Belt tracking is a fundamental aspect of CNC machining that plays a crucial role in the overall performance and efficiency of the equipment. In essence, belt tracking refers to the alignment and positioning of the belt on the pulleys of a machine. Proper belt tracking ensures that the belt runs smoothly along its intended path without slipping or misaligning.
This is particularly important in CNC machines, where precision and accuracy are paramount. A well-tracked belt contributes to consistent machining results, reducing the likelihood of errors that could compromise the quality of the finished product. In the context of CNC machining, understanding belt tracking involves recognizing how various factors can influence the performance of the belt.
These factors include the tension applied to the belt, the condition of the pulleys, and the overall alignment of the machine components. For instance, if a belt is too loose or too tight, it can lead to uneven wear and tear, resulting in premature failure. Additionally, environmental conditions such as temperature and humidity can also affect belt performance.
Therefore, a comprehensive understanding of belt tracking is essential for operators and technicians to maintain optimal machine functionality.
Key Takeaways
- Proper belt tracking is essential for smooth and accurate CNC machining operations
- Common issues with belt tracking include misalignment, slippage, and excessive wear
- Achieving perfect belt tracking requires proper tensioning and regular maintenance
- Tensioning systems play a crucial role in ensuring optimal belt tracking in CNC machining
- Perfect belt tracking leads to improved accuracy, reduced downtime, and extended belt life in CNC machining operations
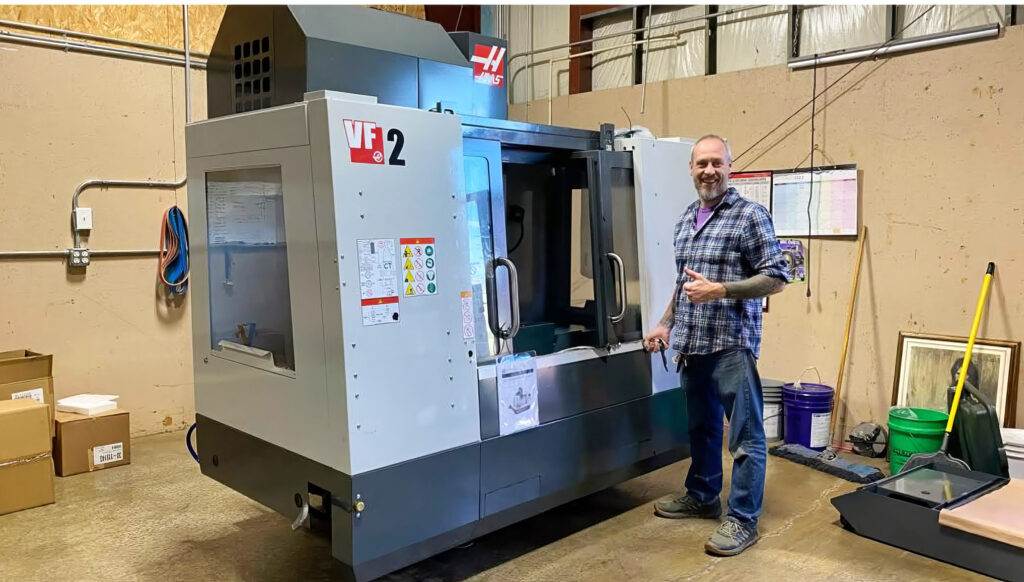
Common Issues with Belt Tracking
Despite its importance, several common issues can arise with belt tracking in CNC machining. One prevalent problem is belt slippage, which occurs when the belt fails to maintain contact with the pulleys. This can lead to a loss of power transmission, resulting in decreased machine performance and potential damage to both the belt and the machine itself.
Slippage can be caused by various factors, including improper tensioning, misalignment of pulleys, or wear and tear on the belt material. Another issue that often arises is uneven wear on the belt. This can manifest as fraying or cracking along the edges, which not only affects the longevity of the belt but can also compromise machining accuracy.
Uneven wear is typically a result of poor tracking, where the belt does not run parallel to the pulleys. This misalignment can lead to increased friction and heat generation, further exacerbating wear and potentially leading to catastrophic failure if not addressed promptly. Identifying these common issues early on is crucial for maintaining the integrity of CNC machines.
