In the realm of manufacturing and fabrication, the significance of perfectly square angles cannot be overstated. Square angles serve as the foundation for a multitude of processes, ensuring that components fit together seamlessly and function as intended. Whether in woodworking, metalworking, or any other form of construction, achieving precise angles is crucial for structural integrity and aesthetic appeal.
A slight deviation from a perfect square can lead to misalignments, which may compromise the overall quality of the final product. This is particularly important in industries where safety and durability are paramount, such as aerospace and automotive manufacturing. Moreover, perfectly square angles contribute to the efficiency of production processes.
When components are manufactured with exact angles, assembly becomes more straightforward, reducing the time and effort required to fit parts together. This not only streamlines operations but also minimizes waste, as fewer adjustments and corrections are needed. In an era where precision is increasingly demanded, understanding the importance of square angles is essential for any manufacturer aiming to maintain high standards and meet customer expectations.
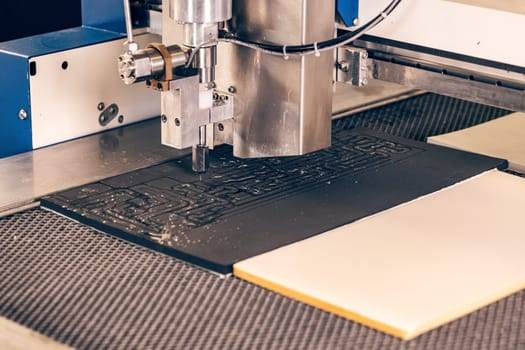
Key Takeaways
- Perfectly square angles are crucial for ensuring structural integrity and precision in various industries such as construction and manufacturing.
- CNC technology allows for precise angle measurements, resulting in accurate and consistent square angles for a wide range of applications.
- Utilizing CNC technology enables the achievement of plumb surfaces, ensuring that structures are level and stable.
- The benefits of using CNC for ensuring perfectly square angles include improved accuracy, efficiency, and consistency in production processes.
- Common challenges in achieving square angles can be overcome with CNC technology, which offers solutions for maintaining precision in angle and surface measurements.
Utilizing CNC Technology for Precise Angle Measurements
Computer Numerical Control (CNC) technology has revolutionized the way manufacturers approach precision in their work. By integrating advanced software and machinery, CNC systems can measure and produce angles with remarkable accuracy. The ability to program specific dimensions into a CNC machine allows for consistent results that are repeatable across multiple production runs.
This level of precision is particularly beneficial when working with materials that require exact specifications, as even minor discrepancies can lead to significant issues down the line. CNC technology also enhances the measurement process itself. Traditional methods of measuring angles often rely on manual tools that can introduce human error.
In contrast, CNC machines utilize digital readouts and automated systems to ensure that every angle is measured accurately. This not only increases reliability but also allows for real-time adjustments during the manufacturing process. As a result, manufacturers can achieve a level of precision that was previously unattainable, making CNC an invaluable tool in the quest for perfectly square angles.
Techniques for Achieving Plumb Surfaces with CNC Advantage
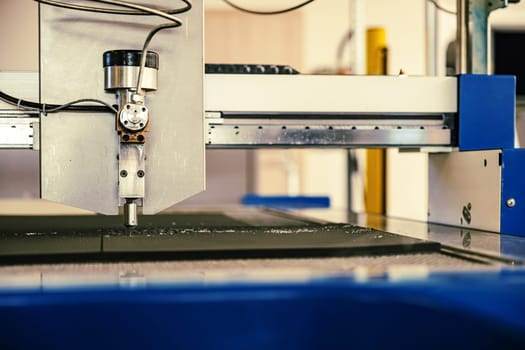
Achieving plumb surfaces is another critical aspect of precision manufacturing that can be greatly enhanced through CNC technology. A plumb surface refers to a vertical alignment that is perpendicular to a horizontal plane, which is essential for ensuring that structures are stable and aesthetically pleasing. CNC machines can be programmed to create plumb surfaces with exact specifications, eliminating the guesswork often associated with manual methods.
One effective technique for achieving plumb surfaces using CNC is through the use of specialized tooling and fixtures. By designing custom jigs that hold materials in place during machining, manufacturers can ensure that surfaces remain stable and aligned throughout the process. Additionally, CNC machines can be equipped with sensors that detect deviations from plumb, allowing for immediate corrections to be made.
