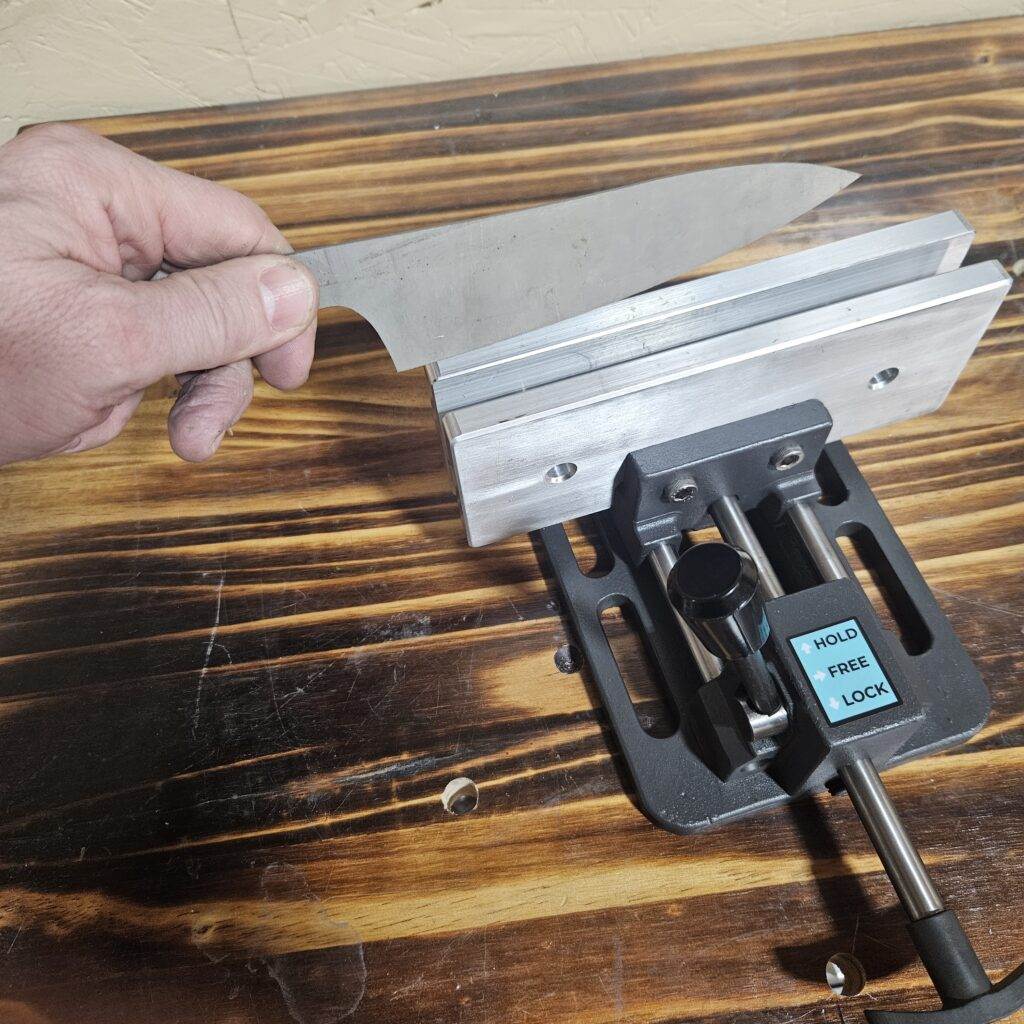
Benefits of Aluminum Components
Aluminum is a lightweight yet robust material that offers numerous advantages in various applications. One of its most notable benefits is its excellent strength-to-weight ratio, which allows for the construction of durable components without adding unnecessary weight to machinery. This characteristic is particularly advantageous in high-speed applications where excess weight can lead to increased inertia and, consequently, more pronounced vibrations.
By utilizing aluminum components, manufacturers can create machines that are not only easier to handle but also more efficient in their operation. In addition to its lightweight nature, aluminum possesses inherent damping properties that contribute to vibration reduction. The material’s ability to absorb and dissipate energy makes it an ideal choice for components that are subject to dynamic loads.