Importance of Proper Belt Tracking in CNC Machining
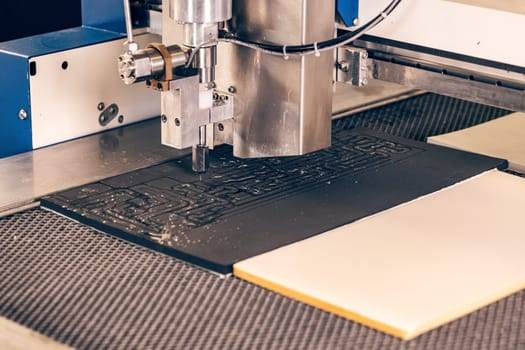
Proper belt tracking is vital for several reasons, primarily related to machine performance and product quality. When a belt is correctly tracked, it ensures that power is transmitted efficiently from the motor to the cutting tools or other components of the CNC machine. This efficiency translates into smoother operation, reduced energy consumption, and ultimately lower operational costs.
Additionally, proper tracking minimizes the risk of unexpected downtime due to mechanical failures, allowing for more consistent production schedules. Moreover, accurate belt tracking directly impacts the quality of the machined parts. In CNC machining, precision is key; even minor deviations can lead to significant discrepancies in dimensions and tolerances.
A well-tracked belt helps maintain consistent feed rates and cutting speeds, which are essential for achieving high-quality finishes on machined components. Therefore, investing time and resources into ensuring proper belt tracking is not just a maintenance task; it is a critical component of achieving excellence in CNC machining.
Techniques for Achieving Perfect Belt Tracking
Technique | Description |
---|---|
Proper Belt Tension | Ensuring the belt is properly tensioned to prevent slipping or misalignment. |
Alignment of Pulleys | Ensuring that all pulleys are properly aligned to prevent belt tracking issues. |
Regular Maintenance | Regularly inspecting and maintaining the belt and pulley system to prevent tracking problems. |
Use of Tracking Guides | Installing tracking guides to help keep the belt in the correct position. |
Achieving perfect belt tracking requires a combination of techniques and best practices that focus on alignment and tensioning. One effective method is to regularly check and adjust the alignment of pulleys. This involves ensuring that all pulleys are parallel to each other and that they are positioned correctly relative to the machine frame.
Misalignment can often be detected visually or through simple measurements using tools like calipers or laser alignment devices. By maintaining proper alignment, operators can significantly reduce the risk of tracking issues. Another technique involves monitoring and adjusting belt tension.
The correct tension is crucial for optimal performance; too much tension can lead to excessive wear on both the belt and pulleys, while too little tension can result in slippage. Operators should refer to manufacturer specifications for recommended tension levels and use appropriate tools such as tension gauges to achieve accurate adjustments. Regularly checking tension as part of routine maintenance can help prevent tracking problems before they escalate.
Using Tensioning Systems for Belt Tracking
Tensioning systems play a pivotal role in maintaining proper belt tracking in CNC machines. These systems are designed to apply consistent pressure to the belt, ensuring that it remains taut without being overly tight. There are various types of tensioning systems available, including manual and automatic options.
Manual tensioners require operators to make adjustments based on visual inspections or measurements, while automatic systems continuously monitor and adjust tension as needed. The use of automatic tensioning systems can significantly enhance operational efficiency by reducing the need for frequent manual adjustments. These systems often incorporate sensors that detect changes in tension and automatically compensate for them, ensuring optimal performance at all times.
By implementing a reliable tensioning system, CNC operators can minimize downtime associated with tracking issues and improve overall productivity.