This proactive approach not only enhances accuracy but also reduces the likelihood of errors that could compromise the integrity of the final product.
Benefits of Using CNC for Ensuring Perfectly Square Angles
Benefits of Using CNC for Ensuring Perfectly Square Angles |
---|
1. Precision: CNC machines can accurately cut and shape materials to ensure perfectly square angles with high precision. |
2. Consistency: CNC technology allows for consistent and repeatable results, ensuring that all angles are perfectly square across multiple workpieces. |
3. Time-saving: Using CNC for ensuring square angles can save time compared to manual methods, as the process can be automated and completed more efficiently. |
4. Versatility: CNC machines can work with a variety of materials, making it suitable for a wide range of applications that require perfectly square angles. |
5. Reduced waste: CNC technology minimizes material waste by accurately cutting and shaping materials to achieve perfectly square angles, reducing the need for rework. |
The benefits of utilizing CNC technology for achieving perfectly square angles extend beyond mere accuracy. One of the most significant advantages is the increased efficiency it brings to production processes. With CNC machines capable of executing complex cuts and measurements at high speeds, manufacturers can produce components faster than ever before.
This efficiency translates into shorter lead times and the ability to meet tight deadlines without sacrificing quality. Furthermore, CNC technology reduces material waste by optimizing cutting paths and minimizing errors. When angles are measured and cut with precision, there is less likelihood of needing to scrap materials due to mistakes or misalignments.
This not only saves costs but also contributes to more sustainable manufacturing practices. As industries increasingly focus on reducing their environmental impact, the ability to produce perfectly square angles with minimal waste becomes a significant advantage.
Common Challenges in Achieving Square Angles and How CNC Can Help
Despite the advancements in technology, achieving perfectly square angles still presents challenges for many manufacturers. One common issue is the variability in material properties, which can affect how materials respond to cutting processes. For instance, different types of wood or metal may expand or contract based on environmental conditions, leading to potential misalignments during production.
CNC technology addresses these challenges by providing a level of adaptability that traditional methods lack. With programmable settings, manufacturers can adjust cutting parameters based on the specific characteristics of the material being used. Additionally, CNC machines can incorporate feedback mechanisms that monitor performance in real-time, allowing for immediate adjustments if deviations occur.
This capability not only enhances precision but also empowers manufacturers to tackle challenges head-on, ensuring that square angles are consistently achieved.
Tips for Maintaining Precision in Angle and Surface Measurements with CNC
To fully leverage the capabilities of CNC technology in achieving precision in angle and surface measurements, manufacturers should adopt best practices that promote accuracy and consistency. One essential tip is regular calibration of CNC machines. Over time, wear and tear can affect a machine’s performance, leading to potential inaccuracies in measurements.
By implementing a routine calibration schedule, manufacturers can ensure that their equipment remains in optimal condition. Another important practice is thorough training for operators who work with CNC machines. Understanding how to program and operate these systems effectively is crucial for maintaining precision.
Operators should be well-versed in interpreting measurement data and making necessary adjustments during production. Additionally, utilizing high-quality tooling and fixtures can significantly enhance the accuracy of angle and surface measurements, further contributing to the overall quality of the final product.
How CNC Can Improve Efficiency and Accuracy in Square Angle and Plumb Surface Production
The integration of CNC technology into manufacturing processes has fundamentally transformed how efficiency and accuracy are achieved in producing square angles and plumb surfaces. By automating many aspects of production, CNC machines reduce the time required for setup and execution compared to traditional methods. This automation allows manufacturers to allocate resources more effectively, focusing on other critical areas of production while maintaining high standards of quality.
Moreover, CNC systems enable manufacturers to produce complex geometries with ease. The ability to program intricate designs into a machine means that even challenging shapes can be created with precision. This capability not only enhances creativity in design but also ensures that components fit together seamlessly during assembly.
As a result, manufacturers can achieve higher levels of productivity without compromising on accuracy or quality.
Case Studies: Successful Applications of CNC for Achieving Perfectly Square Angles and Plumb Surfaces
Numerous case studies illustrate the successful application of CNC technology in achieving perfectly square angles and plumb surfaces across various industries. For instance, a leading aerospace manufacturer implemented CNC machining to produce components with stringent tolerances required for aircraft assembly. By utilizing advanced CNC systems, they were able to achieve remarkable precision in their angle measurements, resulting in improved assembly times and enhanced safety standards.
