In the ever-evolving landscape of manufacturing, the quest for efficiency and precision has become paramount. Streamlining assembly processes is not merely a goal; it is a necessity for companies aiming to remain competitive in a global market. The integration of advanced technologies, particularly Computer Numerical Control (CNC) machining, has revolutionized how components are produced and assembled.
By utilizing CNC aluminum components, manufacturers can significantly enhance their assembly operations, leading to reduced lead times, improved product quality, and lower production costs. The importance of streamlining assembly cannot be overstated. As consumer demands grow and industries become more complex, the need for faster and more reliable production methods has surged.
Companies are increasingly turning to CNC machining as a solution to these challenges. The precision and repeatability offered by CNC machines allow for the creation of intricate aluminum components that fit together seamlessly, minimizing the time spent on assembly and reducing the likelihood of errors. This article will explore the myriad benefits of using CNC aluminum components, delve into the machining process itself, and provide insights into designing for efficiency, all while highlighting the transformative impact of these technologies on assembly processes.
Key Takeaways
- Streamlining assembly processes can lead to increased efficiency and cost savings for manufacturers.
- Using CNC aluminum components can significantly reduce setup time and improve overall production speed.
- Understanding the CNC machining process is crucial for designing and implementing efficient aluminum components.
- Designing CNC aluminum components with efficiency in mind can further optimize assembly processes.
- Successful case studies demonstrate the benefits of using CNC aluminum components for streamlining assembly.
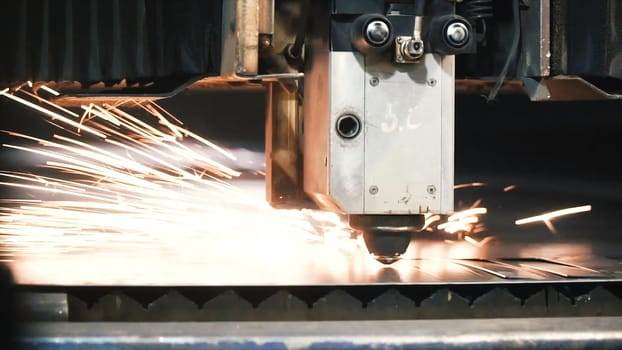
Benefits of Using CNC Aluminum Components for Faster Setup
One of the most significant advantages of utilizing CNC aluminum components is the speed at which they can be produced and assembled. CNC machining allows for rapid prototyping and production runs, enabling manufacturers to respond quickly to market demands. The ability to create complex geometries with high precision means that components can be manufactured to exact specifications, reducing the need for extensive adjustments during assembly.
This not only accelerates the setup process but also enhances overall productivity. Moreover, CNC aluminum components contribute to a reduction in material waste. Traditional manufacturing methods often result in excess scrap material due to inaccuracies in cutting and shaping.
In contrast, CNC machining optimizes material usage by employing advanced software that calculates the most efficient cutting paths. This efficiency not only lowers costs but also aligns with sustainability goals by minimizing waste. As companies increasingly prioritize environmentally friendly practices, the use of CNC aluminum components becomes an attractive option that supports both operational efficiency and corporate responsibility.
Understanding the CNC Machining Process
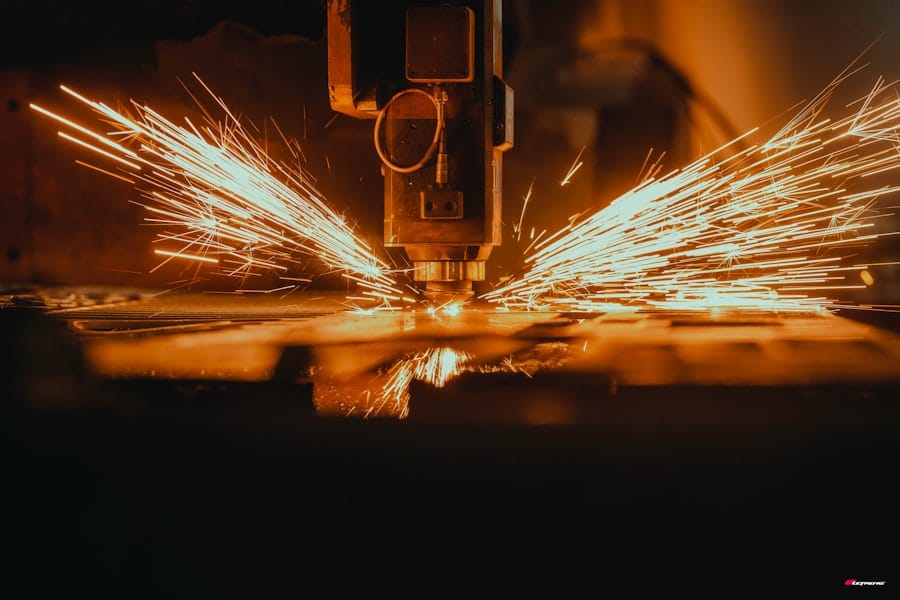
To fully appreciate the benefits of CNC aluminum components, it is essential to understand the CNC machining process itself. CNC machining involves the use of computer-controlled machines to remove material from a workpiece, creating precise shapes and features. The process begins with a digital design, typically created using Computer-Aided Design (CAD) software.
This design is then translated into a set of instructions that guide the CNC machine in executing the required cuts and operations. The versatility of CNC machining allows for various techniques, including milling, turning, and drilling, each suited for different applications. Aluminum is a popular choice for CNC machining due to its lightweight nature and excellent machinability.
The process can produce components with tight tolerances and smooth finishes, making them ideal for assembly in various industries, from aerospace to automotive. Understanding this process is crucial for manufacturers looking to leverage CNC technology effectively and maximize the potential of their aluminum components.
