Stainless steel dust is a byproduct of various industrial processes, including cutting, grinding, and welding. This fine particulate matter can pose significant health risks to workers if not properly managed. The composition of stainless steel, which includes chromium, nickel, and other alloying elements, means that the dust generated can be toxic when inhaled.
Prolonged exposure to stainless steel dust can lead to respiratory issues, skin irritation, and other health complications. Understanding these hazards is crucial for any organization involved in stainless steel fabrication or machining. Moreover, the physical properties of stainless steel dust contribute to its potential dangers.
The particles are often very small, allowing them to remain airborne for extended periods and making them easy to inhale. This characteristic necessitates stringent control measures to minimize exposure. Additionally, the dust can accumulate in work areas, creating slip hazards and increasing the risk of fire or explosion in certain conditions.
Therefore, recognizing the hazards associated with stainless steel dust is the first step in developing effective safety protocols.
Key Takeaways
- Stainless steel dust can pose serious hazards including fire, explosion, and respiratory issues.
- Potential sources of stainless steel dust include grinding, cutting, welding, and handling of stainless steel materials.
- Risks associated with stainless steel dust include inhalation, skin contact, and ignition potential.
- Engineering controls such as ventilation and enclosure can help minimize stainless steel dust hazards.
- Administrative controls like training, signage, and work practices can also help mitigate stainless steel dust risks.
Identifying Potential Sources of Stainless Steel Dust
Identifying the sources of stainless steel dust within a facility is essential for implementing effective control measures. Common sources include machining operations such as grinding, cutting, and polishing, where metal is removed from the workpiece, generating fine particles. Welding processes also contribute significantly to dust generation, particularly when using certain types of filler materials that may contain additional alloying elements.
Each of these processes can produce varying amounts of dust depending on the techniques and equipment used. In addition to direct operations, secondary sources of stainless steel dust can arise from maintenance activities and the handling of raw materials. For instance, transporting stainless steel sheets or components can lead to the release of dust into the air.
Furthermore, inadequate housekeeping practices can exacerbate the problem by allowing dust to accumulate on surfaces and equipment. Identifying these potential sources is critical for developing a comprehensive approach to dust management that addresses all aspects of the operation.
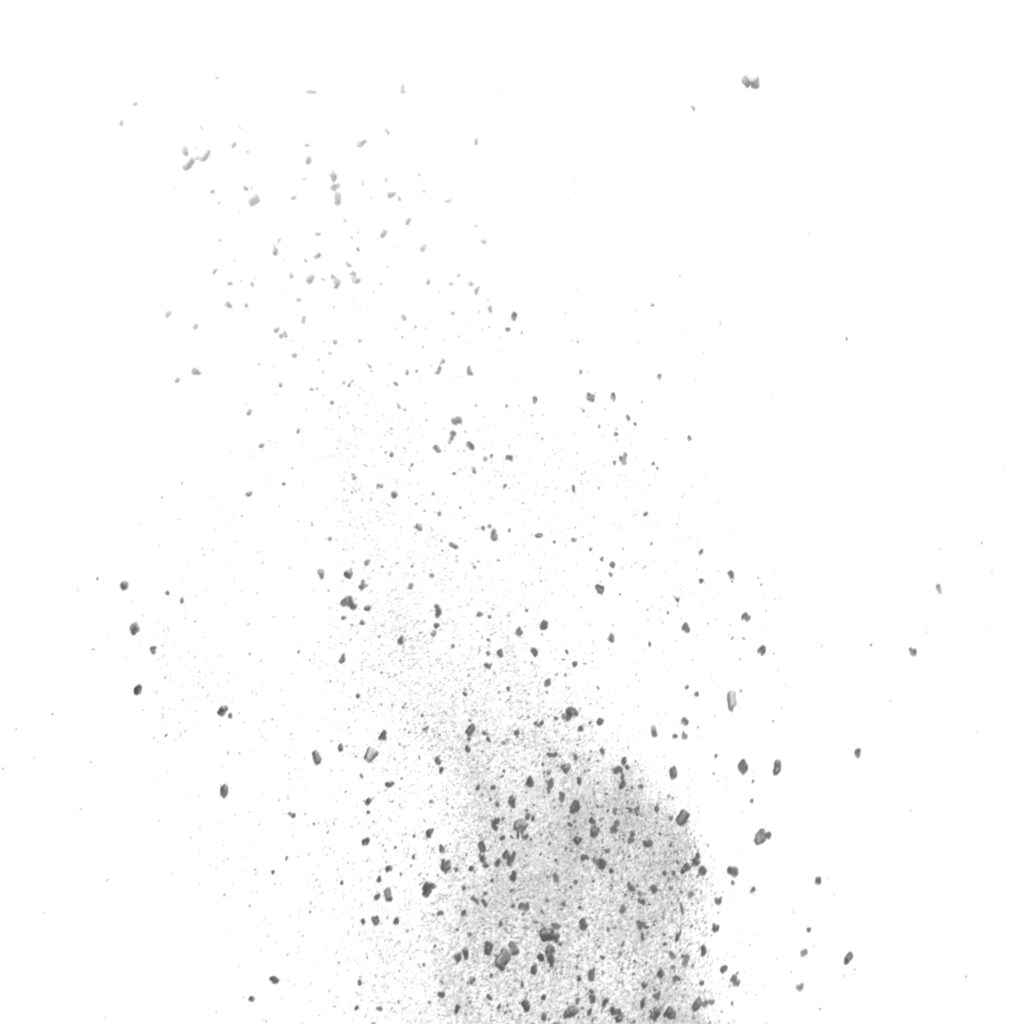
Assessing the Risks Associated with Stainless Steel Dust