This energy absorption helps to minimize the transmission of vibrations throughout the machine, leading to smoother operation and improved performance. Furthermore, aluminum is resistant to corrosion, which enhances the longevity of components and reduces maintenance requirements. These benefits make aluminum an attractive option for manufacturers looking to improve their machinery’s performance while ensuring durability and reliability.
How Aluminum Components Reduce Vibration
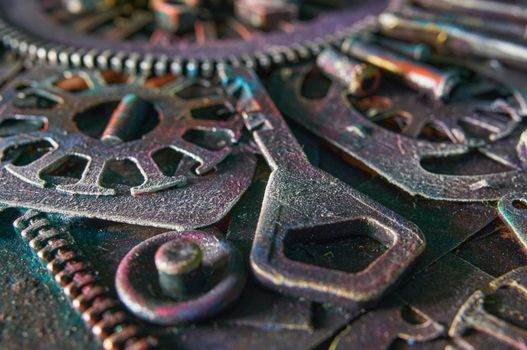
The mechanism by which aluminum components reduce vibration is multifaceted. First and foremost, aluminum’s lightweight nature allows for a more responsive design in machinery. When components are lighter, they can be engineered to move more freely and with less resistance, which helps to mitigate the effects of vibration during operation.
This responsiveness is particularly crucial in high-speed applications where rapid changes in direction or speed can exacerbate vibrational issues. Moreover, aluminum’s damping characteristics play a significant role in vibration reduction. When vibrations occur, they generate energy that can propagate through materials.
Aluminum’s ability to absorb this energy means that less of it is transmitted through the machine, resulting in a quieter and more stable operation. This energy dissipation is particularly beneficial in applications like the TorusCNC 2×72 Grinders, where precision is essential for achieving high-quality finishes on workpieces. By incorporating aluminum components into these grinders, manufacturers can enhance their performance while reducing the negative impacts of vibration.
Applications of Smooth Grind Technology
Application | Smooth Grind Technology Benefits |
---|---|
Automotive Industry | Improved surface finish for engine components |
Aerospace Industry | Enhanced precision for aircraft parts |
Medical Devices | High-quality finish for surgical instruments |
Tool and Die Making | Increased tool life and performance |
Smooth grind technology is an innovative approach that leverages advanced materials and engineering techniques to achieve superior grinding results. In the context of machines like the TorusCNC 2×72 Grinders, smooth grind technology focuses on minimizing vibrations during the grinding process. This technology is particularly beneficial in industries such as metalworking, woodworking, and tool manufacturing, where precision and surface finish are critical.
The application of smooth grind technology extends beyond just improving surface finishes; it also enhances overall productivity. By reducing vibrations, machines can operate at higher speeds without compromising quality. This increased efficiency translates into shorter production times and lower operational costs.
Additionally, smooth grind technology can lead to less wear on grinding belts and other consumables, further contributing to cost savings over time. As industries continue to seek ways to optimize their processes, the adoption of smooth grind technology will likely become increasingly prevalent.
Comparison with Other Vibration Reduction Methods
While aluminum components offer significant advantages for vibration reduction, it is essential to consider them within the broader context of available methods. Traditional approaches to vibration control often involve the use of rubber mounts or isolators designed to absorb shock and dampen vibrations. While these methods can be effective, they may not provide the same level of performance as aluminum components when integrated into machinery.
Aluminum’s unique properties allow for a more holistic approach to vibration reduction. Instead of merely isolating vibrations, aluminum components actively contribute to minimizing their generation through lightweight design and energy absorption capabilities. This proactive approach can lead to more significant improvements in machine performance compared to passive methods like rubber isolators.
As industries continue to evolve and demand higher precision and efficiency, the integration of aluminum components into machinery will likely become a preferred solution for vibration reduction.