Tips for Designing CNC Aluminum Components for Efficiency
Tip | Description |
---|---|
Use proper tooling | Choose the right cutting tools and tool paths for efficient aluminum machining. |
Optimize cutting parameters | Adjust spindle speed, feed rate, and depth of cut for maximum efficiency. |
Minimize tool changes | Reduce downtime by using tools that can perform multiple operations. |
Implement cooling strategies | Use coolant and air blast systems to improve chip evacuation and extend tool life. |
Design for manufacturability | Consider machinability when designing part geometries and features. |
Designing CNC aluminum components with efficiency in mind requires careful consideration of several factors. First and foremost, simplicity is key. Components should be designed with minimal complexity to facilitate easier machining and assembly.
This means avoiding intricate features that may complicate the manufacturing process or require additional tooling. By focusing on straightforward designs, manufacturers can reduce production time and costs while maintaining quality. Another important aspect is the consideration of tolerances and fits.
When designing components for assembly, it is vital to ensure that parts fit together correctly without excessive play or tightness. This can be achieved by specifying appropriate tolerances during the design phase. Additionally, incorporating features such as alignment pins or dowels can aid in achieving precise assembly without requiring extensive adjustments.
By prioritizing these design elements, manufacturers can streamline their assembly processes and enhance overall efficiency.
Maximizing Efficiency in Assembly Processes with CNC Aluminum Components
Maximizing efficiency in assembly processes involves more than just producing high-quality components; it requires a holistic approach that encompasses workflow optimization and effective resource management. One effective strategy is to implement modular assembly techniques that leverage the strengths of CNC aluminum components. By designing components that can be easily combined or interchanged, manufacturers can simplify assembly tasks and reduce the time spent on each unit.
Furthermore, investing in training for assembly personnel can significantly impact efficiency. Workers who are well-versed in handling CNC aluminum components will be better equipped to assemble products quickly and accurately. Providing ongoing education about best practices in assembly techniques can lead to improved productivity and reduced error rates.
By fostering a culture of continuous improvement within the workforce, companies can ensure that their assembly processes remain efficient and responsive to changing demands.
Case Studies: Successful Implementation of CNC Aluminum Components
Numerous companies have successfully implemented CNC aluminum components into their assembly processes, reaping significant benefits in terms of efficiency and productivity. For instance, a leading aerospace manufacturer adopted CNC machining for its aircraft component production. By transitioning from traditional manufacturing methods to CNC technology, the company was able to reduce lead times by 30%, allowing them to meet tight project deadlines without compromising quality.
Another case study involves an automotive parts supplier that integrated CNC aluminum components into its production line. The supplier reported a 25% reduction in assembly time due to the precision and consistency of the machined parts. Additionally, the use of modular designs allowed for easier reconfiguration of assembly lines based on changing product demands.
These examples illustrate how embracing CNC technology can lead to tangible improvements in assembly efficiency across various industries.
Overcoming Challenges in Implementing CNC Aluminum Components
While the benefits of using CNC aluminum components are clear, challenges may arise during implementation. One common hurdle is the initial investment required for CNC machinery and software. Although these costs can be substantial, they should be viewed as long-term investments that will yield significant returns through increased efficiency and reduced operational costs over time.
Another challenge lies in ensuring that personnel are adequately trained to operate CNC machines and understand the intricacies of working with aluminum materials. Companies must prioritize training programs that equip employees with the necessary skills to maximize the potential of CNC technology. By addressing these challenges head-on, manufacturers can successfully integrate CNC aluminum components into their operations and unlock new levels of efficiency.
Future Trends in Streamlining Assembly with CNC Aluminum Components
As technology continues to advance, the future of streamlining assembly processes with CNC aluminum components looks promising. One emerging trend is the integration of automation and robotics into CNC machining operations. Automated systems can enhance production speed while maintaining high levels of precision, further reducing lead times in assembly processes.
Additionally, advancements in materials science may lead to new aluminum alloys specifically designed for improved machinability and performance in various applications. These innovations will enable manufacturers to push the boundaries of what is possible with CNC machining, resulting in even more efficient assembly processes. In conclusion, streamlining assembly through the use of CNC aluminum components presents a wealth of opportunities for manufacturers seeking to enhance their operations.
By understanding the benefits of CNC technology, optimizing design processes, and addressing implementation challenges, companies can position themselves for success in an increasingly competitive landscape. As trends continue to evolve, those who embrace these advancements will undoubtedly lead the way in efficient manufacturing practices.
FAQs
What are CNC aluminum components?
CNC aluminum components are parts or pieces made from aluminum using a computer numerical control (CNC) machine. This process involves cutting and shaping the aluminum material to create precise and accurate components.
How do CNC aluminum components reduce assembly time?
CNC aluminum components are manufactured with high precision, which ensures that they fit together perfectly during assembly. This reduces the need for adjustments or modifications, ultimately saving time during the assembly process.
What are the benefits of using CNC aluminum components in manufacturing?
Some benefits of using CNC aluminum components in manufacturing include faster setup times, improved product quality, reduced material waste, and increased production efficiency. Additionally, CNC machining allows for complex and intricate designs to be achieved with high accuracy.
What industries can benefit from using CNC aluminum components?
Industries such as aerospace, automotive, electronics, medical devices, and industrial equipment can benefit from using CNC aluminum components due to their high precision, durability, and lightweight properties.
How does precision fit contribute to overall product quality?
Precision fit ensures that components fit together seamlessly, reducing the risk of errors or malfunctions in the final product. This contributes to overall product quality by enhancing performance, reliability, and longevity.