Once potential sources of stainless steel dust have been identified, it is vital to assess the associated risks. This assessment involves evaluating the likelihood of exposure and the potential health effects on workers. Factors such as the duration and frequency of exposure, as well as individual susceptibility, play a significant role in determining risk levels.
For example, workers engaged in high-intensity grinding operations may face greater exposure compared to those performing less dusty tasks. Additionally, understanding the specific health effects linked to stainless steel dust is crucial for risk assessment. Chronic exposure can lead to conditions such as asthma, chronic obstructive pulmonary disease (COPD), and even lung cancer in severe cases.
The presence of nickel in some stainless steel alloys has also been associated with allergic reactions and dermatitis. By thoroughly assessing these risks, organizations can prioritize their efforts in implementing control measures that protect worker health and safety.
Implementing Engineering Controls for Stainless Steel Dust
Engineering controls are among the most effective strategies for managing stainless steel dust hazards. These controls involve modifying equipment or processes to reduce dust generation at the source or to capture it before it becomes airborne. For instance, using enclosed machining centers or wet cutting techniques can significantly minimize dust production during operations.
Additionally, local exhaust ventilation systems can be installed to capture airborne particles at their source, preventing them from dispersing throughout the work environment. Another effective engineering control is the use of air filtration systems that can remove fine particles from the air. High-efficiency particulate air (HEPA) filters are particularly effective in capturing small dust particles, ensuring cleaner air quality within the facility.
Regular maintenance and monitoring of these systems are essential to ensure their effectiveness over time. By investing in robust engineering controls, organizations can create a safer working environment while also enhancing productivity by reducing downtime associated with health-related issues.
Utilizing Administrative Controls for Stainless Steel Dust
In addition to engineering controls, administrative controls play a vital role in managing stainless steel dust hazards. These controls involve implementing policies and procedures that govern how work is conducted within the facility. For example, establishing work schedules that limit exposure time for employees can help reduce overall risk.
Rotating workers through different tasks can also minimize prolonged exposure to dusty environments. Training and awareness programs are another critical component of administrative controls. Employees should be educated about the hazards associated with stainless steel dust and the importance of following established safety protocols.
Clear communication regarding safe work practices and the proper use of equipment can significantly reduce the likelihood of accidents and health issues. By fostering a culture of safety through administrative controls, organizations can enhance their overall approach to dust management.