Regular Maintenance and Inspection for Belt Tracking
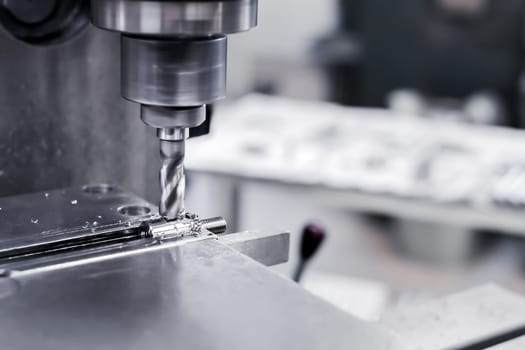
Effective Belt Tracking Management in CNC Machining
Regular maintenance and inspection are crucial components of effective belt tracking management in CNC machining. Establishing a routine maintenance schedule allows operators to proactively identify potential issues before they escalate into significant problems. Inspections should include checking for signs of wear on both the belt and pulleys, as well as verifying alignment and tension levels.
Preventative Maintenance for Extended Belt Lifespan
By addressing minor issues early on, operators can extend the lifespan of their belts and reduce the likelihood of unexpected breakdowns. This proactive approach not only saves time and resources but also minimizes downtime and increases overall productivity.
Advanced Diagnostic Techniques for Enhanced Maintenance
In addition to visual inspections, operators should also consider implementing more advanced diagnostic techniques such as vibration analysis or thermal imaging. These methods can provide valuable insights into the condition of belts and pulleys that may not be visible during standard inspections. By leveraging these technologies, operators can gain a deeper understanding of their equipment’s condition and make data-driven decisions.
Enhancing Maintenance Practices with Technology
By leveraging technology in maintenance practices, CNC operators can enhance their ability to detect early signs of tracking issues and take corrective action promptly. This integrated approach to maintenance enables operators to optimize their equipment’s performance, reduce downtime, and increase overall efficiency.
Troubleshooting and Correcting Belt Tracking Issues
When belt tracking issues arise, it is essential to have a systematic approach to troubleshooting and correction. The first step in this process is to identify the root cause of the problem. This may involve examining factors such as pulley alignment, tension levels, and overall machine condition.
Once the underlying issue has been identified, operators can take appropriate corrective actions. For instance, if misalignment is detected as the cause of tracking problems, adjustments should be made to realign pulleys accurately. If uneven wear is observed on the belt, it may be necessary to replace it entirely or adjust tension levels to prevent further damage.
Documenting these troubleshooting steps can also be beneficial for future reference, allowing operators to recognize patterns in recurring issues and develop more effective preventive measures.
Benefits of Perfect Belt Tracking in CNC Machining
The benefits of achieving perfect belt tracking in CNC machining are manifold and significantly contribute to operational success. One of the most notable advantages is enhanced machine efficiency. When belts are properly tracked, they operate smoothly without unnecessary friction or slippage, leading to improved power transmission and reduced energy consumption.
This efficiency not only lowers operational costs but also extends the lifespan of both belts and machine components. Furthermore, perfect belt tracking directly correlates with improved product quality. Consistent feed rates and cutting speeds result in higher precision machining, which is essential for meeting stringent industry standards and customer expectations.
As a result, manufacturers can achieve greater customer satisfaction through reliable delivery of high-quality products. In summary, investing in proper belt tracking practices yields substantial returns in terms of efficiency, cost savings, and product quality within CNC machining operations like those offered by TorusCNC 2×72 Grinders.
FAQs
What is CNC machining?
CNC machining stands for Computer Numerical Control machining, which is a manufacturing process that uses pre-programmed computer software to control the movement of machinery and tools. This technology is used to create precise and complex parts from various materials such as metal, plastic, wood, and more.
How does CNC machining ensure consistent belt tracking?
CNC machining ensures consistent belt tracking by producing precise and accurate components for belt tracking systems. This technology allows for the creation of perfectly aligned and dimensionally accurate parts, which are essential for maintaining consistent belt tracking in industrial machinery and conveyor systems.
What are the benefits of using CNC machining for belt tracking systems?
Using CNC machining for belt tracking systems offers several benefits, including high precision, repeatability, and consistency in part production. This technology also allows for the creation of custom-designed components to meet specific belt tracking requirements, resulting in improved performance and reduced maintenance needs.
How does CNC machining contribute to engineering for perfection in belt tracking?
CNC machining contributes to engineering for perfection in belt tracking by ensuring that the components used in belt tracking systems are manufactured to the highest standards of accuracy and quality. This precision engineering plays a crucial role in achieving consistent and reliable belt tracking performance in industrial applications.