Case Studies of Successful Implementation
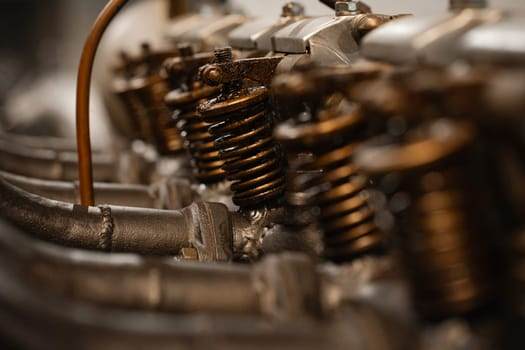
Several case studies illustrate the successful implementation of aluminum components in reducing vibration within various industries. One notable example involves a manufacturer of precision tools that integrated aluminum components into their grinding machines. By replacing heavier steel parts with aluminum alternatives, they observed a marked decrease in vibrations during operation.
This change not only improved the quality of their finished products but also extended the lifespan of their machinery. Another case study highlights a woodworking company that adopted aluminum components in their CNC routers. The transition resulted in smoother operation and reduced noise levels during cutting processes.
Operators reported less fatigue due to decreased vibrations transmitted through the machine frame, leading to improved overall productivity. These examples underscore the tangible benefits that aluminum components can bring to various applications, reinforcing their value as a solution for vibration reduction.
Considerations for Implementing Aluminum Components
While the advantages of aluminum components are clear, several considerations must be taken into account when implementing them into machinery. First and foremost is the cost factor; while aluminum may offer long-term savings through reduced maintenance and improved efficiency, the initial investment can be higher than traditional materials like steel. Manufacturers must weigh these costs against potential benefits to determine if aluminum is the right choice for their specific applications.
Additionally, engineers must consider the design implications when integrating aluminum components into existing machinery. The unique properties of aluminum may require adjustments in design parameters or manufacturing processes to ensure optimal performance. Collaboration between design engineers and manufacturing teams is crucial to successfully implement these changes while maintaining product quality and performance standards.
The Future of Vibration Reduction Technology
As industries continue to evolve and demand higher levels of precision and efficiency, the future of vibration reduction technology looks promising with innovations like aluminum components at the forefront. The unique properties of aluminum—its lightweight nature, strength-to-weight ratio, and damping capabilities—position it as an ideal material for enhancing machine performance while minimizing vibrations. The integration of technologies such as smooth grind technology within machines like the TorusCNC 2×72 Grinders exemplifies how manufacturers can leverage advanced materials for superior results.
As more companies recognize the benefits of incorporating aluminum components into their machinery, we can expect a shift towards more efficient and reliable manufacturing processes across various sectors. In conclusion, as we look ahead, it is clear that vibration reduction technology will continue to evolve alongside advancements in materials science and engineering practices. The adoption of aluminum components represents just one facet of this ongoing development, promising a future where precision manufacturing becomes increasingly attainable through innovative solutions.
FAQs
What are the benefits of using aluminum components to reduce vibration in grinding processes?
Aluminum components are known for their lightweight and high strength-to-weight ratio, which can help reduce the overall weight of the grinding equipment and minimize vibration. This can result in a quieter and smoother grinding process, leading to improved precision and efficiency.
How do aluminum components contribute to reducing vibration in grinding equipment?
Aluminum components have natural damping properties that can help absorb and dissipate vibration energy, resulting in a reduction of vibration levels in the grinding equipment. This can lead to a more stable and consistent grinding operation.
Are there any other advantages of using aluminum components in grinding equipment?
In addition to reducing vibration, aluminum components offer other benefits such as corrosion resistance, high thermal conductivity, and ease of machining. These properties can contribute to the overall performance and longevity of the grinding equipment.
Can aluminum components be used in various types of grinding equipment?
Yes, aluminum components can be utilized in a wide range of grinding equipment, including surface grinders, cylindrical grinders, centerless grinders, and more. Their versatility and compatibility make them a suitable choice for different grinding applications.
Are there any limitations or considerations when using aluminum components in grinding equipment?
While aluminum components offer many advantages, it is important to consider factors such as material compatibility, load-bearing requirements, and potential wear and tear. Proper engineering and design considerations are essential to ensure the optimal performance of aluminum components in grinding equipment.