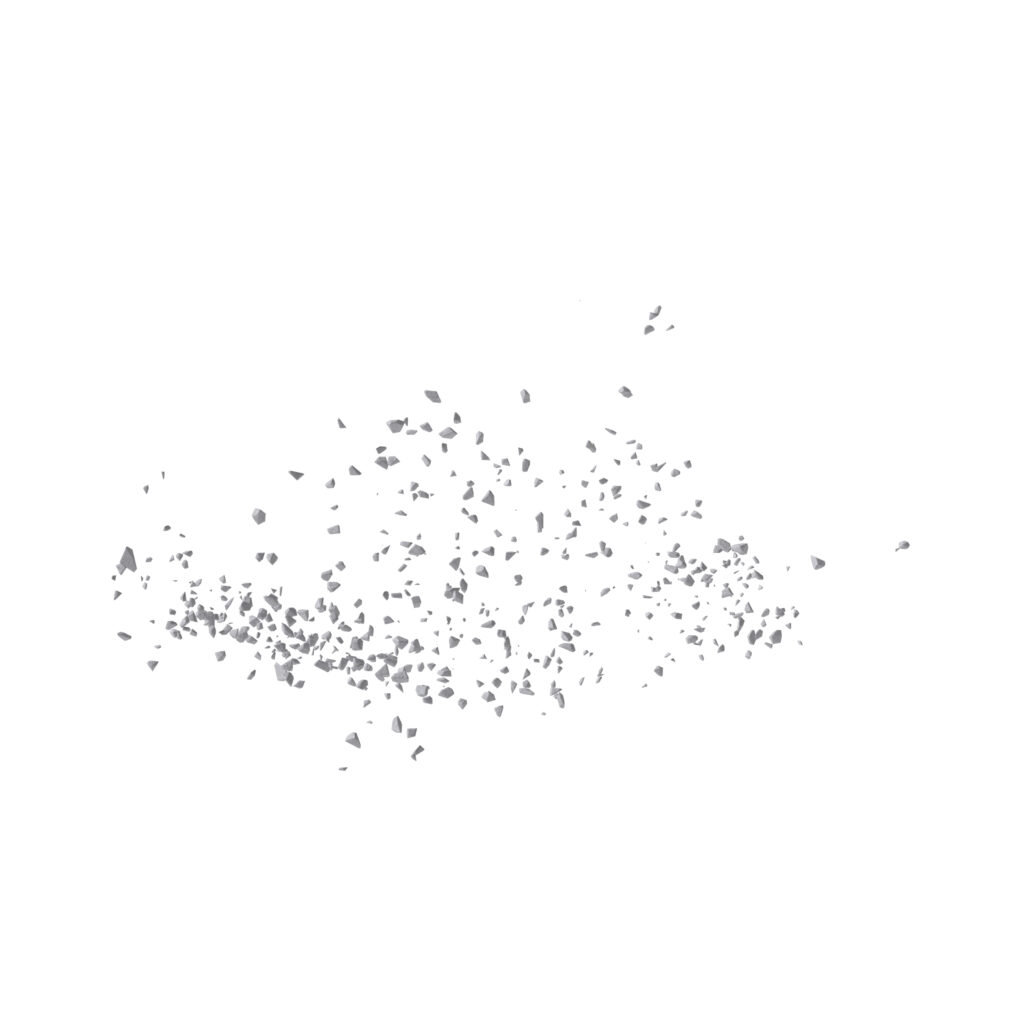
Selecting Personal Protective Equipment for Stainless Steel Dust
Personal protective equipment (PPE) is an essential line of defense against stainless steel dust exposure. Selecting appropriate PPE involves considering the specific tasks being performed and the level of exposure risk associated with those tasks. Respirators equipped with HEPA filters are often necessary for workers engaged in high-dust activities, ensuring that they do not inhale harmful particles.
Additionally, protective clothing such as coveralls can help prevent skin contact with dust. It is also important to ensure that PPE fits properly and is comfortable for employees to wear throughout their shifts. Regular training on the correct use and maintenance of PPE is crucial for maximizing its effectiveness.
Employees should be encouraged to report any issues with their equipment so that prompt replacements or repairs can be made. By prioritizing PPE selection and training, organizations can significantly reduce the risk of health complications related to stainless steel dust exposure.
Developing a Comprehensive Dust Management Plan
A comprehensive dust management plan is essential for effectively addressing stainless steel dust hazards within a facility. This plan should outline specific strategies for identifying sources of dust, assessing risks, implementing engineering and administrative controls, and selecting appropriate PPE. Additionally, it should include procedures for regular monitoring and evaluation of dust levels in the workplace.
The development of this plan should involve input from various stakeholders, including management, safety personnel, and employees who are directly involved in operations. By fostering collaboration, organizations can ensure that all perspectives are considered and that the plan is practical and effective. Regular reviews and updates to the dust management plan are also necessary to adapt to changes in operations or regulations, ensuring ongoing protection for workers.
Training Employees on Stainless Steel Dust Hazards and Control Strategies
Training employees on stainless steel dust hazards and control strategies is a critical component of any effective safety program. This training should cover the nature of stainless steel dust, its potential health effects, and the importance of adhering to safety protocols. Employees should also be educated on how to recognize potential hazards in their work environment and understand their role in maintaining a safe workplace.