In another example, a furniture manufacturer adopted CNC technology to streamline their production processes while ensuring high-quality finishes on their products. By programming their CNC machines to create perfectly square angles in tabletops and cabinets, they significantly reduced material waste and improved overall product quality. The integration of CNC not only enhanced their operational efficiency but also allowed them to meet growing customer demands for custom designs without sacrificing precision.
In conclusion, understanding the importance of perfectly square angles is fundamental for any manufacturer aiming for excellence in their products. The utilization of CNC technology has transformed how these angles are measured and produced, offering unparalleled precision and efficiency. By adopting best practices and leveraging advanced techniques, manufacturers can overcome common challenges associated with achieving square angles and plumb surfaces while reaping significant benefits in terms of quality and sustainability.
As industries continue to evolve, embracing CNC technology will remain essential for maintaining competitive advantages in an increasingly demanding market.
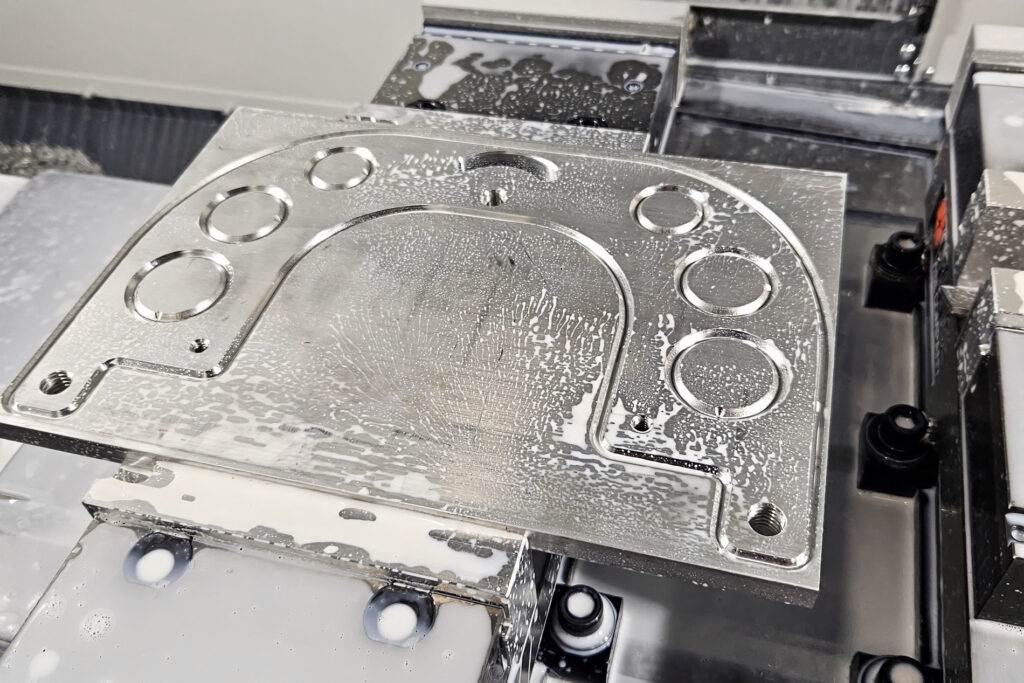
FAQs
What is CNC grinding?
CNC grinding is a manufacturing process that uses computer numerical control (CNC) to precisely remove material from a workpiece to create a desired shape or finish.
What are the advantages of CNC grinding?
CNC grinding offers the advantage of producing perfectly square angles and plumb surfaces, resulting in highly accurate and precise components. It also allows for greater consistency and repeatability in the manufacturing process.
How does CNC grinding achieve perfectly square angles and plumb surfaces?
CNC grinding machines are equipped with advanced technology and precision controls that allow for the accurate removal of material from the workpiece. This results in the creation of perfectly square angles and plumb surfaces.
What industries benefit from CNC grinding?
Industries such as aerospace, automotive, medical, and tool and die making benefit from CNC grinding due to the need for highly accurate and precise components in their manufacturing processes.
What types of materials can be CNC ground?
CNC grinding can be used on a wide range of materials, including metals, plastics, ceramics, and composites. This versatility makes it a valuable process for many different industries.