Moreover, training should include practical demonstrations on the proper use of engineering controls, administrative procedures, and PPE. Engaging employees through hands-on training sessions can enhance retention and encourage active participation in safety initiatives. Regular refresher courses should be scheduled to keep safety information current and reinforce best practices among staff members.
Conducting Regular Inspections and Maintenance of Dust Control Measures
Regular inspections and maintenance of dust control measures are essential for ensuring their continued effectiveness in managing stainless steel dust hazards. Inspections should be conducted frequently to identify any issues with equipment such as ventilation systems or air filters that may hinder performance. Additionally, housekeeping practices should be evaluated to ensure that surfaces are kept clean and free from accumulated dust.
Maintenance schedules should be established for all dust control equipment to ensure timely repairs or replacements as needed. Keeping detailed records of inspections and maintenance activities can help organizations track performance over time and identify trends that may require further attention. By prioritizing regular inspections and maintenance, organizations can sustain a safer working environment for their employees.
Monitoring Air Quality to Ensure Effective Dust Control
Monitoring air quality is a crucial aspect of managing stainless steel dust hazards effectively. Regular air quality assessments can help organizations determine whether their control measures are working as intended or if adjustments are necessary. Various methods exist for monitoring airborne particulate levels, including real-time monitoring systems that provide immediate feedback on air quality conditions.
Data collected from air quality monitoring should be analyzed regularly to identify trends or spikes in dust levels that may indicate a need for enhanced control measures. This information can also inform decisions regarding employee exposure limits and help ensure compliance with regulatory standards. By actively monitoring air quality, organizations can take proactive steps to protect worker health while continuously improving their dust management strategies.
Continuously Improving Dust Control Strategies for Stainless Steel Operations
Continuous improvement is essential for maintaining effective dust control strategies in stainless steel operations. As technology advances and new methods emerge, organizations should remain open to adopting innovative solutions that enhance safety and efficiency. Regularly reviewing existing practices allows companies to identify areas for improvement and implement changes that reflect best practices in the industry.
Engaging employees in discussions about potential improvements can also foster a culture of safety and innovation within the organization. Employees often have valuable insights based on their experiences in the field that can lead to more effective dust management strategies. By committing to continuous improvement efforts, organizations not only enhance worker safety but also contribute to a more sustainable operational environment overall.
FAQs
What are the hazards of stainless steel dust?
Stainless steel dust can pose a fire and explosion hazard due to its fine particle size and potential for ignition. Inhaling stainless steel dust can also cause respiratory issues and irritation to the lungs.
How can stainless steel dust be controlled?
Stainless steel dust can be controlled through proper ventilation, dust collection systems, and the use of personal protective equipment such as respirators and protective clothing. Regular cleaning and maintenance of equipment and work areas can also help control the spread of stainless steel dust.
What industries are at risk for stainless steel dust hazards?
Industries that work with stainless steel, such as metal fabrication, welding, and machining, are at risk for stainless steel dust hazards. Additionally, industries that use stainless steel in powder form, such as in the production of metal powders or 3D printing, may also face hazards related to stainless steel dust.
What are the regulations and standards for controlling stainless steel dust hazards?
Regulations and standards for controlling stainless steel dust hazards may vary by region and industry. However, general workplace safety regulations and standards, such as those set by OSHA in the United States, provide guidelines for controlling hazardous dusts in the workplace. Employers are responsible for ensuring compliance with these regulations and standards to protect workers from stainless steel dust hazards.
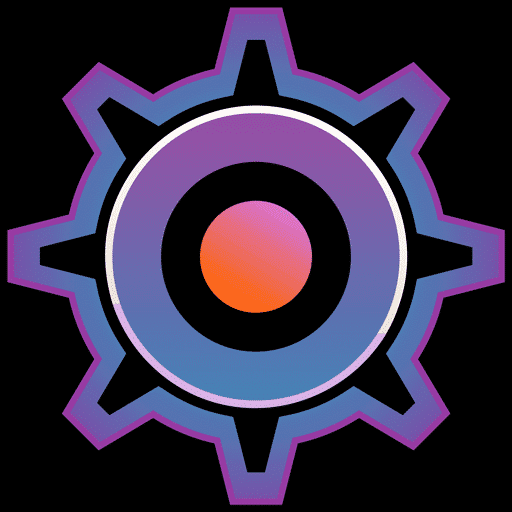